
What Manufacturing Leaders Need to Know About Workforce Empowerment
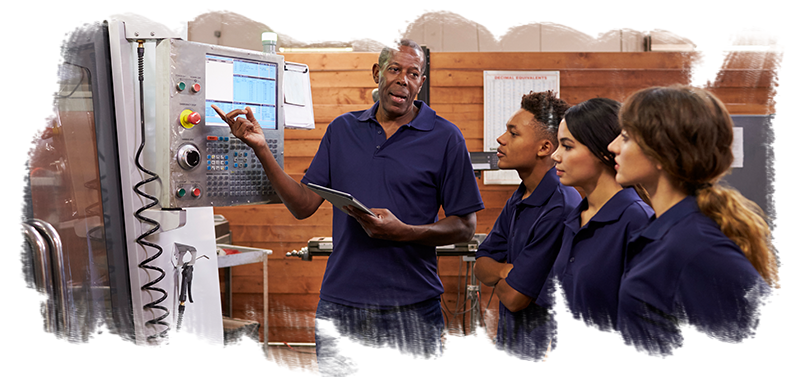
Empowered workers require enlightened leaders.
Organizations can either act as an incentive (or an obstruction!) to the expression of a frontline worker's sense of ownership.
Historically, manufacturers dating back to the industrial ages operated by command and control. Employees with inconvenient feedback that didn’t align with management were either fired, or sent off to facilities in remote locations.
To quote Tim Robbins from my favorite manufacturing movie, The Hudsucker Proxy:
“You’re barging in here and taking up my valuable time! I've got a company to run, and I can't have every deadbeat on the payroll pestering me with their idiotic brainwaves!”
Have you ever worked for a leader like that? Ownership has left the building.
Toyota came along the seventies and shifted the paradigm of modern manufacturing. They began developing the foundation of what we now know as lean culture, part of which included folding factory floor suggestions into improving operations.
Their frontline workers contributed process improvement ideas, rather than just punching in and going through the motions. Their input was truly welcome.
Fast forward to today, and the leading manufacturers that achieve focused and persistent task engagement on the floor are aligned on an intentional and consistent effort for workforce empowerment.
How does your culture train frontline workers to take prudent risks? Do your teams feel empowered to test out new process ideas to find new pathways to improvement?
Here's what manufacturing leaders need to know about workforce empowerment. Below are strategies and tactics that you can put into action on the factory floor, starting today.
Overcoming Barriers To Empowerment
Most plant managers, frontline supervisors and human resources professionals in our industry have seen firsthand horror stories of new employees coming to work on their first day, but not coming back from lunch.
What happened? Why couldn’t they last for the full shift?
One observation many of our customers make about this trend is, it’s because frontline workers didn't receive proper, or even any training. On day one, they might be operating a multi million dollar piece of equipment, and if they make a mistake because of poor process, that could cost the company hundreds of thousands of dollars.
In short: fear.
Now, while the apocryphal “quit by lunch” story might not resonate with your facility, it still suggests barriers to empowerment that need to be overcome.
As an example, perhaps your process of authoring and distributing work instructions for approvals and implementation is “cumbersome.” That’s a red flag term that comes up many times in Dozuki’s customer conversations.
Managers often stifle the creation of new processes from tribal knowledge. Leaders aren’t kindling the entrepreneurial flame within employees to express their ideas publicly.
This is when lightweight, streamlined digital training solutions swoop in to save the day.
We were speaking to one of our food manufacturing customers recently, and they’re a perfect case study of how to overcome barriers to empowerment.
-
Their facility had a new frontline employee who was just a few weeks past their initial training, with no previous manufacturing experience.
-
The young man was tasked to perform a complex changeover by himself with nothing but a Dozuki guide on how to do so.
-
And they were amazed to see that he performed the entire changeover without any issues in ninety minutes. The process usually takes three to four hours.
This is what empowerment looks like when fear isn’t a factor.
If you have young, new or inexperienced workers, leverage the power of digital training programs to push them out of their comfort zone.
Soon enough, rather than tapping someone on the shoulder, they will tap the screen on their tablet, and feel empowered to execute challenging tasks.
Another aspect of fear that blocks empowerment is exclusivity.
Workers need to feel that training is done with them, not to them.
Manufacturers should provide sufficient opportunities for them to be involved in decision making, problem solving and goal setting. They should provide employees with at least some degree of sufficient control over how they perform their jobs.
Whether it’s updating work instructions, improving training, or turning expert knowledge into trusted processes, employees will be excited to participate if they don't feel like it's being done to them, but with them.
Whereas if they feel like they’re just mindlessly following someone’s detailed rules and procedures that are imposed on them, they won’t be happy or engaged. Mostly scared.
Dozuki writes a lot about The Frontline of the Future, and we believe the days of just going through the motions under the watchful eye of the foreman are over. It’s only a matter of time before strictly policed rules that workers view as coercive will be a thing of the past. Such a disempowered approach will no longer become a source of friction and resistance between management and workers.
You can start today.
If you want to help workers bypass their fear of making suggestions that are wrong or silly, then err on the side of inclusivity and trust. For newer employees, give them the task so they understand, but also leave them to do the work. They shouldn’t be held captive by outdated work instructions.
As it states in The Toyota Way:
“The critical task for standardized work is to find that balance between providing employees with rigid procedures to follow and providing the freedom to innovate and to be creative in consistently meeting challenging targets for cost, quality, and delivery. The standardized work must be specific enough to be a useful guide, yet general enough to allow for some flexibility.”
You can't afford to bring somebody in and have them get frustrated because they don't understand what you're talking about.
But if you’re diligent about digital transformation, then operators can quickly relieve some of their anxiety when they wonder, am I doing my job correctly?
People’s reasonable fear gets quelled quickly when every task for every machine on every line has an instructional video that walks frontline workers through the process, one step at a time.
Reducing Fear and Increasing Empowerment
To replicate this first type of empowerment at your manufacturing organization, here are several recommendations:
-
Build a process so you capture those voices, ideas and observations into some sort of pipeline where you can say to people, “That’s a great idea!”
-
Use commenting where users can make notes on specific steps within a guide. They can ask for clarification when needed and offer suggestions for process improvements.
-
Build in a question and answer engine for users to ask and answer one another increases collaboration and knowledge sharing across continents.
-
Even on a relatively simple, day one job, invite your new operators to think about troubleshooting. A brand new person needs the ability to comment, observe, and improve. They immediately contribute to the standard.
-
In addition to experts sharing their knowledge, ensure your learners immediately have an opportunity to improve the standard. As a result, everyone is striving for betterment.
-
The most important question to ask on the factory floor is, “Can you show me how to do that?” People feel seen, heard, helpful and engaged. Especially if you’re documenting everything they say.
Now that you have an understanding of fear’s origins in manufacturing (and how to overcome it), in a future post, we’ll continue the discussion of empowerment as it relates to building manufacturing momentum.
Related Posts
View All PostsWhy HR Shouldn't Manage Your Technical Skills Training
Amid the Silver Tsunami, HR departments are hustling to onboard and fill personnel gaps, but they can’t predict the evolving demands of your operations. Manufacturing...
Continue ReadingAdapting Training to Meet the Needs of the Modern Manufacturer
Manufacturers are faced with a much different workforce than they've traditionally dealt with. Previous generations had more foundational knowledge, incoming generations need...
Continue ReadingHow 3 Leaders Tackled Key Workforce Challenges
A recent survey by the National Association of Manufacturers underscores a pressing concern for manufacturing executives. Nearly 75% identify attracting and retaining a...
Continue Reading