
4x Operator Training Completion Rates
How a leading agricultural manufacturer standardized operations across multiple plants and thousands of operators.
The Customer
A Dairy and Feed Industry Powerhouse
With a staggering presence in a $15 billion market, this agricultural powerhouse operates across multiple locations and boasts diverse business units.
Notably, the company navigates the nuanced areas of dairy and feed, each posing unique challenges and demanding distinct solutions.
As the quest for excellence persists, the demand arises for a comprehensive digital manufacturing training platform that seamlessly integrates continuous skills development.
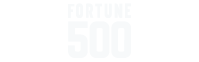
“
I’m thrilled that this is an enterprise wide initiative. Dozuki gives us cross departmental alignment to continue our full enterprise rollout in pursuit of our operational excellence journey.”
The Challenge Part 1
Reshaping Training for Workforce Dynamics
In facing a manufacturing challenge shaped by workforce shifts, the company grappled with the upcoming retirement of seasoned operators and leads. These employees are retiring and taking years of know-how with them.
As they prepared for the exodus of this highly experienced workforce, the reliance on a long job shadowing program raised concerns about the lack of documentation to support future training.
The risk loomed large, without an effective training infrastructure, the company faced the specter of production and quality issues, resulting in the scrapping of products. Rooted in a union shop history, the organization exhibited a distinct tribe mentality, a culture resistant to change that became a significant obstacle.
The plant floor was strewn with outdated paper instructions, and frontline workforce training lacked coherence. Leading to high employee turnover, safety incidents, and overall dissatisfaction.
The urgency amplified as the average tenure plummeted from 35 years to just 9 years in the last two years, with 47% of the workforce having less than 2 years of experience.
Changeovers, a crucial aspect of their operations, showcased the experience gap. With new hires taking 12 minutes compared to the 4 minutes achieved by seasoned operators.
The goal, set at a baseline of 5 minutes for all, aimed to enhance efficiency. With plants that handle 100 SKUs, there’s substantial savings to gain.
The Challenge Part 2
Unity Across Operations
Running multiple business units, the company sought a corporate solution that could standardize operations across all plants and prevent rogue practices.
With operations taking the lead, the project embraced cross-functional collaboration involving IT, HR, and more at both plant and corporate levels. The excitement stemmed from the full Dozuki offering, notably video work instructions, maintenance check sheets, and robust training. Their competitive analysis against alternatives Alchemy and Workday Learning highlighted the Dozuki advantage, leading to the decision to rip and replace their old system.
“When I showed Dozuki to senior management, everybody was so excited. All twenty people were jumping up and down for joy.”
-Training Coordinator
“What we currently have is, sit and learn,” revealed the Training Coordinator. “I need microlearning. I need two minutes or less. That’s exactly what Dozuki is offering.”
This became a pivotal moment, revealing senior management’s excitement around the project. Microlearning, with two-minute instructions, resonated with the company’s need for accelerated training timelines.
Leveraging Dozuki, the company aspired to trim the typical 13-week training period new hires, focusing on a faster time to competency and making employees confident quicker.
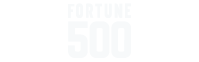
“
Dozuki changed everything for us.”
The Dozuki Solution
Accessible and High Quality Documentation
The ability to validate and regularly assess skills became paramount, addressing the unique challenges posed by a rotating set of skills required in this industry.
What sets Dozuki apart in this story is its roots in digital documentation. With a foundation of standards-based processes, Dozuki allowed the customer to build a controlled library of production standards, which was then organized into training units. This combination of digital standards and training platform allowed for operator training to scale across operations without variation.
Dozuki, initially rooted in training solutions, now unfolds as a transformative force shaping continuous skills development and expanding its impact across diverse functional work areas.