The training and quality teams at Automation Plastics believed in better work guidance and documentation, but didn’t have the right toolset to implement a solution.
Using a combination of Word, Powerpoint, Crystal Reports, and PDF files, their system lacked standardization, was slow to update, and didn’t effectively capture tribal knowledge.
When the time came to evaluate a comprehensive solution, they jumped into researching and quickly knew Dozuki was the right fit.
Lack of Standardization Prevented ISO 9001 Compliance
Ipper Collens, Training and Process Improvement Specialist for Automation Plastics, was frustrated by the limitations of their existing documentation tools and how they impacted the facility’s ability to achieve ISO certification compliance. There was no structured system for work guidance and documentation.
A combination of Word, Powerpoint, Crystal Reports, and PDF files was inflexible, confusing, and slow to update. “We were coming from a world with a complete lack of standardization, it wasn’t unusual to see three or four versions of the same document in use on the shop floor, it was a mess,” says Collens, “this poor communication was a major problem that derailed everyone’s performance.”
The entire Automation Plastics team wanted to improve documentation to achieve ISO certification compliance, but didn’t have the right tools to implement it. When the opportunity came to evaluate software solutions, Collens and his colleague Anne Klonowski started researching.
They required a system that had built-in version control, supported video instructions, and streamlined the approval process; when combined with their desire for easy-to-use software, numerous solutions were immediately eliminated. Collens and Klonowski agreed, “We felt Dozuki was the best way to take our informal and tribal knowledge and create work guidance that operators with all levels of experience can benefit from. This type of standardization was essential in successfully achieving ISO certification compliance.”
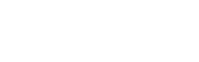
“
Implementing Dozuki helped control documents, capture expert knowledge, and to train consistently across shifts.”
Using Dozuki to Capture Tribal Knowledge
When employees have over 20 years of experience, processes become more muscle memory than anything else, new process updates aren’t properly documented, and paper instructions are often ignored. Training new, inexperienced employees was not reliable with such an outdated process. Since implementing Dozuki, training a new employee went from taking roughly 4 hours, down to just 15 minutes—a 90% time reduction.
Not only are these employees trained faster, they are also given instant access to the latest process updates via tablets and mobile devices at their workstations.
Most of all, Collens found that videos helped make the training process even more effective, “We felt Dozuki was the best way to take informal tribal knowledge and create work guidance that all of our operators can benefit from. It gives us documentation features and control like we’ve never had before.”
“Dozuki offers us the ability to capture knowledge of experienced personnel while utilizing the technical skills of millennials. The collaboration has been incredible.”
Anne Klonowski, Quality Technician