
Book Club: “The Machine That Changed the World”
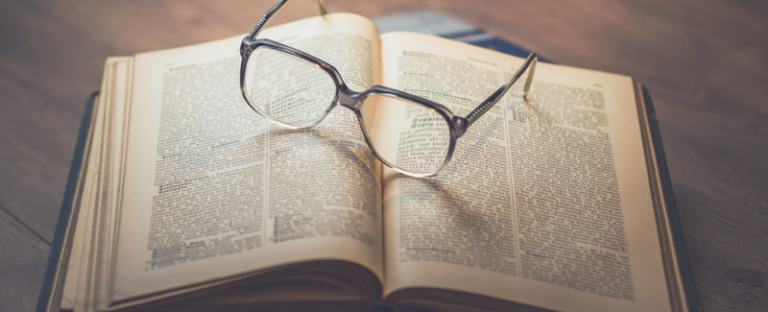
The Dozuki book club is your go-to place for industry books and resources. Our team curates knowledge from industry experts, letting you identify key takeaways and start implementing solutions quickly.
This Month
"The Machine That Changed the World" by James P. Womack is the bestselling book that first articulated the principles of lean production, this management classic was the first book to reveal that Toyota’s lean production system is the basis for its enduring success.
Industries in Transition
Craft Production vs. Mass Production
- Craft Production: highly skilled workers using simple/flexible tools
- Mass Production: narrowly skilled professionals that design products to be made by unskilled workers, using single-purpose machines
- The end result: lower customer cost & standardized products
The Best of Both Worlds: Lean Production
- Constantly seeks perfection
- Zero defects, zero inventory, endless product variety, and declining costs
- Retains: Teams of multi skilled workers, flexible and automated machines
- Avoids: High cost of craft production, rigidity of mass productions
The Origins of Lean Production
Before we look forward, we must look to the past.
Craft Production
Before WWI, craft production was the dominant method for automobile manufacturers.
- Craft production consisted of:
- A highly skilled workforce that progressed through apprenticeships, possessing a wide range of skills
- Decentralized resources
- Centralized workforce
- General purpose machine tools
- Low production volume
Mass Production
The key to Mass Production: “Complete and consistent interchangeability of parts and the simplicity of attaching them to each other.”
- The Model T by Ford Motors
- The first car designed for mass manufacturing
- Advances in machine tools made it possible to work with pre-hardened metals
- Two Key Innovations:
- Perfect part interchangeability - eliminating the need for customization and fitting
- The moving assembly line - each worker was performing a single task, reducing cycle time from 2.3 to 1.19 minutes
The Mass Production Workforce
- Ford perfected the interchangeable worker
- Extreme division of labor
- Ford workers were only focused on completing one, small task
- Everything outside of that domain was not the concern
- Over 50 different language were spoken in factories
- Siloed division of labor meant language barriers weren’t an issue
- Ford took it as a given that his workers wouldn’t volunteer any information on operating conditions [...] much less suggest ways to improve the process.
- Process improvement and reporting fell to the foreman and the new position of the process engineer
- This opened up a whole new range of knowledge workers, but also lead to a minute division of labor that would later cause problems
- Extreme division of labor
"Ford took it as a given that his workers wouldn’t volunteer any
information on operating conditions ... much less suggest ways to improve the process."
Organization
- Ford’s cars were designed, engineered, and produced in Detroit, but assembled in remote locations
- This worked for a standard product, but created problems when specialization was required for different markets
Tools
- Ford reduced setup time by creating machines that could only do one task at a time
- Required minimal training
- Allowed machines to be placed in order of the production process
Product
- The Model T was popular because of it’s low price point and repairability
- Repairability was key for cars in this age, because all cars inevitably broke down
The Rise of Lean Production
The need for lean production was born in Japan because:
- The Japanese markets demanded a wide range of vehicles
- The native workforce required higher pay and was no longer willing to be treated as a “variable cost”
- The post-WWII economy made it impossible to purchase the latest production technology
Enter: Taiichi Ohno
- Taiichi Ohno developed a method at Toyota for changing the molds of metal sheet stamping required to make 300 metal parts stamped using this process
- Western companies didn’t change the molds for months and required a full day to change the mold, Ohno’s methods reduced this time to a matter of minutes
- After promising lifetime employment and raises based on seniority and profitability, employees no longer felt like a disposable resource
- As a result, workers began contributing to improvements and became more invested in the success of the company
- Ohno developed a new way to coordinate part flow with the daily demand using a just-in-time system, now known as ‘Kanban’
- If one part of this large system failed, the entire workflow stopped
"The lean plant has two key features: (1) it transfers the max number of tasks and responsibilities to workers actually adding value, and (2) it has a system for detecting defects that quickly traces every problem to its ultimate cause."
The Elements of Lean Production
“The truly lean plant has two key organizational features: (1) it transfers the maximum number of tasks and responsibilities to those workers actually adding value to the car on the line, and (2) it has in place a system for detecting defects that quickly traces every problem, once discovered, to its ultimate cause.”
The dynamic team of operators who have the knowledge, motivation, and skills to improve processes is what drives a lean factory.
Lean Product Development
During the product development lifecycle, cross-departmental teams in Japan were so connected, they were able to develop machinery and parts for new products while designs were still being finalized, shaving years of the design lifecycle.
Problems in the Mass Production Supply Chain
Suppliers are brought in too late to the design process
- Not enough time to make design improvements
- Suppliers are under pressure to reduce costs from a manufacturer who doesn’t fully understand the product
- Bids are unrealistic, leading to annual cost adjustments that ultimately cost the manufacturer more money
Benefits of the Lean Production Supply Chain
- Suppliers selected on the basis of past performance and relationships, rather than bids
- Lead producers assume that the initial price is a reasonable estimate for the cost plus profits and will continually decline price adjustments
- Suppliers make mutual agreements with producers on a cost reduction curve
- If the cost is reduced below the agreed upon curve, the additional savings go to the supplier
Dealing With Customers
Mass manufacturing practices popularized by Ford set a bad precedent that the production needs came before customer needs.
The Lean Producer and the Consumer
- Distribution is a fully integrated part of the entire production system
- Rather than getting as many products off the distribution lot, lean manufacturers saw that focusing on better product-demand fit, resulted in:
- Better production scheduling (higher efficiency, therefore lower cost)
- Higher level of service
- Higher customer satisfaction
- These producers were driven by the needs of the customer, not the factory
Related Posts
View All PostsBest Practices to Maximize Production Capacity in Manufacturing | 2023
According to the numbers, manufacturing makes up around 12% of the U.S. GDP and provides jobs for 12.984 million Americans, or about 9.6% of all U.S. workers. In other words,...
Continue ReadingLean, Six Sigma, and Quality Management Systems
Six Sigma, Lean, and Quality Management are distinct approaches to reducing waste, defects, and providing value to the customer. With so many approaches to process...
Continue ReadingContinuous Manufacturing: Streamlining Production for A Competitive Edge
Continuous manufacturing (CM) is a production method that has gained a lot of attention in different industries due to its ability to streamline production, enhance profits...
Continue Reading