
How to Perform a Time Observation
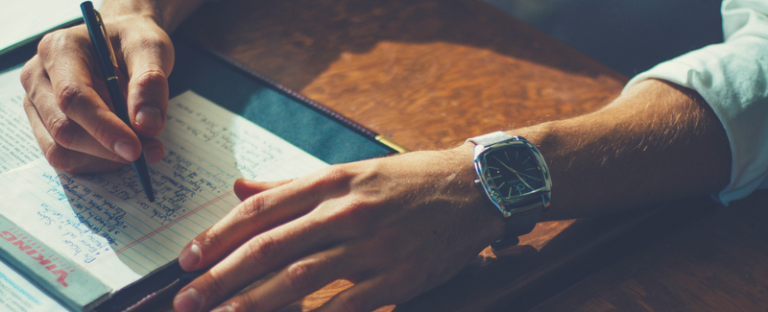
Without Standard Work, documented processes are often not used, or so out of date, that following them could become problematic. Standard Work is the foundation for any continuous improvement or Lean program, and time observations are the starting point. They are the foundation for which improvements are based on.
Time Studies vs. Time Observations
Time observations are a unique way of documenting an entire process, from setup to cleanup, in a format that is comprehensive and objective. Time studies on the other hand, simply record the length of time required to complete certain processes. Additionally, time studies start and stop within each element, while a time observation records the entirety of the process.
Emphasis on the Observation
The key distinction here is that time observations require the observer to go to the Gemba, the place where work is done, in order to document a process as it’s occurring.
Using a manager or someone not directly involved in the process, the observer is focused on recording the various actions with great detail. The emphasis is on the observation, with the time recording as a secondary consideration. This is an important distinction. Cycle times may appear to be efficient, but if you are not attently observing a process, you may not notice that the operator is performing unnecessary work.
5 Steps for a Great Time Observation
In his book, “Standard Work is a Verb,” John Allwood sees time observations as the heart of Standard Work.
“In fact a decent time observation is like a pencil drawn video. It is a running credible record of integrity as to what was happening at the time of the observation.”
A good time observation is something that can be difficult to do. We came up with some actionable tips to help you start making great time observations and begin the process of continual improvement with Standard Work.
1. Be as Objective as Possible
This is a challenge. As humans, it’s impossible to be completely objective. That said, there are a few simple things that you can do to limit bias. For one, don’t converse with the operator once the process has begun.
Speaking with the operator during the process will create bias and the operator may start explaining what they are doing, which is counterproductive to the reasoning behind a time observation. Beforehand, inform them why the time observation is being performed, clarifying that it is not an analysis of employee performance. This helps the operator feel at ease and allow them to focus on doing the work. From there, simply watch and record.
2. Write Clearly and Use Plain English
It sounds straightforward, but in an industry full of acronyms and jargon, it can be easy to get lost in the lingo. Speak plainly about what you’re seeing. The easiest way to achieve this is by writing steps in everyday language. Plain old English.
Ditch the industry jargon and pre-existing knowledge of the operations. The focus is on recording exactly what happens, while it’s happening. Don’t import any background knowledge into the process. This also highlights the importance of objectivity, since prior knowledge is a form of bias.
3. Time the Whole Thing
This is a smaller point, but provides a critical distinction between time observations and time studies. Rather than timing the individual elements, like in a time study, time observations record the entire time it takes to complete the process. This makes every component of the process a part of the time observation.
The steps, or non-value adding periods between elements are also recorded as a part of the process. This forces you to take a hard look at every aspect of a process, focusing on adding value to the customer
4. Observe, Observe, Observe
This is the most challenging component of a great time observation - just observing. It sounds simple, however we have a natural tendency to simplify the information that we receive, because it allows us to process faster. Unfortunately, the purpose of a time observation is to break down the process into individual actions and steps.
For example, “employee then disposes of the plastic material waste,” might sound like an adequate description, however there could be many actions that are implied (or assumed) by the writer. Where is the garbage disposed? Does the employee have to use a dolly to transport the waste? Are gloves necessary for this task? Do plastic bags need to be replaced as a part of this process? Recording exactly what happens is a constant battle against our natural preference to simplify. Learning to accurately record what is happening is a skill that must be continually practiced and maintained.
5. Start Slow, Move Your Way Up
Time observations aren’t easy. We can miss important details, or forget to document a crucial step. Start by observing simple processes first and then work your way to more complex ones. Beginning with observing simple procedures allows you focus on the details, without missing something important or inadvertently simplifying a process.
Once your accurate time observation is completed, it’s time to standardize and start implementing Standard Work to continually improve your processes. Dozuki provides Standard Work software for hundreds of companies that want to use documentation to empower their employees and create a culture of continuous improvement.
Related Posts
View All PostsA Quick 5 Step Guide to Lean Product Development
In the fast-paced world of product research and development, lean methodology can help reduce waste and shorten delivery times. This guide outlines five quick steps to bring...
Continue ReadingOvercoming Manufacturing Lead Time | What Is Lead Time & How To Reduce It?
Manufacturing companies rely on their ability to get products to customers quickly and efficiently. If it’s one thing customers are not, it’s understanding when it comes to...
Continue ReadingBook Club: "The Spirit of Kaizen"
About the Dozuki Book Club: Your go-to place for industry books and resources. Our team works hard to curate knowledge from industry experts, letting you quickly identify key...
Continue Reading