
Quality Assurance in Manufacturing: An In-Depth Guide to Achieve Customer Confidence
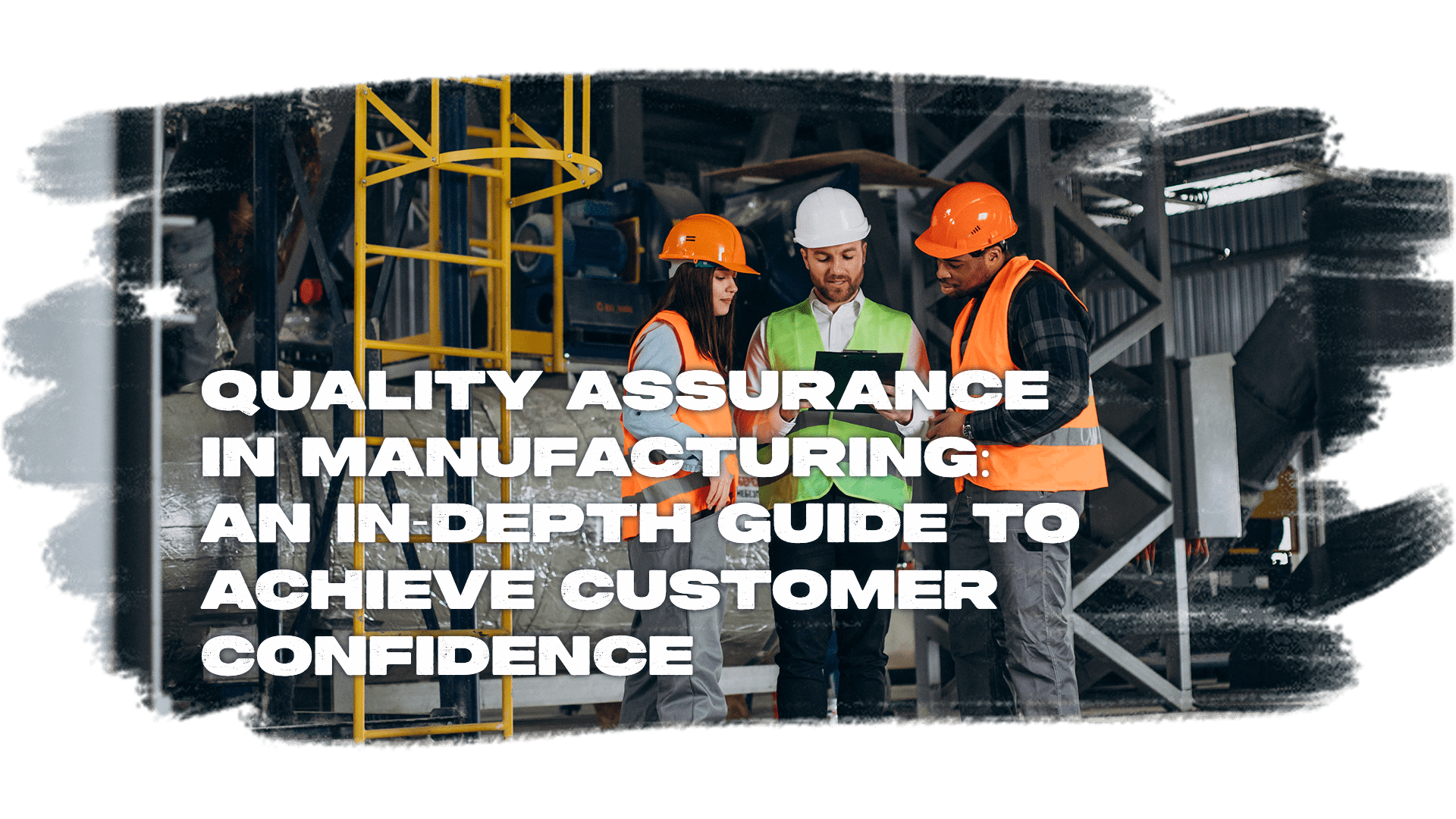
It’s time to talk about quality. In this industry, quality is everything, and competition between manufacturers is fierce.
Table of Content
1. Key Principles of Quality Assurance
2. Quality Control Vs. Quality Assurance
5. Risk Management & Prevention
6. Testing & Inspection Techniques
7. Statistical Process Control
8. Employee Training & Skill Development
Manufacturing companies are telling customers that their product is created with quality in mind. Break that promise and customers are not likely to be forgiving.
Want proof?
Check out this list of some of the biggest payouts from manufacturing companies that faced product liability lawsuits in 2022. You will find billions of dollars in payouts that manufacturers made to consumers because of poor-quality products.
Sometimes that failure is in the design itself. Sometimes it results from poor materials or construction. But in the end, it all comes down to a failure to establish effective quality assurance in manufacturing.
Quality assurance involves creating processes, protocols, and procedures designed to monitor, test, and inspect manufacturing processes.
The goal is to ensure that production meets the specified requirements for each unit produced every time.
A well-designed quality assurance plan can improve process control and company culture while reducing costs.
This article deals with quality assurance – what it is, why it matters, and how to achieve it.
Key Principles of Quality Assurance
Quality assurance in manufacturing is sometimes hard to define because it is a far-reaching concept and looks different for each organization.
The industry typically refers to the ISO 9000, or the International Organization for Standardization, an international standard for quality management systems in the manufacturing industry.
Quality assurance is all about systems and the principles that help shape those systems.
These principles are fundamental to creating effective organizational quality management. They provide framework organizations can use to ensure they approach production with quality in mind.
Building an organization around these principles proves a commitment to strive for customer satisfaction and ultimately achieve long-term success.
The Principles of Quality
Customer Focus – Putting the customer first is a goal for any business. But what does that mean exactly? Well, a customer has expectations. They expect that any company they give their hard-earned money to is doing their due diligence to ensure they're receiving value in exchange.
Customer focus requires that manufacturers use high-quality materials, carefully planned processes, stringent testing, and careful consideration of things like safety.
Leadership – Leadership is a principle of quality assurance because it’s the leaders who steer an organization. A company culture centered around the customer and quality must start from the top.
Engagement – Equal in importance to the leaders of an organization are the employees who do the actual work. And when it comes to quality, these employees are the ones who often dictate the outcome. Getting everyone engaged and on board is the only way to ensure quality is a focus.
Process Approach - Manufacturing relies on processes, one often reliant on others, in an unbreakable chain. Building processes with quality at the forefront is a requirement of quality assurance.
Continuous Improvement – Improvements in the manufacturing industry never stop. Continuous improvement is a concept that manufacturers use to motivate team members to constantly look for ways to end up with better, higher-quality results.
Evidence-Based Decision Making – How does one improve quality results? By relying on hard data. Guesswork has given way to statistical analysis and evidenced-based decision-making. What results is a better likelihood of making the right decisions for the customer?
Relationship Management – We can’t leave out the importance of relationship building in the quality management discussion. From suppliers to investors, and yes, even the bankers – everyone involved in the process contributes and is affected by the outcome, and so should be considered in quality assurance.
Quality Control Vs. Quality Assurance
Quality assurance in manufacturing requires a systematic approach to the overarching goal of quality management.
Both quality assurance and quality control fall under the umbrella of quality management. These terms represent two different yet intertwined processes and are often misapplied.
Quality Assurance
Quality assurance is about implementing systems to support the highest-possible quality outcome. It focuses on ensuring the right tools and processes are in place to meet pre-specified quality requirements.
Quality Control
Quality control differs from quality assurance in its specific applications. Quality control safeguards against a negative outcome in quality assurance systems. So, in essence, quality control is a tool of quality assurance. It focuses on fulfilling specific quality requirements through things like inspection and testing.
Proactive vs. Reactive
Quality assurance and control are integral to an organization's ability to produce a high-quality product. What differs between the two is the approach they take toward solutions.
QA is a proactive tool designed to ensure the right systems and processes are in place to guarantee a quality outcome. It touches every aspect of manufacturing, from the initial design to suppliers and materials, down to specific production processes.
QC is more of a reactive tool designed to test the outcome of the quality assurance systems. When a deviation from expectations is discovered, companies can react and improve those systems where they are needed. However, a careful understanding of both QA and QC is crucial for organizations seeking the highest-quality outcome.
Quality Assurance Process
According to the American Society for Quality, most organizations experience quality-related costs of between 15-20% of their revenue, with the average cost at a successful company being around 15% and as high as 40% at the top of the scale.
To ensure these dollars are well spent, organizations must ensure that manufacturing quality assurance processes are efficient and effective. To do so, many organizations follow a map called PDCA, which stands for Plan, Do, Check, Act.
This process represents a never-ending cycle that drives the quality management system. Each step leads into the next, with the eventual outcome hopefully being a higher-quality product. However, with continuous improvement leading the way, the PDCA cycle never truly ends.
Using it effectively will ensure that products are manufactured consistently and up to the standards. The PDCA also helps highlight and prevent issues before they occur, saving companies stacks of cash and customers.
PDCA – The QA Process in Action
- Plan – Creating the objective or goal of the process.
- Do – Developing the process with the goal in mind and testing the outcome of the process to ensure that goal is met.
- Check – QA team monitors the process in action to determine whether the outcome meets the original goal or objective. Deviations from expectations or failures are noted.
- Act – QA team makes any necessary changes or improvements to the process to ensure the result is a product that meets pre-determined standards.
Defining Quality Standards
A “quality product” is sometimes a vague moniker, especially in an industry like manufacturing. Organizations need more than just a common denominator regarding quality and quality assurance in manufacturing. They need specifics – measurements, data, testing, and qualifying conditions that must be met to earn that descriptor of “quality.”
Setting clear quality standards is of the utmost importance for virtually any industry. This is especially true from the customer’s perspective. Every company is likely making a similar claim, telling the customer that their products are superior and “high-quality.”
But many consumers want peace of mind, and organizations must set clearly defined parameters for what quality means to them. And they need to base those parameters on the expectations of the industry and their customers.
Setting clearly defined quality standards benefits an organization in many ways, both internally and externally.
For example, quality standards provide
- A framework that drives a positive company culture
- A set of clearly defined expectations for employees
- Improved communication with suppliers and investors
- Increased customer satisfaction and loyalty
- Improved company reputation
- Reduced costs
- A greater competitive advantage
Quality standards will differ depending on the specific industry, product, and even the customer base itself. But the most important thing to remember is that quality is paramount to the reputation of an organization and the loyalty of its customers.
When a manufacturer operates with a set of clear and pre-determined quality standards already in place from the outset, and everyone on the field understands those expectations, outcomes will improve.
Risk Management & Prevention
Risk management is a commonplace topic in any business. Quality assurance in manufacturing is another topic that gets its fair share of attention. Many organizations miss the opportunity to merge the two concepts for a better result.
Reducing risks within the manufacturing industry is likely one of the most crucial tasks organizations face today. Manufacturing can be hazardous to workers, consumers, and the environment.
With so many risks already in play in the industry, is there room for quality assurance in the conversation? Absolutely. And there needs to be an understanding that the two are intertwined is essential.
Manufacturers must take a proactive approach to risk management. We already mentioned that quality assurance requires a proactive approach as well.
Ignoring one or the other will result in a poor outcome on both fronts – a higher-risk environment and a poor-quality outcome.
Organizations can follow four basic steps when building a risk management or business continuity plan.
Implementing these steps can help manufacturers take the necessary proactive strategy, identify potential root causes of risks, and prevent or lessen the probability of future problems.
These steps involve:
1. Risk Assessment
Performing a risk assessment can be a wide-reaching task or a very targeted and specific one. And in truth, organizations need to be doing both. Risk assessments are useful tools for determining the probability of a scenario unfolding and will look different for every organization.
For example, companies with coastline holdings are at a higher risk for things like floods and hurricanes. Manufacturers who deal with flammable or combustible materials are at a higher risk for fires and explosions.
And companies that deal with bio-chemicals or other potentially hazardous materials face a whole new set of problems.
Apart from these types of uncontrollable risks are more commonplace ones, like the risk of injury on the job from poor maintenance, equipment failure, or even workplace violence.
These are potential scenarios that can lead to major and costly problems for an organization. Identifying them is the first step to addressing them.
2. Incident Management & Recovery Planning
Each identified risk requires a specific plan of action. The next step in risk management is to develop that plan down to the most minute details.
Who does what and how? Who do they call? Where are the emergency response materials and phone numbers? What’s the escape plan in the event of a weather emergency or fire?
This step aims to create a fail-proof plan that protects employees first and assets second.
3. Internal Audit Checks
No risk management or emergency plan should be created and then forgotten about. This is an area where manufacturers cannot afford to be lax. Careful auditing of incident management and recovery plans should occur regularly.
Plans should be updated to include new information, and employees should be trained and retrained in their execution.
4. Test Exercises and Scenarios
This brings us to our next step, testing the emergency plan through orchestrated exercises. Employees amid a crisis may panic. Don’t rely on their ability to think clearly and act decisively without practice. Companies provide on-the-job training for virtually every other task. Emergency response should be no different.
Testing & Inspection Techniques
Let’s talk about some numbers. We’ve discussed exactly how much revenue manufacturers spend on quality management practices. But what often gets overlooked is the cost of poor quality. Many organizations cite their cost of poor quality, or COPQ, as around 5%. However, according to Quality Digest, the reality is that this number is likely much higher, and for some manufacturing companies it can be as high as 30%.
When it comes to stopping poor-quality outcomes from occurring or catching poor-quality products before reaching consumers, testing and inspection are the best available tools .
But wait. Don’t testing and inspection fall under the definition of quality control? The answer is yes. But let's not forget that QC is one of the tools organizations can use to improve quality assurance in manufacturing.
Product inspections and testing happen at all stages of product development and production. Quality control is more of a reactive tool designed to catch potential flaws and failures in the outcome, but testing isn’t relegated to only post-production.
Inspections and testing help prevent product recalls, a scenario that can cost organizations more than dollars spent in costly litigation but their entire reputation. And quality testing ensures that only the highest-quality products make their way into the hands of consumers.
Statistical Process Control
Another tool that can help improve quality assurance in manufacturing is data. Manufacturing organizations today have access to more data than they ever have before in the history of the industry, thanks to technology. By collecting and evaluating that data, businesses can:
- Better create, manage, and improve processes
- Ensure the production of consistent, high-quality products
- Pinpoint potential problems before they occur
- Measure results more effectively
- Make better decisions
- Reduce costs
- Increase customer satisfaction
Statistics & Quality Assurance
Statistical process control (SPC) uses technology to collect and analyze data and put it to better use. By applying statistical process control, manufacturers have the best possible chance of monitoring and controlling quality. It only makes sense that access to accurate data and a better way to analyze it would lead to a better outcome.
SPC allows for a more proactive approach to quality management by providing a looking glass for organizations. Using real-time data, companies can spot potential problems before they result in poor-quality outcomes. The result is a higher quality product and another step toward continuous improvement.
Statistical process control involves the use of tools to harness and analyze data.
Some of these tools include:
- Cause-and-effect diagrams
- Histograms
- Pareto charts
- Check sheets
- Scatter diagrams
- Control charts
- Stratification
- Defect maps
- Event logs
- Flow charts
- Randomization
- Sample size determination
Employee Training & Skill Development
Every product that comes off the line passes through the hands of the employees. And the amount of attention, training, and development that organizations dedicate to those employees plays a significant role in their ability to provide high-quality products to their customers.
In an industry that pulled in over $6 trillion in revenue in the United States in 2022, the number of employees working to build the products consumers use daily is substantial. Manufacturers make an enormous investment in their people, and rightly so. Employees can make or break a business.
Hiring in today's labor environment is difficult and costly, as is high turnover and poorly motivated employees. But the reality is that the fault of this situation lies directly with the organization itself.
It’s the company’s job to ensure workers are given the tools they need to succeed, including proper onboarding, training, and opportunities to develop. And it includes a clear understanding of the importance of quality.
The benefits of investing in employee training programs are many and include:
Improved Productivity & Profitability
It’s no secret that employee training boosts productivity and profitability. A well-trained employee knows their job inside and out, is less likely to make costly mistakes, and can identify issues within the manufacturing process. This leads to less downtime and waste reduction.
Improved Safety & Reduced Risk
A well-trained employee has the essential skills to operate machinery, work efficiently, and follow safety protocols. This leads to fewer accidents and a better ability to remain productive.
Improved Culture & Engagement
A well-trained employee is given the tools they need to be successful and understand the overall vision of the organization. Employees provided with training are happier, more well-adjusted, and more willing to pull for the company goals. And a smart organization puts quality at the forefront of that training.
Final Thoughts
Quality assurance in manufacturing is a topic that gets much attention but maybe not enough initiative. It’s easy to talk about quality. But as they say, companies need to walk the walk, not just talk the talk.
Consumer confidence is a fickle thing today. It only takes one mistake for a well-trusted and highly reputable company to become the exact opposite in the eyes of the public. Earning the trust and loyalty of customers is hard enough without having to fight your back from bad publicity.
Organizations can ensure quality requirements are met and exceeded by implementing effective quality assurance practices.
The result of an established and well-communicated quality assurance system is improved process control, reduced costs, and an increase in customer satisfaction. In other words, quality assurance provides the recipe that manufacturing organizations need to be successful.
Related Posts
View All PostsHow To Reduce Defects in Manufacturing in 2022
Product defects are a pain at any manufacturing company. When all the time, energy, and money that is spent to produce a product is wasted due to defects in the final...
Continue Reading5 Ways To Improve Quality Control in Manufacturing
In manufacturing, quality is everything. Businesses need to focus on creating products that are high quality enough to meet or exceed the customer's needs if they want to be...
Continue ReadingContinuous Manufacturing: Streamlining Production for A Competitive Edge
Continuous manufacturing (CM) is a production method that has gained a lot of attention in different industries due to its ability to streamline production, enhance profits...
Continue Reading