
World Class Training with Digital Work Instructions
Fortune 500 Food and Beverage Company
The Customer
A Fortune 500 manufacturer of branded consumer foods and pet food products sold through retail stores. In the past 150 years, they’ve built a portfolio made up of more than 100 brands around the world.
To achieve its goals of manufacturing human and pet food products that provide great taste, nutrition, convenience, and value for consumers, this customer needed a frontline digital transformation to create a world class training and upskilling program. So far, they have fully deployed Dozuki at five of their facilities, with plans for more.
The Challenge
The compounding issues of increasing staff retirements, lack of digitized processes, and lack of formal training program — the company was seeing spikes in quality issues and downtime.
As new frontline employees join, there was no program in place to get them upskilled properly to help meet production demands, and the cycle continued to repeat itself.
Customer Goals
This ultimate goal in partnering with Dozuki was to create a world class training and upskilling program within their manufacturing operations.
Historically, their facilities relied on job shadowing and word of mouth for operator training. Their training team was tasked with thinking outside of the box for their standard work manuals.
The company realized they had a need to create and distribute work instructions digitally. With high numbers of retiring staff and out of date process documentation in paper binders, standardizing process documentation was a must.
Sensitive assembly lines for perishable products meant changeover errors were costing the company millions of dollars a year in defects, supply chain issues, and profit losses.
A Training Manager reported they lose approximately $3 million dollars a year on just one line due to poor frontline training.
If frontline employees change one little thing incorrectly, it could cause the lids not to be sealed properly, which could explode. Errors like this cause raw material waste and huge profit losses.
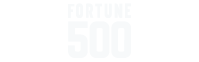
“
The Dozuki connected worker solution is on track to save millions of dollars on just one of our lines this year. It’s a game changer.”
Why did they choose Dozuki?
Our customer needed a central solution for maintaining changeover processes. Previously all they had was a generic spreadsheet with measurements, but no specific work instructions, tools, or images.
They chose Dozuki because it gave their frontline employees easy and instant access to key information from a tablet, rather than one person on each shift having knowledge for a single task.
“90% of our issues come from poor frontline training and a lack of documentation,” the Training Manager explained. “Dozuki gave employees a tool to help them fix a jam right away and not have to wait for help. Now the knowledge was all right in front of him. The Dozuki connected worker solution is on track to save just one line millions of dollars this year. It’s a game changer.”
Initially, Dozuki was piloted at one facility. Once results were shown, that facility has become a lighthouse for future rollouts across the enterprise.
How has Dozuki changed their day to day operations?
Prior to launching Dozuki, most employees relied on text heavy information and content, which lacked any visual context or support. Now that processes had photos and videos embedded in them, workers had a visual aid to reinforce processes, reducing the potential for errors.
All frontline operators are granted permission to be authors. If they don’t see something on their site, then they can create a process. Now employees have access to all the information they need to perform their work, rather than one person on one shift having knowledge for one task.
Digital training helped close gaps in basic manufacturing knowledge. This lack of assumed knowledge would have eventually turned into downtime.
But with Dozuki, every process is laid out in an easy to understand, efficient digital layout. There was no question about what their workers needed to do next to be successful.
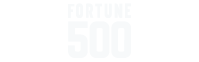
“
Assessing frontline competency is difficult. Dozuki helps us do this by using skills data to help inform workforce agility.”