
Creating The Frontline Of The Future, Part 9
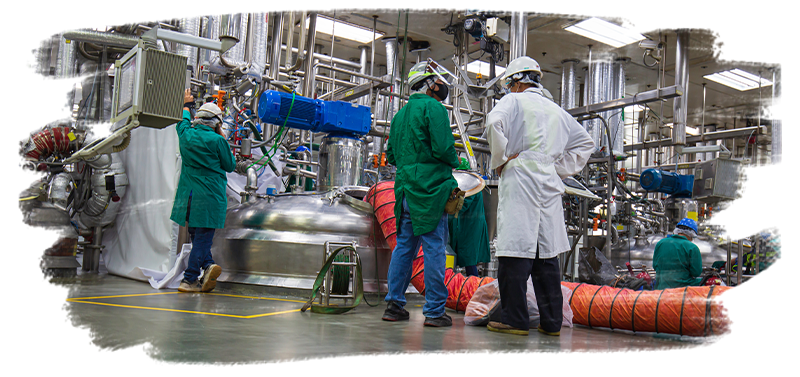
Workforce Development
You’ve probably heard the adage, the tool is as only as good or bad as the user.
We believe this principle has broad applications in digital transformation work.
As we mentioned in part 1 of this series:
If you’re starting with technology, you’re starting wrong. The most successful and sustainable manufacturing companies start with people, and the tech comes later.
In the informative book, Faster, Better, Cheaper in the History of Manufacturingwe learned the stories of real inventors and industrialists. And it’s not only about machines, but also about people. Christopher Roser writes:
“Throughout history, numerous technical advances were made not to increase productivity but to get rid of people. Robert invented the continuous paper machine with a primary purpose to get rid of workers. Blanc developed interchangeable parts to control strong independent gun makers. Taylor considered an intelligent gorilla a better worker than the people he had. Smith invested heavily in robotics with the goal to get rid of workers, envisioning a lights out factory.
And manufacturing history is a lot of history of workplace conflict, with managers trying to solve the conflict by getting rid of the workers. Nevertheless, we still need workers. Even advanced lights out factories and semi automated chemical plants need maintenance and installation. Yet, most companies still treat workers as machines.”
The challenge is, manufacturers aren’t as inclusive as they could be. Traditional approaches to workforce training, knowledge management and quality management were limited to only certain stakeholders within the company.
If you want to create the frontline of the future, here’s a diagnostic to track your progress:
To bring your frontline out the past and into future, here are the tactics we recommend:
Moving from pilot to enterprise
For your measured adoption of digital transformation, start with your gatekeepers. The people most hyped about the functionality. The people who are actually creating procedures and own the knowledge.
They will be the champions that inspire others to join the movement.
Once you get them onboard, then slowly start to bring in other departments that can add to continuous improvement and culture. Like your training team, for example. They can iterate on the first version of the frontline training and take it to the next.
All transitions to digital are going to be a bit rough around the edges at first, so your second line can help perfect your processes. They will ensure there are no safety risks and everything is audit ready.
Engage managers to iterate off of data
If you’ve ever spent time on a factory floor, most engineering and operating jobs don’t revolve solely around machines or analyzing data on a computer.
Manufacturing is a very people oriented job, working with groups of people every day to solve problems. We believe in a combination of both. People centric has always been our approach, but we also know how important it is to take a step back and see what the data says about your people.
This is why Approval Workflows are a critical feature to empowering your people. They allow you to publish and push new work instructions and process across the floor quickly. With our Document Control, now the governance of your processes will remain robust.
Don’t let technology trump the real asset
In our experience, machines aren’t actually innovating anything. People are the source of all your competitiveness. And the frontline of the future puts them first.
The future of quality will become a balancing act between the advantages of new technology and cultivating the human centric processes that make businesses successful. Every manufacturer works in the people business. No matter what they make, it is the people that help them make it.
Our recent numbers show that 72% of tasks in the factory are still performed by people. Your job is to take the people and connect them with tech, skills and processes to do the work. The myth of automation is that you will automate yourself out of humans in manufacturing.
But you still need people to buy the robots and service and install them. People aren’t going away. They’re an invaluable part of the process.
In sum here’s a passage from The Organizational Handbook of Creativity, which encapsulates this people centric philosophy:
“The urge to create is also a healthy part of the human being, and creative activity is usually accompanied by feelings of satisfaction and pleasure, which are fundamental elements of emotional welfare and mental health. At the level of the organization, creativity is an essential factor for innovation and consequent organizational success. It has been considered a critical element for the survival of many companies, in view of challenges generated by globalization, growing competition and accelerated rhythm of change. These factors drive organizations to remain in a continuous process of innovation, which requires better use of available resources, especially the creativity of their human resources.”
As you create the frontline of the future, err on the side of humanity, empathy and inclusion.
Start with people, and the transformation will follow.
Finally, read Part 10!
Related Posts
View All PostsCreating The Frontline Of The Future, Part 8
Alignment Fosters ScalabilityIn the early stages of digital transformation, only a few stakeholders are involved Manufacturing companies typically begin their journey by...
Continue ReadingHow to Get More Out of Your Work Instructions
When leveraged properly, standardized work instructions can transform operational efficiency, quality management, employee performance, and more. All industrial businesses...
Continue ReadingManage Workforce Training with Dozuki Courses
At Dozuki, we’ve made it our mission to make Standard Work an industry standard. We envision documented standards and worker knowledge continuously improving alongside one...
Continue Reading