
Identifying Defects: How Root Cause Analysis Will Save Manufacturing
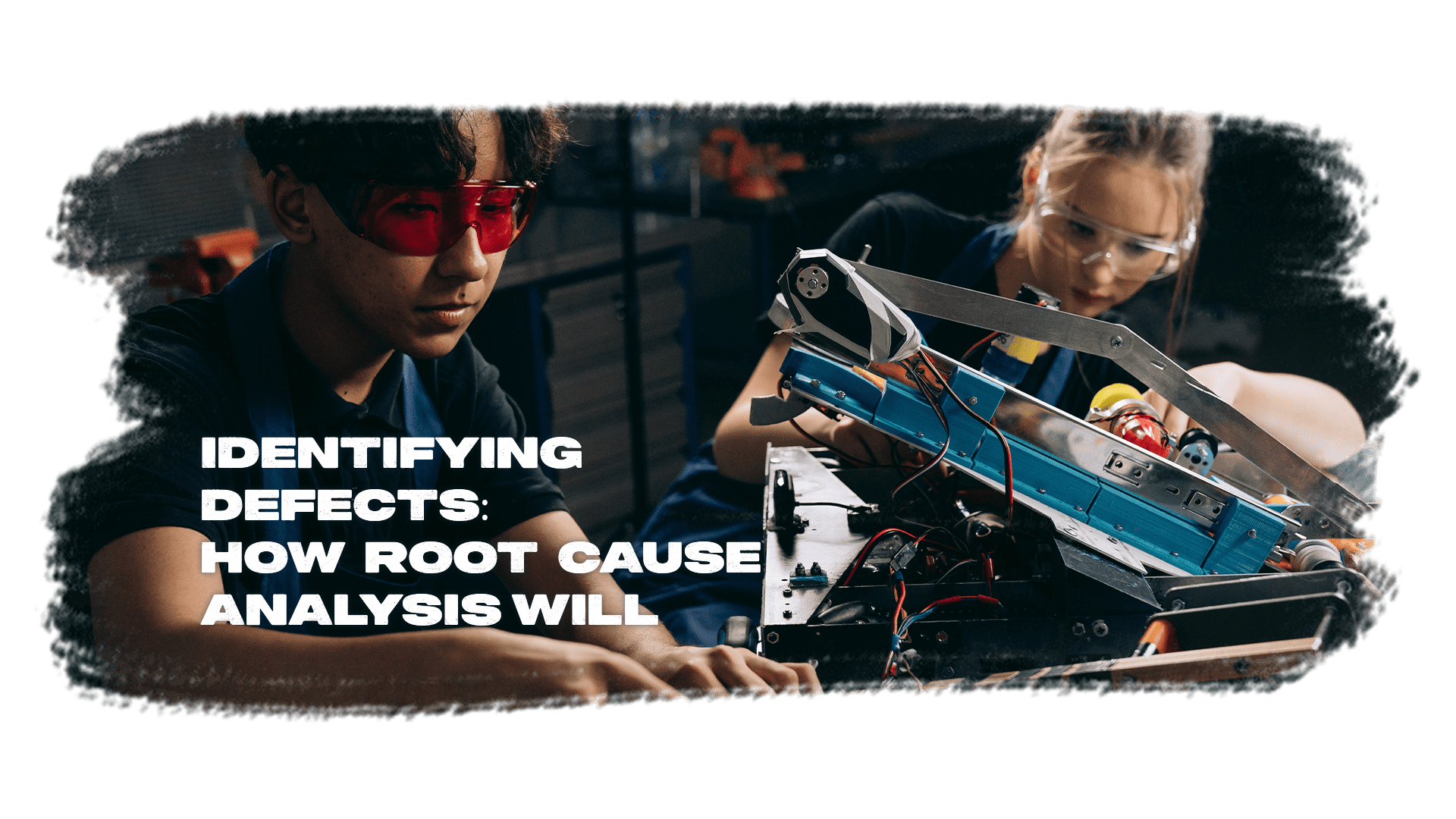
Manufacturing companies work hard to build a lean culture. The never-ending march toward the ideal of perfection through the motto of continuous improvement requires constant vigilance. Part of the process means solving problems when they arise.
Table of Contents
1. The Importance of Identifying Defects
2. Benefits of Root Cause Analysis
4. Root Cause Analysis Methods
5. Tools and Techniques Used in Root Cause Analysis
7. How To Implement RCA in Manufacturing
8. Challenges Manufacturers May Face When Implementing RCA
In manufacturing, the process of problem-solving is of the utmost importance. Unsolved problems can lead to catastrophic results for organizations, including lost revenue and materials, defective products, and even liability for injury to workers or the public.
When we solve problems in our daily lives, we tend to look for solutions to those problems first. But to truly eliminate the problem, it’s necessary to uncover the “root” of that problem. Think of the root as the initial cause of the problem. That’s when a process known as Root Cause Analysis can be helpful.
The American Society for Quality (ASQ) defines Root Cause Analysis, or RCA, as a term that describes a range of approaches, tools, and techniques used to uncover the causes of problems or the root.
A "root cause" is a factor that causes a nonconformance, resulting in processes or results that fall outside predefined expectations.
Manufacturers look to RCA to pinpoint the root cause and then work to eliminate it through process improvement. RCA can be used in a general problem-solving capacity or as a tool to precisely identify the root cause of a problem.
This article will define the uses for RCA, give some examples of RCA in practice, and go over some of the different tools and methods manufacturers can use to solve problems in real-time.
The Importance of Identifying Defects
Problems are, well, problematic. But for manufacturers, problems in processing can lead to defective products. And defective products cause problems for both the manufacturers in the form of lost revenue, lowered productivity, and risk of injury to workers, but also to consumers.
When defective products go unnoticed and are allowed to reach consumers, manufacturers can be held liable for potential illness or injury caused by those products.
Root cause analysis is a way for manufacturers to fully solve problems in processing rather than band-aid the problem with temporary solutions.
And it's one of the most important things manufacturers can do to protect themselves and the public from defective products.
Protecting Consumers
In 2022, more than 1.5 billion units of products from various manufacturing industries were recalled, including food, drugs, medical devices, automobiles, and other consumer goods. Defective products reaching consumers can cause injury, illness, or even death.
There are laws and regulations in place that are designed to protect the public from manufacturers who allow defective products to reach consumers, meaning that those companies are liable for the harm those products cause to people or even the potential for harm.
Protecting the Organization
A failure to address problems within a manufacturing facility can lead to a waterfall of negative consequences. It starts with the product itself. A faulty process or poorly maintained machinery can lead to defective output. And the longer that problem is allowed to continue, the more money organizations lose.
Lost revenue, a drop in productivity, wasted materials, and lost time is the tangible consequences of unaddressed problems. But there are other consequences of a not-so-tangible nature. Opening the organization to liability is a big one, but so is a drop in the quality of products. Lowered quality and recalls can lead to a damaged reputation, decreased public trust, and a reduced chance of remaining competitive in a tight market.
Benefits of Root Cause Analysis
Besides the importance of problem-solving to protect consumers and the organizations themselves, manufacturers benefit from using root cause analysis to solve those problems in other ways.
Discovering the root cause of an issue is the most efficient way to solve that problem. Here are a few of the benefits organizations can gain by implementing RCA.
Preventing Recurring Failures
A problem remains a problem until the root cause is discovered and remedied. Solving a problem without proper analysis of the originating factor that caused that problem could lead to ineffective solutions focusing on the wrong strategy. What often results is a reoccurrence of the problem.
Enhancing System and Process Reliability
In the vein of continuous improvement, RCA serves to improve and enhance systems and processes by creating scenarios where permanent improvements are implemented.
Again, a bandage for a problem might eliminate that problem temporarily. However, RCA strives to go a step further by focusing on the original cause and making changes to the system that prevent that problem from occurring again.
Improved Quality
Problems in manufacturing usually result in products that fall outside the acceptable or expected quality. Defects can be large and noticeable or small and hard to spot.
Either way, the result is a drop in quality, which manufacturers need to avoid. RCA is a way to catch problems and implement solutions that will lead to a higher quality of products.
Greater Efficiency
Solving problems the wrong way usually means circling back to those problems repeatedly. Using RCA to discover the root of the problem and focusing on that factor is the best way to guarantee the problem doesn’t reoccur.
This means workers can get back to producing faster and with fewer opportunities for defects in the future.
Greater Customer Satisfaction and Safety
Keeping defective products from reaching consumers will keep the public safe, improve a company's reputation, and ensure customers receive the highest quality products.
Saves Time, Money, and Effort
Ineffective problem-solving is a waste-maker. It leads to wasted materials, defective products, rework, and reprocessing. And it causes a snowball effect, where one problem leads to another. The result is a time, revenue, productivity, and efficiency loss.
Fosters a Positive Culture of Collaboration
When teams use RCA, they must work together to solve problems. This allows for autonomy and teamwork, as employees provide insight into problems and work together to create and implement solutions.
This type of culture benefits organizations that strive for continuous improvement and fosters an environment of positivity and possibility.
Types of Root Causes
In general, root cause analysis uncovers three fundamental factors contributing to a problem. These three types of root causes are:
- Physical Causes
- Human Causes
- Organizational Causes
These root causes can contribute to a problem individually or in conjunction with one another. Sometimes, one cause can lead to another, but the point of RCA is to work backward and uncover the original cause of a problem.
Let’s look at some examples of each type of root cause.
Physical Causes
A physical root cause is a factor linked to a tangible object. It might be an equipment failure, like a piece of machinery not working correctly. It might also be a problem related to raw materials or some other tangible source.
Human Causes
A failure that occurs during human interaction is considered a human root cause. Incorrect actions, bad decisions, and human error are all human causes. And human root causes are a good example of one problem leading to another. For example, a worker who fails to perform maintenance procedures correctly could result in a physical problem when a piece of machinery fails.
Organizational Causes
Organizational causes are problems that occur because of a failure in the system of processes established by the organization. These systems provide a framework for the processing procedure, and if a failure occurs somewhere during the establishment of these systems, it will likely cause other problems down the line.
Root Cause Analysis Methods
Root cause analysis is a multi-step process. These steps have several goals. First, to uncover the root cause.
Second, to work out a solution to the problem by addressing the root cause directly.
Third, implementation of that solution. A fourth goal could be included: follow-up observations and testing to ensure the problem has been solved successfully.
The ASQ has outlined six steps organizations should follow to perform an effective root cause analysis. They are:
- Define the event that took place
The work of RCA is usually conducted by small, dedicated groups. These individuals are tasked with working through the steps of RCA and may consult with a Subject Matter Expert (SME) to help them define the problem.
The SME may be someone involved with the organization who has specific knowledge of a process or department or an expert in a specific field brought in from outside the organization.
- Finding the causes of the event
Finding the cause, or causes, typically requires gathering information from those with knowledge of the event or gathering data relevant to the event. This data helps team members understand the factors that contributed to the event and understand if one cause may have led to further problems.
- Pinpointing the root cause
Pinpointing the root cause of an event is the key to RCA. Team members working through a problem have several established methods to help them uncover the root cause (more on those coming up). But the key is understanding how to work a problem backward – until you reach the originating cause of the problem.
- Finding solutions
Finding the cause of a problem does little good without a follow-up effort to remedy that problem. RCA allows for more efficient problem-solving because it’s easier to work through potential solutions if you understand what led to the event in the first place.
This prevents problems from recurring and eliminates wasted effort spent fixing the wrong part of a problem.
- Implementing the solutions
Once an effective solution that solves the root cause of a problem has been established, it’s time to implement the solutions. This might mean a change in materials or suppliers, changes in machinery or processes, changes in design, or even retraining of personnel.
- Verifying the effectiveness of the solutions
Once changes have been implemented, completing the process requires further analysis to ensure the problem has been solved at the root cause. Further testing, data collection, and analysis can verify that the improvements or changes have truly fixed the problem and eliminated any future chance of the problem reoccurring.
Tools and Techniques Used in Root Cause Analysis
Root cause analysis is made easier using targeted methods or tools. These tools are designed to help organize the data involved with an event in a way that makes it easier to discover the root cause. Or in other words, they help point the way to the root cause by defining the most reasonable path to that root cause and eliminating the distractions.
These methods also allow for greater efficiency in creating and implementing a solution. Organizing data in a clear and easy-to-visualize format makes it easier to understand and apply it in a real-time setting. Of course, no solution is deemed complete without proper implementation and follow-up testing.
Pareto Chart
A Pareto chart is a histogram– a bar chart and a line chart combined into one. A Pareto chart is used to demonstrate an event's frequency and the cost, or significance, of those events concerning that frequency.
Pareto charts are based on the 80/20 rule, which states that 20% of inputs drive 80% of results. Seeing how the frequency of an event correlates with other factors can help identify the significance of the event and its direct results.
5 Whys
Think of the 5 Whys like every toddler you’ve ever met; the ones who ask a series of "why" questions repeatedly, always seeking more knowledge. Asking “why” about an event helps uncover the cause of that event. But instead of stopping there, continuing to ask “why” is an effective way of working a problem in reverse until you reach the root cause.
Fishbone Diagram
A Fishbone Diagram is sometimes also called a cause-and-effect or Ishikawa diagram. It helps organize sub-causes by type, making it easier to see where patterns lie. The fishbone diagram model uses the “6Ms” to categorize sub-causes. Those 6Ms are:
- Man
- Machine
- Methods
- Materials
- Measurement
- Mother Nature (Environment)
Categorizing sub-causes into these categories makes it easier to see which is the most probable root cause through organization and pattern recognition.
Scatter Diagram
Also known as a scatter plot, this method of RCA uses a graph to plot out the values of two separate variables, the cause and the effect. This method is also effective in identifying patterns. Wherever the plots on the diagram are of the highest concentration points to a correlation.
Failure Mode and Effect Analysis (FMEA)
The FMEA method of RCA focuses more on identifying problems before they occur, which can be extremely beneficial for manufacturers. It can help organizations plan for a failure they know will happen and determine which problems require attention based on the severity of the outcome.
The FMEA method is a chart that helps categorize potential failures based on their occurrence, severity, and detection rate. These three factors are used to calculate a risk priority number or RPN.
Case Studies
Manufacturers worldwide use root cause analysis to solve problems and improve their organization. So, what does RCA look like when applied to real-world settings? And does it work to uncover the root cause of a problem? Let’s look at an example of RCA in action.
A275 and The Kverneland Group Klepp
The Kverneland Group Klepp is a manufacturing company that experienced a problem with one of its units. This unit, A275, was experiencing excessive downtime (a productivity killer for manufacturing companies).
This significant problem needed a solution. At the same time, the manufacturing company was looking to establish a better framework for solving problems - one that was specific to their facility, machinery, and processes.
They assembled a team to conduct a root cause analysis to meet both goals. It started with establishing the problem – too much downtime. Then they gathered data, including conversations with key personnel and an in-depth examination of their maintenance database.
Through RCA methods, they established that the root cause of the problem was a lack of a feedback system between two systems inside a sub-unit of A275. They were able to use this information to create a solution.
Then they implemented and tested that solution and used the experience to create a new RCA framework that worked better for their organization. In effect, they saved time, created a system themselves time,their team could use more effectively going forward.
How To Implement RCA in Manufacturing
Understanding root cause analysis and its methods is the first step toward using it effectively. But implementing it effectively in real-time settings requires some planning and strategy.
Here are some tips for using RCA in a manufacturing setting correctly.
Establish Processes and Systems
Every manufacturing facility works within an individual framework, depending on the specifics of its processing systems and needs. Because of this, a generalized approach to RCA might not be the most effective.
Instead, teams should seek to create RCA systems that are specific to their facility and work best for the organization's needs. This might mean establishing a team to create and test that system for the best result.
Create Standardized Work Documents
Just like any process within a manufacturing facility, RCA is a process unto itself. Best practices, standard operating procedures, operational checklists, rules, and requirements should be created and used for training and implementation to keep everyone on the same page.
Training
Team members should be trained in the practices of procedures of the specific RCA process established for the facility. No new system will operate effectively without team members being allowed to learn its ins and outs and practice using it in real-time.
Follow-up and Testing
Using RCA to discover the root cause of a problem is half the battle. The most important aspect of RCA is using it effectively to create solutions to those problems and then implementing those solutions.
This might require further training of employees, follow-up testing and analysis, updating SOPs, and more to ensure that processes are permanently improved going forward.
Document
Employees tasked with RCA should create documentation outlining their experiences, including details about the event, data collected regarding the event, steps taken, methods used to uncover the root, solutions implemented, and their effectiveness, etc.
This keeps employees on task, guarantees they are using RCA effectively by following the guidelines and can be used to help future RCA teams learn and improve upon the process.
Challenges Manufacturers May Face When Implementing RCA
Every new system will face challenges and setbacks. The same is true for root cause analysis. And because every organization and facility is unique in its framework, these challenges may be just as individual. But organizations make common missteps that can be easily avoided – if you know what to look for. Here are some of the most frequently encountered challenges for RCA organizations.
Assigning Blame
RCA is designed to help organizations focus on the right causal factor instead of putting time and energy into ineffective solutions. Focusing on assigning blame for a problem is not helpful. Instead, companies should focus on the solutions to a specific problem.
Focusing on Failure Rather Than Success
RCA is intended to solve problems and address failures in the system. But we cannot overstate the importance of focusing on the success created by the process rather than the failure itself.
Key Performance Indicators (KPIs) are an effective way to measure the results of a successful correction to a problem. Tracking KPIs can point out places where RCA improved operations, help team members understand the effects of their actions, and build positivity within the organization.
Failure to Implement Corrective Solutions
Root cause analysis is ineffective without a proper focus on the solution to the problem, not the problem itself. It is a two-fold process, and the benefit of RCA is helping team members focus on the right solution to a problem. Implementing corrective actions to solve that problem is the only way to make RCA successful.
A Lack of Training and Support
The employees and leadership teams work together to make an organization run successfully. But part of that process is proper training and support. That means ensuring teams understand how to use RCA effectively and supporting them via time, effort, oversight, and praise throughout the process.
Final Thoughts
Root cause analysis is one of the most useful tools for manufacturing companies. Striving for a lean manufacturing environment and reaching for that ideal of continuous improvement requires seeking out potential problems and implementing solutions – or finding a way to do things better.
RCA has a great potential impact on both the organization and consumers. It holds immense potential for manufacturers by allowing for a systematic approach to problem-solving and helps companies uncover the underlying causes of defects faster and more efficiently.
Addressing defects within a manufacturing facility helps protect the organization and the consumers who purchase and use the products. Using RCA within an effective framework of problem-solving and solution implementation can help organizations be more efficient and more productive. It improves the reliability of the processing systems, creates a higher quality result and improves customer satisfaction in the end. Keeping customers happy and safe while boosting productivity and efficiency is the key to success for manufacturers.
Related Posts
View All PostsStreamlining Production: How Lean Manufacturing Can Revolutionize Your Business
Manufacturing is a delicate process. So many moving parts must come together just right if the aim is to produce goods of the highest quality in the most cost-effective way...
Continue ReadingHow To Reduce Defects in Manufacturing in 2022
Product defects are a pain at any manufacturing company. When all the time, energy, and money that is spent to produce a product is wasted due to defects in the final...
Continue ReadingThe Most Common 8 Wastes of Lean Manufacturing & How to Manage Resources
Manufacturing is all about making the highest quality products at the lowest cost. Reaching that goal means searching for and eliminating causes of wasted time, wasted...
Continue Reading