
90% Faster Onboarding
How a Fortune 500 motion and control technology manufacturer accelerated frontline operator training time after just one month with Dozuki.
The Customer
Enabling Operational Excellence
A global powerhouse specializing in motion and control manufacturing, this Fortune 500 company is one of the most productive in the world.
Boasting a diverse portfolio, this industry leader operates with a workforce of over 30,000 employees. Faced with the upcoming retirement of skilled workers, they are trying to replenish its workforce with the next generation. This transition involves replacing tribal knowledge with a structured curriculum, specifically tailored to address the skills gap prominent across the industry.
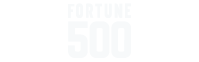
“
We’ve never trained people this quickly. New employees are becoming certified operators almost immediately instead of waiting a full year.”
The Challenge
Fixing Skill Gaps With Enhanced Training
The company is on a quest for standard work generation and process improvement. The objective is to identify bottlenecks in processes, enabling strategic decisions on equipment changes, retraining team members, and additional capital equipment.
“We need a supportive curriculum to replace the retiring skilled trade workers. This transition is not only about inheriting tribal knowledge but also about incorporating a new set of skills into the workforce.”
-Vice President of Manufacturing
A critical challenge is the inconsistency caused by tribal knowledge and check sheets. The team aimed to establish standard work. But despite having a training matrix, they lacked comprehensive backup documentation.
According to the Human Resources Manager, “Some processes are done just because they’ve always been done that way. We need a solution to deliver consistent results across multiple locations.”
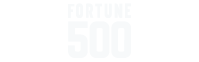
“
Dozuki is helping the sustainability of the training we’re given. Normally, operators go back to work, then learn all the bad habits and forget everything that we trained them to do. Dozuki allows us to keep everyone on track.”


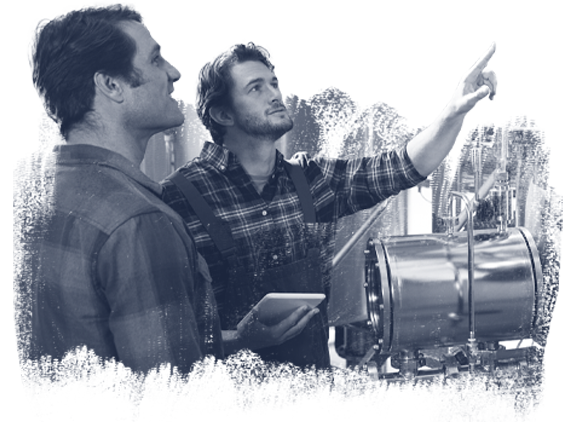
Training Acceleration
Dozuki helps keep operators on track.
AFTER ONE MONTH
Faster onboarding
$80,000 annual savings per plant
MASTER SKILLS
Day for New Operators
Improved operational efficiency
CHANGEOVER TIME
Reduction
$54,000 annual savings in just two plant areas
The Strategy
Driving Improvements
Handwritten notes aren’t a sustainable training method. They often go unnoticed and delay recognizing potential improvements.
“In our old Microsoft Word based system, creating work instructions is cumbersome, confusing, and hard to manage. The sad part is, I don’t know how many people actually even read our instructions.”
-Manufacturing Engineer
The company sought out a digital manufacturing training platform that encourages team members to provide direct feedback on processes, allowing for quicker identification and implementation of improvements.
This shift towards improvement ensures they don’t have to wait for weeks to address issues and can swiftly incorporate suggestions for process enhancement. The customer also highlighted the use of training to embed safety culture into guides and use comment sections and forums for resolving safety issues.
In the motion control industry, this could be a matter of life or death. The platform they sought not only needed to ensure critical safety items were captured and presented effectively, but also facilitated discussions among operators on safety concerns.
The solution would serve as a central hub for safety-related information, promoting a proactive approach to safety within the team.
Their existing method, centered on Microsoft Word and traceability software, lacked a set format, making it difficult to update old documents.
The subjective nature of their training system, using an Excel sheet with opinion based circles, posed challenges, and the manufacturer needed a more objective digital system.
The desire to address gaps in the current system, such as knowing who is trained and available to work, and the need for improved communication between different areas, drove their search for a solution.
“Our manufacturing manager tries to figure out all the best practices from all the different locations and consolidate them. It’s like a second full time job, and we need to free him up for other work,” commented the Manufacturing Engineer.
The Dozuki Solution
Visual Training
Dozuki training tools incorporate videos and photos to enhance communication and execution of processes, providing multimedia support for their operations.
The Plant Quality Manager is impressed by how empowering it is to be able to work through training at your own pace. “Even if you haven’t worked on a certain machine for six months, Dozuki provides efficient refresher training so you never feel foolish.”
Dozuki offers dashboards to maximize analytics and supports linking to a separate form for handling nonconformance issues by filtering capabilities by area, auditor per team leader, and audit ID.
The dashboard includes an overall pass-fail rate and the ability to highlight any failed inspections. This aligns with the customers’ need for visual insight.