
I Got 99 Problems, But Skills Ain’t One
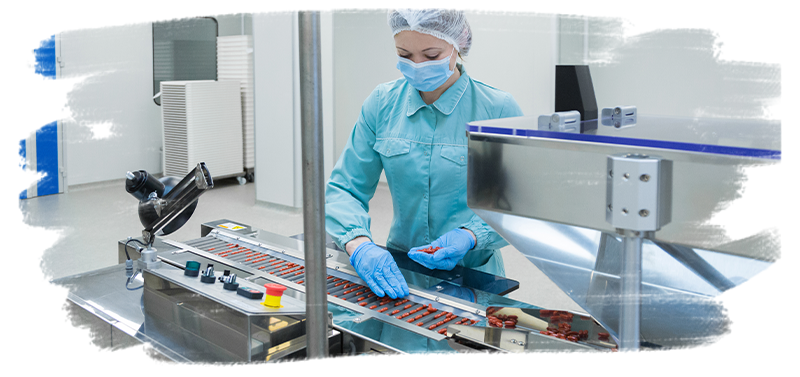
How many of your frontline manufacturing workers are engaged, productive, and feel a sense of ownership in their process?
Manufacturing Digital recently reported that engaged employees have productivity rates that are 70 percent higher than those of non-engaged workers. Additionally, they showed:
- 78 percent higher safety record
- 70 percent lower employee turnover
- 44 percent greater profitability
If you want your workforce to be that productive and engaged, our recommendation is to focus on skill development.
According to the APA’s 2021’s Manufacturing Engagement and Retention Study, a key retention activity is offering job training and career development opportunities that help employees expand their knowledge, skills and abilities and apply the competencies they have gained to new situations.
Manufacturing companies that give their workers opportunities for broad experiences and interesting and challenging assignments have an edge over competitors.
Below, you will learn how to support your workforce with best in class digital tools. And even when inevitable problems arise, their skills will remain high.
Training Mitigates Employee Attrition
Companies that offer inefficient training methods and limited visibility into the path for vertical growth cannot prosper. Nor can their employees. This gap will leads to lack of confidence and instability in their team’s work assignments, combined with a blind spot around future career prospect.,
No wonder resignations and ghosting have become the norm in our industry. Employees come and go so quickly. It's not a static workforce. Some people start today, receive poor training, and don't return to work tomorrow.
What’s more, if that reputation for being a revolving door becomes a part of that company’s employer brand in the community, word spreads quickly.
How are you empowering your facility managers to tackle gaps in the frontline workforce? And what tools do your managers have to ensure they have the right skills on the frontline?
Whichever tool you implement, our recommendation is simple: Make it visual.
Visuals in any form of communication reduce the time it takes for a viewer to understand and respond to information. Training and skill development can be complex and nuanced, so by creating a visual portrayal that extends the viewer’s ability to see, think, and know, empowering frontline workers to grow is a natural byproduct.
Your connected worker solution need visual achievability that’s purpose built into the design. This proves to employees that someone at work encourages their development and will recognize them for great work. This solution is ideal for our industry where retirements, resignations, absenteeism, and stopgaps with unskilled workers have become the norm.
Customer Spotlight: Lighting Manufacturer
A common complaint we hear from manufacturers across all verticals is that they have some kind of skills matrix, but it’s basically a glorified Excel spreadsheet. Few companies equip their managers with modern solutions that are tied into the actual training documents and quizzes.
One of our customers, a manufacturer of performance lighting systems, has been growing rapidly over the past three years. They now have two hundred product lines, and have had to say goodbye to managing employee skills via paper based systems.
“We have a skills matrix and it's but it's competency based. For example, we won't say that employee A is qualified to build product B, we will say that employee A has the necessary skills to produce products A,B,C,D and E. This is one thing that Dozuki has enabled us to do. If we have someone who can use a screwdriver, soldering gun and power supply for testing, then that means that they can go and build all of these different products. We have something that's more specific, and if we wanted to go into product specific training, then that would be, that would be good.”
The moral of the story is, every manufacturing company has the equivalent of a spreadsheet, or a makeshift solution, just sitting around in a folder, collecting digital dust.
That asset needs to be celebrated, multiplied, elevated, productized and leveraged.
Dozuki can help you do just that. Encouraging people’s development and recognizing them for doing good work will be both easy for you to execute, and visible for all to see.
Remember, your talent pipeline must be built, not bought.
In Deloitte’s annual manufacturing industry outlook, 75% of manufacturing leaders listed attracting and retaining quality workforce as a primary business challenge.
Dozuki offers you a potential retention advantage, showcasing your company’s commitment to supporting its workforce with best in class digital tools to perform their jobs well.
And no matter how many problems you might have, we’ll ensure that skills ain’t one.
Related Posts
View All PostsHow To Increase Productivity in Manufacturing
There are several ways to define productivity depending on the context. In terms of manufacturing, productivity relates to the speed at which quality work is performed....
Continue ReadingFeature Spotlight: Prerequisite Guides
Lean Document Creation & Revision At Dozuki we view creating work instructions like any other manufacturing procedure, implementing lean principles throughout the authoring...
Continue ReadingLean, Six Sigma, and Quality Management Systems
Six Sigma, Lean, and Quality Management are distinct approaches to reducing waste, defects, and providing value to the customer. With so many approaches to process...
Continue Reading