
Benefits of Procedures & Work Instructions in Manufacturing
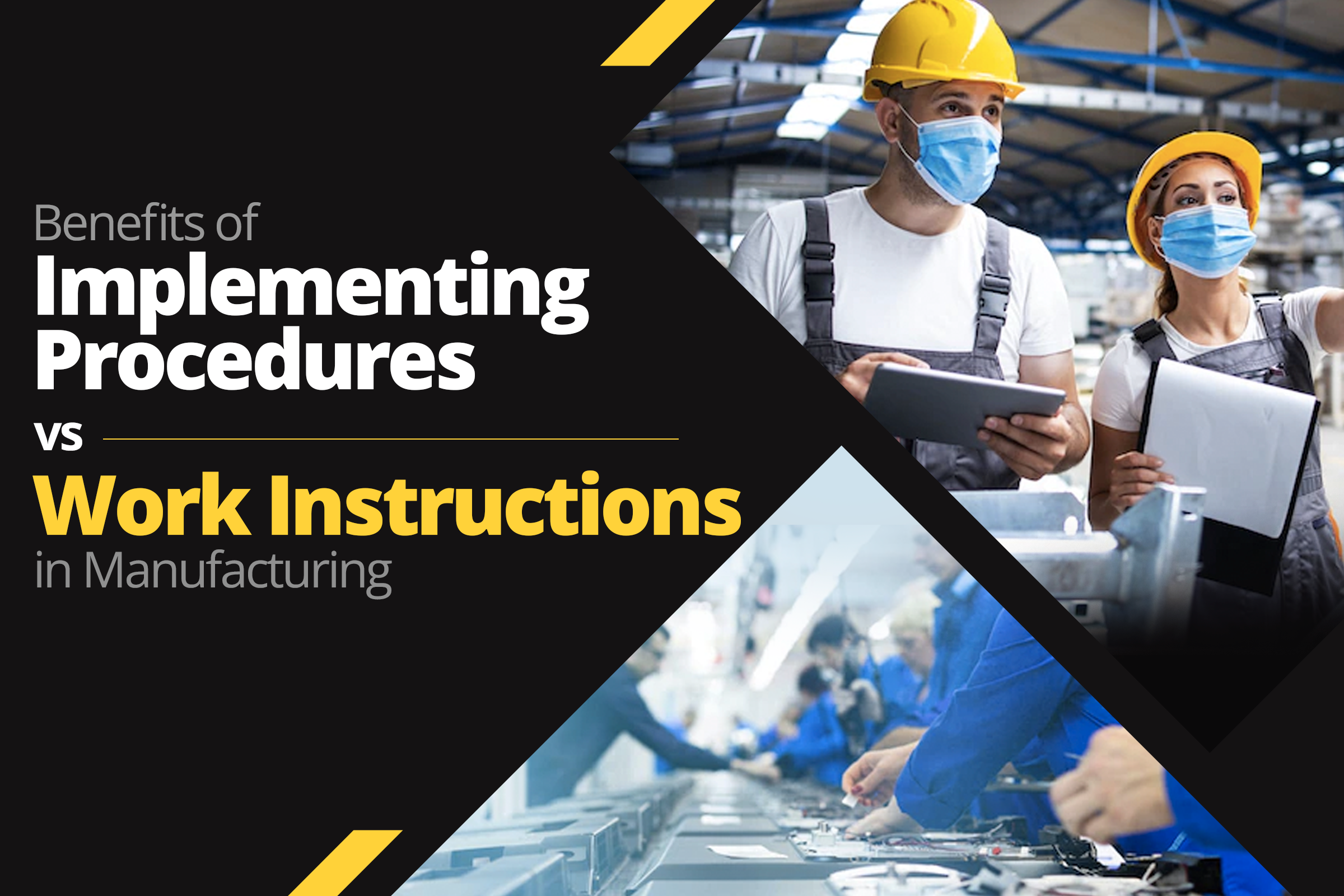
Ah, the lingo of business. If there’s one thing that the world of business and industry loves, it’s terminology.
Every industry has developed its own language, with specific words, descriptors, and acronyms that are often unique to a sector. And this lingo can be very beneficial, allowing people to quickly grasp concepts and understand each other easily.
The problem comes when the language and terminology are used incorrectly. When one person uses a term that they believe means something, and someone else hears the same term but understands it to mean something completely different, problems can arise.
The importance of clearly defining terms becomes much greater when they’re used in reference to production and the frequent use of heavy machinery or dangerous equipment.
Processes, Procedures, and Work Instructions
Three terms that are often confused and misused in manufacturing facilities are processes, procedures, and work instructions.
While these terms are sometimes used interchangeably, they shouldn't be. Each means something different and represents a different step in the production process.
Using them in the wrong way can confuse the way work is done and cause hiccups in a production line, leading to lowered productivity, poor communication, and a loss of revenue.
In this article, we will further define the difference between these three often misused terms and outline the importance of properly implementing each correctly in a factory.
We will also demonstrate the benefits of having solid digital work instructions in place as a supplement to carefully crafted processes and procedures.
How Do Procedures Work and Why They’re Important
When talking about the difference between procedures vs work instructions, the first thing that needs to be defined and explained are the procedures themselves. It’s more than likely that the term standard operating procedures, or SOPs, will be used interchangeably with the term procedures.
The term SOP describes a standard procedure that is outlined for employees to use as a guidebook when performing routine or repetitive tasks. A procedure describes the basics of which steps workers should take when completing specific work or processes.
For manufacturing companies, creating a standard procedure for each step of the production process is vital for success because it helps set a baseline for what is acceptable and standard concerning quality, compliance, and safety.
Reasons why having standard operating procedures in place is important:
Creates a Standard and Fosters Communication
Having a documented standard operating procedure keeps everyone on the same page. It outlines the correct and best established way of initiating and completing tasks, and which actions are incorrect, dissuaded, or even non-compliant.
Lessens Risk of Error and Accident
When employees are given a guidebook for success, they are much more likely to succeed. And more than that, they are much less likely to make critical mistakes that result from a lack of knowledge. Not providing SOPs for standard work is like allowing employees to experiment for themselves, encouraging a trial-and-error method of working that is doomed from the start.
Helps With Regulations and Compliance
Many manufacturing companies face the added requirement of meeting specific governmental regulations. Having documented SOPs in place provide manufacturers with an added asset to show auditors, inspectors, and legal representatives to prove that they are operating with safety and compliance in mind at all times.
. OSHA is a great example of a regulatory body that performs inspections at businesses. Because manufacturing comes with a high risk for workers in terms of the potential for catastrophic accidents, OSHA inspectors will be on the lookout for anything that could cause bodily harm or impact employees' well-being. Many inspectors will inquire about SOPs and ask for a hard copy to use as a reference during visits.
What Are Work Instructions and How Do They Work?
We have defined a process as an action that is taken to transform inputs into outputs. It’s a wide, encompassing term that can be used to describe the goal of a manufacturing facility or production line. Procedures are then outlined for each process that might require more detailed information.
Work instructions go a step further by detailing step-by-step information on how to complete procedures. For companies that operate in the manufacturing sector, work instructions are vital documents that help keep employees safe and impart valuable knowledge about how to complete specific tasks in a clear and easy-to-understand way.
Work instructions are put in place to help employees understand exactly how to complete a process or procedure. They are used to break complex procedures down into their simplest form, and detail how to complete each step safely and correctly.
All good work instructions should include:
- The goal or expected results of the process or procedure
- The person or persons responsible for completing the task
- The materials, equipment, and skill set needed
- Detailed, visual, or multi-media reference material that helps workers understand exactly what to do
- Safety and compliance concerns that are outlined and clearly visible
What Are Processes in Manufacturing, and What Are Some Types?
While the issue of procedures vs. work instructions helps companies define the best way to complete a process, processes themselves are the basis of the manufacturing industry. The kinds of processes used in manufacturing are as varied as the companies who use them. A process can be extremely intricate or shockingly simple, depending on the needs of the manufacturer and the intended result.
A process can be defined as an established method for transforming raw materials into ready-to-sell products. Manufacturing processes can be sorted into different categories, and then further subcategorized based on similar characteristics, such as the scale of the production required, the type of product, the intended role of the process, or the level of automation used during production.
Some of the most utilized manufacturing processes include:
Job-Shop Manufacturing
Job-shop refers mostly to a small series, or even singular production, of products. This type of manufacturing typically takes place in a shop that uses tools or machinery that share a similar function and may include workers who have specific skillsets. Job-shop manufacturers usually handle custom orders that are often used by other manufacturing companies in their production lines.
Batch / Serial Production
Batch manufacturing involves a range of products that are produced in batches, or simultaneously. These batches can vary from small to large inscale. These products often move through the production line in steps, meaning each batch will undergo individual steps in the process before moving on to the next.
Mass Production
Mass production is used in manufacturing facilities that need to produce a very large number of products quickly. Typically used to produce consumer goods, mass production facilities can produce several thousand products in a single month. Workers in this type of manufacturing facility are typically tasked with one specific step in the production line and may not need as detailed of a skill set to complete work.
Made-to-Order / Made-to-Stock
These types of manufacturing are dictated by demand. A made-to-order facility will produce a product in response to a direct order from a customer, meaning there are no products ready until orders are placed. The made-to-stock facility produces products in response to the expected, or forecasted, need. This type of manufacturing means that products are readily available when orders come in.
These categories of manufacturing are based on the size and scale of the process. There are further subcategories as well that relate to the type of process involved, and may include repetitive, discrete, continuous process manufacturing, and many more.
Differences Between Procedures, Work Instructions, & Processes?
There are key differences between procedures vs. work instructions, and how they are both used to complete a process. So, what’s the big difference and why does it matter so much? All three of these terms come together to form what is known as standard work.
A process is the overall goal of a manufacturing facility; that is to take inputs, or raw materials, and perform an action that transforms them into an output, or a product. The standard procedures then define the best way to complete the process. And work instructions are used to further explain and instruct workers on how to complete a procedure. Together, these three concepts lead to standard work.
Processes
A process can be defined as any activity that works to transform inputs into outputs. Or more simply applied to the manufacturing industry, the materials used and actions taken that result in a product.
Procedures
A procedure is the next step that leads from process to product and can be defined as a specific action taken to accomplish the goal of a process. For example, if the process being referred to is the manufacturing of brake pads for a vehicle, then the procedure is the specific way in which that brake pad is created, the materials that are used, and the way it's assembled or packaged.
Some processes will have no procedures attached to them at all, while others may have several. A procedure essentially explains the specific actions that will be taken to fulfill a process.
Work Instructions
A work instruction is a clearly defined, step-by-step guide that users and operators can refer to as a way to understand how to complete a procedure. The procedure itself isn’t enough, because without having specific, documented work instructions, employees are left to figure out the details for themselves.
For a manufacturing company that aims to produce high-quality, consistent products, work instructions are an absolute necessity.
What is the Purpose of Work Instructions in Manufacturing?
When identifying the importance of work instructions vs standard procedures alone, you might be wondering why work instructions are even necessary. The answer is that manufacturing companies rely on many complex processes and procedures that often involve the use of machinery, equipment, and tools.
Despite the rise in automation in factories, human workers are still at the front line of production and must interact with potentially dangerous and complicated equipment every day.
Having work instructions available for employees not only ensures they will be equipped with the knowledge to complete work safely but helps companies be confident that they are producing products that will meet their customers' needs and expectations.
The purpose of work instructions include:
Minimizes Variation and Lessens the Risk of Error
Work instructions are designed so that employees can complete a task the same way every time. This ensures that the result will be the same as well. Eliminating even the slightest variation in the way a job is completed means that companies will get more efficient work, higher productivity, and fewer mistakes.
Aids in Producing High-Quality Products
Manufacturing is a competitive industry, and customers demand high-quality, consistent products. With well-designed work instructions in place, companies can guarantee that they’re taking every effort to produce the kind of quality and value that will keep customers satisfied, and hopefully, coming back for more.
Makes Training and Upskilling Easier
With a skilled worker shortage that shows no signs of resolving any time soon, manufacturers in today’s job market are facing unprecedented challenges. This means that new workers will need to be trained quickly, efficiently, and most importantly, effectively.
Having clear and precise work instructions is the best way to help new employees succeed, and can even help companies up-skill and cross-train current employees quickly.
Benefits of Having Procedures and Work Instructions
While it's important to define the difference between procedures vs work instructions, what's more helpful is understanding that a successful manufacturing company will include both. The benefits that come with having documented standard procedures and clearly defined work instructions in place wherever they’re needed come in many forms.
Increases Productivity and Efficiency
Creating standard procedures will inevitably lead to an increase in both efficiency and productivity. Standard procedures allow employees to quickly answer questions, or better yet, have the questions already answered for them before work even begins. This means that they will be able to complete tasks faster and more accurately.
Eliminates Waste and Promotes Lean Manufacturing
Any tool that helps workers complete tasks correctly the first time will help to promote a lean manufacturing environment. This means that every outcome that might lead to waste, like defects, potential downtime, overproduction, and many more, can be avoided or minimized through the use of documented standard procedures.
Increases Quality Control and Assurance
SOPs also serves as a valuable tool for companies that help strengthen the likelihood of producing high-quality, consistent results in terms of production or work. When everyone is working from the same guidelines, it means the output will be uniform instead of variable. And nothing could be more important in terms of quality control.
Manufacturing companies should have a quality management system in place to ensure that every effort is made to create standard work that leads to higher quality products. Companies may refer to the ISO 9000 as a guideline for what's acceptable in terms of quality management. Having documented procedures in place is one of the most important steps companies can take while establishing quality assurance practices.
Not Using Work Instructions in a Manufacturing Company?
A manufacturing company that doesn’t have detailed work instructions faces certain disadvantages.
While the importance of defining standard procedures vs work instructions is valuable, nothing beneficial can be obtained if manufacturers don’t take advantage of the fact that work instructions are vital for increasing and maintaining a company’s productivity, efficiency, and quality control.
These three things help form a solid foundation for success and continuous improvement, which is something every manufacturing company should strive for.
Below are just a few of the disadvantages of not utilizing work instructions within a manufacturing facility.
Lowered Productivity
Instructions are easily defined as a specific and outlined way to complete a task. Putting workers at the helm of production without giving them the benefit of step-by-step instructions would be similar to hiring a new employee and not providing them with any training on how to do a job.
When employees are allowed, or even encouraged, to figure out how to do things their way, a decrease in productivity is inevitable. They will either have to stop working to ask questions or devise their own methods to complete a task, opening themselves up to the potential for critical errors.
Unsafe Work Environments
Factories are inherently dangerous environments. Heavy machinery and equipment are involved in many manufacturing processes, and when human behavior is factored into this equation, the risk of accidents is multiplied.
Employees are entitled to a safe working environment, and without detailed work instructions that explain the safest and best way to complete a job, workers are put at risk. Statistics show that 15% of workplace injuries in the U.S. occur in the manufacturing sector.
With the high risk of life-altering or even fatal accidents prevalent in factory environments, not having detailed work instructions is irresponsible in the least, and can even be considered criminal in certain situations.
Increased Waste and Defects
Workers that aren’t given the knowledge and guidance to do their jobs correctly are inevitably going to make more mistakes. In the manufacturing industry, mistakes and errors lead to wasted materials, an increase in expensive downtime, and the potential for costly rework. All of these things take a significant bite out of profits and are damaging to a company’s bottom line.
No Way to Measure Performance
Consider this: an employee is tasked with a specific job but given no clear instructions on how to best complete the job. Left to their own devices, they make decisions based on their own experiences and whatever knowledge they may have. Inevitably, they will make a mistake along the way.
Can a manager or company hold that employee accountable for a mistake they didn’t know they were making? Not ethically. But when the same employee is given a set of clear work instructions that detail what to do, and what not to do, then the responsibility of adhering to those instructions is obvious.
Work instructions can help companies monitor the performance and compliance of workers and allow managers and supervisors to gain valuable insights into where knowledge is lacking, and areas where improvements can be made.
Benefits of Using Software for Work Instructions and Procedures?
We’ve underlined the difference between processes and procedures vs. work instructions and explained how successful manufacturing companies need all three in place in a structured and well-communicated way.
However, the future of the manufacturing industry is a digital one. And traditional work instructions are falling to the wayside as companies embrace a better and more efficient way to instruct workers on how to complete complex procedures.
Software that can digitize work instructions is the newest and best way for companies to face the changing landscape of manufacturing.
Companies are turning toward automation and technology as a way to improve their processes and get better results on the plant floor, and digital work instructions can easily integrate into these new and improved methods.
Benefits of Digital Work Instructions:
- Centrally located and easy to access
- Easily revised and updated
- Include detailed visuals, video, and 3D models
- Allow for easy translation into multiple languages
- Integrate easily into already established systems
- Help quickly train and upskill workers
- Capture valuable tribal knowledge
- Allow communication between teams, departments, or facilities
- Assign tasks and track progress
- Capture real-time performance data
- Create checklists for any activity
- Aid in compliance and regulatory standards
- Can be used on multiple platforms, including computers and mobile devices
Using digital work instruction software has become a key component of the goal of continuous improvement. Manufacturing companies should be constantly working to improve every process and procedure. Digital work instructions provide a better, faster, and more effective way for companies to accomplish this.
Dozuki is a leading software choice for companies who want to upgrade and streamline their work instructions. Dozuki is designed to provide the very best way for companies to create, publish, and utilize work instructions for manufacturing companies. But the best part about Dozuki is that it’s much more than that.
Every step of the standard work equation can be quickly and easily outlined, do cumented, and followed up on with Dozuki. Processes, procedures, and instructions are managed centrally so that companies can spend more time and energy on projects that add value and build revenue.
Wrapping Up Final Thoughts
Manufacturing companies face an uphill battle when it comes to success.
Many external factors create challenges within a facility, and internal issues can arise and cause serious disruptions in production. For companies to find long-term success, they must use every tool at their disposal to increase productivity, keep costs low, and create a steady revenue flow.
The processes that make up the manufacturing sector are varied, and clearly defining them is the first step toward a successful outcome. And because there is an endless list of products being produced globally, processes and procedures have been refined and perfected over the decades. And that progress is unlikely to slow down.
Having detailed work instructions is an essential part of any manufacturing process. Most manufacturers understand this fact. But work creating, maintaining, and publishing work instructions represents a large cost of both time and money.
It only makes sense for companies to invest in software that can transform outdated and old-fashioned paper instructions into much more valuable digital versions. Doing so will boost productivity, increase efficiency, and speed-up training.
The use of automation and technology has made vast improvements to the way work is completed on the factory floor. And companies that understand the importance of maintaining a competitive edge will work to stay ahead of these developments.
Using the very best tools to manage processes and procedures vs. work instructions will give companies the advantage they need to stay relevant and build toward long-term success.
Related Posts
View All PostsWhat Makes a Good Digital Work Instruction Software?
When Bob Dylan sang the lyrics, “the times they are a-changin’,” he probably never envisioned what the world would look like just six short decades later. The rise of digital...
Continue ReadingWhy Sharepoint Fails at Knowledge Management
Many industrial businesses rely on generic document management tools, like Microsoft Sharepoint, to store and share files. As a document management strategy, this makes...
Continue Reading5 Ways to Fix the Skills Gap on the Factory Floor
Properly addressing the skills gap takes time. But before you start forming an internal task force or scheduling strategy meetings, consider what impact you can have on the...
Continue Reading