
5 Instant Benefits of Digital Work Instructions
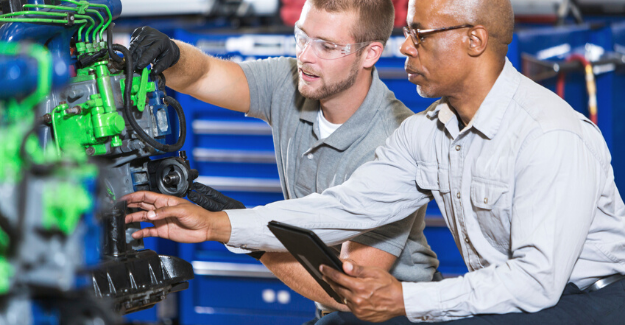
Unlike other digital transformation projects, making the simple switch from paper-based work instructions, SOPs, and other documentation to digital work instructions provides instant benefits for your workforce and bottom line.
Other digital transformation projects can take years to net any tangible ROI — digital work instructions yield instant value.
Businesses who adopt Dozuki see immediate gains in communication, employee performance, training, and more. Below are five instant benefits that companies can expect when making the switch to digital work instructions.
Increase Accessibility & Control
Digital work instructions provide access via any mobile device, tablet, or computer. Their paper-based counterparts are stored in large binders, often stacked in the back corner of the factory floor. If operators need access to a document, they have to pause their work, spending valuable time to find and transport the information.
Digital documentation tools are easily searchable and can leverage QR codes to instantly access relevant documents while on the shop floor. This provides real time savings and ensures that workers have access to accurate information anywhere.
In Dozuki, you can even control access to documentation based on roles, departments, or shifts. Trust that workers are only accessing current, approved procedures — every time.
Capture Tribal Knowledge
Capturing the knowledge of your most expert workforce is a challenge across almost all manufacturers. With growing numbers of retirements, and the growing skills gap, this trend is not slowing down anytime soon. Digital work instructions enable you to transform tribal knowledge into an asset for your workforce to train against.
It’s estimated that U.S. manufacturers are losing 11% of their annual earnings, or $3,000 per existing employee, due to the skills gap. As manufacturing faces a mass exodus of experienced workers, capturing this tribal knowledge is the key to training the next generation and solving the skills gap.
Digital work instructions make it easy to embed videos and photos of experts performing the work. This enables you to phase-out the errors passed along through job shadowing and outdated training documents. Consider it work instructions for the YouTube generation.
Streamline Process Improvements
Digital work instructions remove friction from the improvement process. Built in revision tools make approving changes is fast. Relevant personnel are notified when changes have been made, and can quickly follow the designated approval process to release changes to the floor.
On the other hand, paper-based documents are inherently difficult to update. When changes are made, old copies have to be tracked down and disposed of, then new copies printed and distributed to the appropriate teams.
This cumbersome process inhibits continuous improvement. When documents are resistant to change, they’re resistant to improvement as well.
“Using Dozuki, even a brand new person can come to the workplace and get trained on a process. On day one, they have the ability to comment and provide suggestions for improvement. That’s a behavior we want to coach. We want every employee to be in the improvement game.”
Manager of Operational Technology, 3M
Improve Employee Performance
Standardize training and onboarding across teams, shifts, and locations by using controlled digital work instructions as the basis of your curriculum. Digital work instructions help support employee performance by communicating best practices with a standardized and visual approach.
85% of quality mistakes are still caused by worker error — current training programs are the common root cause for this. By using digital work instructions to transform traditional training practices, companies can see reduced quality costs.
"Dozuki allowed operators to relieve some of their anxiety where they wonder 'Am I doing my job correctly?' 'Did I remember to do everything?' This motivated members (employees) to adopt Dozuki because they can now rely on the processes rather than tribal knowledge."
Learning & Development Change Coach, Johnsonville
Collect Valuable Data Insights
By leveraging digital forms and monitoring employee performance, digital work instructions can provide new insight into the state of your operations.
Use digital forms to insert prompts within processes to gather data on timing, quality issues, training, and more. View the information in real-time, to help resolve issues on the floor and follow efficiency gains.
Start Realizing the Instant Benefits Today
Related Posts
View All PostsElectronic Work Instructions in Industry 4.0
How do electronic work instructions factor into Industry 4.0 and your digital transformation strategy? With advancements in technology, it’s time to reevaluate how these...
Continue ReadingWhat Makes a Good Digital Work Instruction Software?
When Bob Dylan sang the lyrics, “the times they are a-changin’,” he probably never envisioned what the world would look like just six short decades later. The rise of digital...
Continue Reading