
Book Club: "Value Stream Mapping" (Part 1)
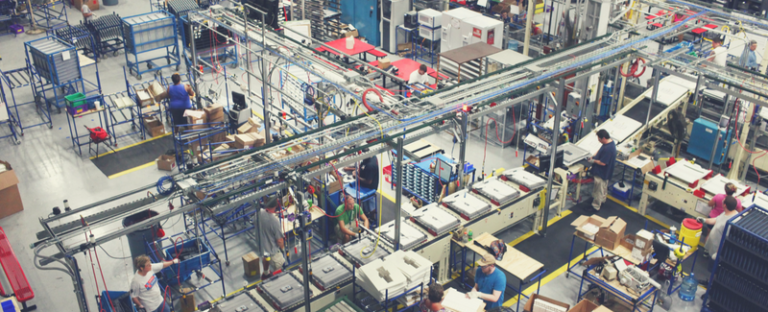
The Dozuki book club is your go-to place for industry books and resources. Our team curates knowledge from industry experts, letting you identify key takeaways and start implementing solutions quickly.
Introduction
- 1999 - “Learning to See” - transformed how people view workflows
- 2004 - “The Complete Lean Enterprise” - introduced powerful metrics for analyzing processes in the office
- Value stream mapping is a foundation for Lean management that applies to a broad spectrum of cross-functional teams
“Rather than viewing value stream mapping as just a tool to reduce operational waste, the broader use of value stream mapping as a methodology can transform leadership thinking, define strategy and priorities, and assure that customers are receiving high levels of value.”
Value Stream Management
No single person in an organization can describe the complete process from customer request to delivering a good or service. Wherever there is a request and a deliverable, there is a value stream.
- Value Stream - the sequence of activities an organization undertakes to design, produce, and deliver on a customer request
- Extended Value Stream - includes activities that precede customer orders
- Support Value Stream - supporting the delivery of value (recruiting, onboarding, IT support)
Value Stream Mapping (VSM) History
- VSM started with Toyota but value stream maps are now clearly understood in all industry circles.
- “Lean” means many things to many people
- Original philosophy was formed by Toyota (value, value stream map, flow, pull, and perfection
- “The Toyota Way” - expanded on the cultural and leadership aspects of Lean
- “Learning to See” - first look at what Value Stream Maps are
What is Value Stream Mapping (VSM)?
- VSMs are a means to establish a strategic direction for improvement
- VSMs provide a visual, whole-cycle view of request to delivery (the entire work system as it relates to customer value)
- Deepens the understanding of work systems that deliver value
- Builds a foundation for data-driven, strategic decision making
- Reflects workflow as a customer experiences it
Benefits of Value Stream Mapping
- Visual verification tool - helps visualize processes, reduce redundancies, and unify teams
- Connection to the customer - clear understanding of how actions relate to customer needs
- Holistic systems-thinking methodology - identifying the relationships between departments/processes allows people to make better decisions
- Simplification tool - a better idea of how work gets done on a macro level
- Practical means to drive continuous improvement
- Effective orientation for new hires
Common Failures with Value Stream Mapping
- Using the mapping process solely as a work design exercise
- Using the map to make tactical improvements
- Creating value stream maps during a Kaizen event
- Value stream mapping is strategical, while process mapping is tactical and should be used for Kaizen events
- Creating maps but not taking action
- Mapping with an inappropriate team or no team at all
- Creating maps with no metrics
Where Should You Begin?
This depends on organizational maturity and experience with Lean principles and improvement. Have a defined purpose, consensus around strategic direction, clearly defined business goals, and alignment around limited number of improvement priorities.
The VSM Phases
1) Prepare
2) Understand Current State
3) Design Future State
4) Develop Transformational Plan
5) Execute Transformational Plan
Laying the Groundwork
It’s important to prepare and scope a project before value stream mapping starts.
- Provide an overview of VSM to your team
- Make sure your team has a basic understanding Lean principles
- Include leadership in the discussion
- Expose middle management and front lines to VSM concepts
Develop a Value Stream Mapping Charter
A well-defined charter plays a vital role in successful value stream mapping activities. They help you plan and scope the endeavor, while also communicating clearly with key stakeholders.
The elements of a charter include:
- Scope - parameter of mapping activity
- Value stream - define what value stream is being mapped
- Specific conditions - definitions for what to include (and exclude) in mapping activity
- Demand rate - the volume of incoming work
- Trigger - the thing that initiates workflow
- First step, last step - starting and ending points of a process
- Boundaries and limitations - decisions and actions not allowed to be taken
- Improvement time frame - a firm deadline for implementing improvements
- Current state problems and business needs - consensus regarding current problems and why improvements need to take place
- Measurable target conditions - raw numbers for the current and future states of the value stream
- Benefits to customers and business - list two to five direct benefits, which will help reduce resistance to change
- Logistics - dates, times, and locations of mapping activities
- Mapping team - a list of the mapping participants, with a bias of company leadership
Socializing the Charter
- To effectively implement improvement from a VSM project, you need to engage three groups:
- Affected leadership
- Mapping team members
- Any affected workers in the value stream
- Exercise humility and an inclusive mentality
- This helps to galvanize your team around a common goal
Collecting Data
- Current and forecasted customer demand
- Quality reports
- Predict how much time to allot for walking through the value stream
Understanding the Current State
You need to have a firm understanding of the current state of the value stream in order to make improvements. VSMs act as visual storyboards that show how work currently gets done.
Activity Kickoff
- Hang a large piece of paper and use sticky notes to draft the value stream map
- Review the charter as a group
Value Stream Walks
- Going to the Gemba - the real place, where work is actually done
- Actually walking through the process will give you a deeper understanding of the work
- Be clear with workers that the observation is about work systems design, not an evaluation of worker performance
- Otherwise, they might withhold information about how the process actually occurs
- Do the same value stream walk twice in one day, for an even deeper understanding
5 Steps to Documenting the Current State
1. Perform First Walk:
- Obtaining the most basic information needed to understand the current state.
- This helps break the value stream into process blocks, which helps the team determine how to construct the map
2. Map Layout:
- Using the sticky notes as previously mentioned, the team places process blocks on the map.
- Each block should contain what is done and who does it (the activity and the functions that perform it)
3. Perform Second Walk:
- This walk identifies performance (time and quality) and barriers to the flow of the value stream.
- Key Metrics for Each Process Block:
- Process time - the time it takes to do the work of a single process (not including delays)
- Lead time - the time from the moment work has been made available to a worker until it is is passed on to the next station
- Percent complete and accurate (%C&A) - the quality of each processes output
- Barriers to Flow:
- Batching - holding work for a specific quantity or time
- System downtime or sub-optimal performance
- Shared resources or inaccessible staff - if staff has multiple obligations and are not available to do the work as soon as it arrives
- Task-Switching/Interruptions
- Prioritization rules - identify any formal or informal prioritizations for teams that could impede workflow
- Additional Information:
- Work-in-Process (WIP) - accumulation of work between or within processes
- Number of people - include the number of employees that currently perform the work on the process blocks
- Number of hours worked - note whether employees are completing their work within the normal work-day hours
- Process effectiveness - the percentage of upstream work that successfully converts into downstream work
- Work trigger - how people know to start doing the work
- Key Metrics for Each Process Block:
4. Add Map Details:
- Adding the information from the second walk to the process blocks. Include all “key metrics” (as described above) on the sticky notes.
- Mapping Information Flow - understanding how information flows throughout the value stream to identify technical gaps and inefficiencies. Use sticky notes to denote all IT systems and applications used across the value stream.
5. Build Timeline and Map Summary:
- Illustrates the efficiency in delivering goods or services to customers.
- Calculating Summary Metrics:
- Total Lead Time (Total LT) - total time to deliver on a customer request
- Total Process Time (Total PT) - total work time required on the timeline critical path
- Activity Ratio (AR) - degree of value stream flow, calculated by Total PT divided by Total LT
- Rolled Percent Complete and Accurate (Rolled %C&A) - the compound effect of output quality, calculated by multiplying all %C&A
- Total Labor Process - total labor time on all process blocks
- Total Labor Effort - annual total labor process time
- Calculating Summary Metrics:
Gaining a Deep and Collective Understanding
VSMs should not only clarify how work gets done, but also illuminate the inefficiencies.
It’s helpful to hold a briefing after the current state Value Stream has been mapped to best align people with the goal of improvement and help them understand why change is needed.
Related Posts
View All PostsBook Club: "Value Stream Mapping" (part 2)
The Dozuki book club is your go-to place for industry books and resources. Our team curates knowledge from industry experts, letting you identify key takeaways and start...
Continue ReadingWhy Do Value Stream Mapping? | Benefits & Examples
A successful business incorporates two critical factors, customers, and cost. The goal of any business is to provide the most outstanding value for the customer at the lowest
Continue ReadingUnderstanding Value Streams with Karen Martin
Employee on-boarding is often overlooked in the business world. We spoke with Karen Martin, author of "Value Stream Mapping" about why all supportive processes are equally...
Continue Reading