Johnsonville makes a lot of sausages and believes in supplying its members with the best tools to do their best work.
At a large volume, minor deviations from the standard work can be costly. If a machine is set up incorrectly or a food safety mistake causes contamination, it can mean many pounds of meat must be scrapped in order to maintain a quality product.
A portion of these waste costs are caused by operator error. Standardized work instructions in Dozuki helped them to improve internal processes, which Johnsonville projects will provide considerable annual cost savings.
Poor Access Systems Meant Standard Work Wasn't Used
Johnsonville had been using a legacy document management system that made it difficult for operators to access standard work instructions and conducting a search was a lengthy process. The operator needed to pause their work, walk to the end of a production line, log in to the computer, and then dig for the right files.
Accessible Documentation the Frontline Can Trust
Taylor and his team knew that in order to reduce costs and improve internal processes, they required a solution that would improve document management and control, while increasing accessibility and ease of use for the Johnsonville operators.
Dozuki was the clear solution for Johnsonville because the intuitive interface reduced the authoring time and streamlined revision processes with custom approval workflows. Above all else, it enabled operators to easily use and be trained to documented standards.
There are many operators who now author the standard work documents thanks to the custom-approval flows that Dozuki offers.
By using Dozuki to standardize work and improve processes, Johnsonville was able to reduce costs and achieve significant annual savings.
These benefits provided Johnsonville with justification to expand their use of Dozuki and equip members with the proper technology to support future digital transformation projects.
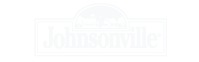
“
By using Dozuki to standardize work and improve processes, Johnsonville was able to reduce costs and achieve significant annual savings.”
Building Trust in Standards to Reduce Quality Costs
For any employer, mistakes carry not only a financial burden, but can also be an ethical one as well. Wasting animal products isn’t taken lightly at Johnsonville so if meat is scrapped for any reason and not used for sausage, this weighs heavily among operators.
After transitioning to work instructions in Dozuki, operators were able to develop trust in their internal process documentation. Morale improved and waste was reduced by allowing members to rely on the standards, as opposed to informal knowledge sharing.
Migrating away from their legacy documentation tool meant that operators could now access work instruction via tablets or from their equipment on the factory floor. This revolutionized the way standard work was done at Johnsonville.
Operators now feel confident in their ability to find the information needed and Dozuki allowed them to follow standardized procedures without disrupting workflows.