
11 Benefits of Standard Work
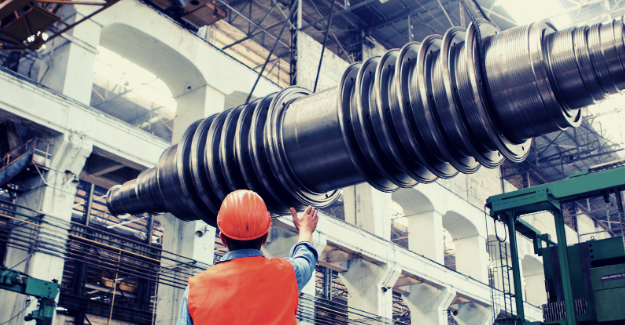
Taiichi Ohno, a founder of the Toyota Production System (TPS), had this to say about Standard Work, “without standards, there can be no Kaizen.” As the foundation for all lean, six sigma, and continuous improvement efforts, the benefits of Standard Work are endless. Ohno's wisdom speaks volumes to the importance of Standard Work, yet many companies aren’t fully practicing it.
Whether you’re in manufacturing, or any other industry, the rewards are universal. See below for the 11 largest benefits of implementing Standard Work.
1. Make Waste More Visible
Illustrate process inefficiencies and allow wasteful activities to surface.
This shifts the focus from placing blame on human errors, to a more positive culture of process improvement and preventative, risk-based thinking. As improving the process becomes the focus, employees are more empowered to think critically about how they can be involved.
2. Train Employees More Effectively
Learning new processes often relies on one-on-one job-shadowing and apprenticeship programs, which are resource intensive and demand the time of more experienced employees. Standard Work helps new employees understand processes quickly and allows them to be less reliant on in-person training. With each task being documented to an approved standard, getting new employees up to speed no longer varies from trainer to trainer.
"If you think of standardization as not the best that you know today, but as that which is to be improved tomorrow; you get somewhere."
- Henry Ford
3. Eliminate Tribal Knowledge
When information is only known by an individual or team, best practices can’t be communicated effectively, making companies reliant on a handful of experienced workers to share important information (“tribal knowledge”). Standard Work allows companies to unleash this information and share it with all employees, reducing the strain of employee attrition.
4. Reduce Defects and Process Variation
Verifying that employees are consistently adhering to procedures is nearly impossible without practicing set standards. Standard Work reduces variation and minimizes defects by creating a universal standard that employees actively engage with, giving them a clear understanding of where their actions deviate from the set process. These easy-to-follow instructions improve employee comprehension and retention of procedural information.
5. Increase Agility and Scale Faster
If done properly, you can rely on your Standard Work to scale procedures and train new employees quickly; freeing up valuable resources to focus on growing your business. Standards provide a base for improvement and take tribal knowledge from the minds of a few employees and turn it into a company asset by being easily shared with new employees. Standard Work enables companies to scale and get the same results from hundreds of people, hundreds of times.
6. Streamline Problem Solving & Process Improvement
One of the most common obstacles teams encounter when problem solving is a mixed understanding of the current process state. Without standards, teams do not have an agreement on the best way to produce the intended result. Standard Work gives everyone an understanding of how improvements affect the workflow in other, related processes.
7. Improve Morale and Promote Innovation
In order for continuous improvement to work, employees need to be provided the proper opportunity and setting to share ideas. Standard Work contextualizes process improvement ideas by creating a baseline for how feedback is given, assessed, and implemented. When employees know that feedback is taken seriously, reducing waste becomes an opportunity to be an insightful contributor.
"Without a standard, there is no logical basis for making a decision or taking action"
- Joseph M. Juran
8. Reduce Scrap and Rework Waste
When the wrong parts are ordered or engineering design changes aren’t communicated to the assembly floor, scrap and rework pile up. Standard Work prevents scrap by giving an accurate account of the materials needed to maintain proper workflows. This way, when processes are altered or changed, the resulting effects can be predicted and prepared for, preventing costly rework.
9. Lower Operational Costs
Standard Work allows organizations to distribute resources more evenly by providing an accurate view of process flow and efficiency. By standardizing procedures, you can assess where bottlenecks exist and clearly define the minimum work in progress (WIP) to maintain proper flow.
10. Increase Customer Satisfaction
When process variation is reduced, customer satisfaction goes up in tandem. Customers will see the benefits of Standard Work via a higher and more consistent product quality delivered by the process improvements standardization has generated. When work is done according to approved standards, customers get what they expect and quality remains the focus.
11. A Chance to Use Dozuki
Dozuki is built for companies to improve their people, processes, and communication. Our goal is to make Standard Work an industry standard by providing companies with the tools and resources they need to implement and sustain standards throughout their organization.
Related Posts
View All PostsWhat's Wrong with Standard Work?
66% of companies fail in their attempts at Standard Work. This begs the question - what’s wrong with Standard Work? How can a seemingly simple methodology be so challenging...
Continue ReadingNavigating Processes: Standard Work vs. Work Instructions
The manufacturing industry is a professional arena with an overwhelming variety of industry terms and acronyms. We’ve tried to make a list of the most common Lean terms...
Continue ReadingManage Workforce Training with Dozuki Courses
At Dozuki, we’ve made it our mission to make Standard Work an industry standard. We envision documented standards and worker knowledge continuously improving alongside one...
Continue Reading