
Creating The Frontline Of The Future, Part 7
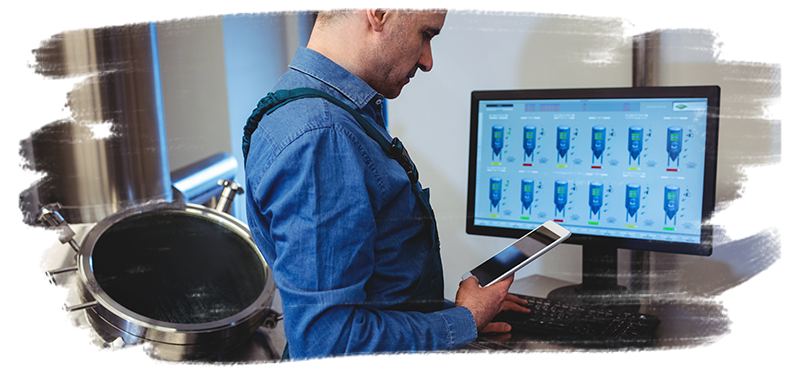
Technology Enables Resilience
Do you know what the first manufacturing technology was?
Let’s go back to prehistoric times, over two million years ago.
The Stone Age began with basic stone implements. Broken rocks were the first manufacturing technology. Talk about cutting through the clutter.
However, stone implements couldn’t scale. And made it hard to control quality.
Thankfully, manufacturing has undergone multiple industrial revolutions in which innovative technology has transformed the way we meet consumer demand, and build and sell products.
The best manufacturers identify and seize on these revolutions, accelerating transformative technology in ways that makes their work more resilient and less prone to interruptions.
Sadly, most digital transformations on the frontline fail because leaders treat digital technology the same as hardware and machines, or companies pick tools that are too advanced or high tech for the frontline worker to adopt.
What good would it do to bring a drill press back to the stone age? How would lean manufacturing help a cave man survive the winter?
It's not as simple as adding a tool or changing a process, manufacturing evolution requires a holistic approach that searches for an entirely new way of work.
We believe the frontline of the future relies on current technology widely adopted today, not future technology widely adopted thirty years from now.
In this lesson, we’re building on the work we’ve already done with process, accessibility and training. Let’s explore the technology that links them all together.
Starting with what manufacturing tech looked like in the past:
-
Dirty, dusty binders stacked on shelves in the break room
-
No wifi on the plant floor, or only available in some areas
-
No handheld digital devices are available to workers on the floor
-
Operators can only access company apps at shared computer stations
Consider what happened at a recent facility we visited. Our customer is a medical device company, and their regulations require keeping every revision of their document for one hundred years.
They have more than a shelf or a corner of the break room for their papers. They have a whole long hallway dedicated to old work instructions, as they have historically operated on paper. In addition to this, they also have a whole separate facility that stores the remainder of this process information.
Sounds like the kind of technology that needs a digital refresh. As we look forward to the frontline of the future, consider these predictions as a mini diagnostic to track your progress:
Additionally, we want to make several technical recommendations. We already talked about how to think about tablets on the floor, so now we’ll expand that discussion to other key topics.
Enable offline functioning for low signal areas.
One of the exciting features Dozuki provides with its app is offline mode. This is a core reason our app even exists in the first place, as customers often asked if they could run procedures without internet access.
If you work in a giant industrial factory that spans multiple lots, buildings, or even miles, wifi is unlikely to be available at every square foot. Giant walls may impede the signal and dead zones are likely to creep up. And tablets wouldn’t work.
We have insured you against that with offline mode. Perhaps your team has field technicians who are working out in the hot sun at an oil rig in the middle of Texas.
Since the internet connection will be spotty or nonexistent, Dozuki is built so you have the ability to view your procedure. Before you leave to go into the field, you simply download the work instructions that you need.
Elevate hardware and accessibility simultaneously.
Earlier in this series, we spent an entire lesson on accessibility, and want to call back a key point here. Many times tech issues in manufacturing come back to the internet connection.
Devices need to be accessible, set up properly at workstations, and so on. Whether tablets are attached to the sides of machines, or embedded into the machines themselves, the big picture here is about access.
Every employee who has to follow some kind of procedure should have access to the hardware and software they need to do their jobs. Even the best tablet and computer program in the world do people no good if they’re not allowed to use them at any time.
Make security and privacy the foundation.
Technological transformation at your company is not necessarily about scaling up, it’s about meeting your unique workforce needs. Perhaps you work at a nuclear facility or fulfill government work orders.
Both require a higher degree of security and safety than other industries.
For example, air gap backups to restore data in the event of a disaster and protect sensitive intel from being accessed by unauthorized personnel.
Our customers’ safety and privacy is at the forefront of every feature we design. Whether they’re using audit logs, running validation for new releases, or other precautions for manufacturing experimental products, we want to make sure the technology is as secure as possible,
Brad Matthews, Industrial Engineer from Husqvarna Industrial Engineering knows this firsthand.
Using the Dozuki mobile app, multiple team members review critical work instructions on the line, providing an in context audit to accurately update instructions. This allows them to implement the comments of all four auditors, take and upload new photos into the work instruction, and show people the updated version immediately. Brad commented:
"Updating work instructions with a phone on the fly has been really helpful. Before it would have taken an entire day to update an instruction, now we can do it on the fly from the floor.”
With the above recommendations, you’re well on your way to building a resilient tech stack that can stand up to all your demanding customers.
We believe the next industrial revolution is the intersection of digital devices, data, and their human counterparts. Soon your factory processes will be now visible and controllable from anywhere with these cloud enabled systems.
The frontline of the future will be a connected one.
Read Part 8 next!
Related Posts
View All PostsCreating The Frontline Of The Future, Part 8
Alignment Fosters ScalabilityIn the early stages of digital transformation, only a few stakeholders are involved Manufacturing companies typically begin their journey by...
Continue ReadingCreating The Frontline Of The Future, Part 9
Workforce Development You’ve probably heard the adage, the tool is as only as good or bad as the user. We believe this principle has broad applications in digital...
Continue ReadingFrontline of the Future: Part 1
Historical Forces Impacting Manufacturing At Dozuki, we have our finger on the pulse of manufacturing trends. We believe it’s part of our mission to formulate clear...
Continue Reading