
What's Wrong with Standard Work?
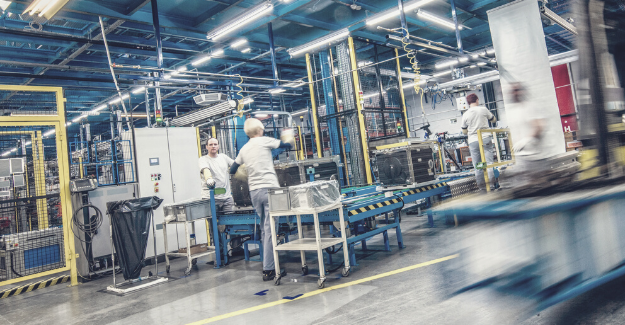
66% of companies fail in their attempts at Standard Work.
This begs the question - what’s wrong with Standard Work?
How can a seemingly simple methodology be so challenging to practice?
Like any lean methodology, successful implementation requires ongoing cultural and leadership support. As such, Standard Work faces challenges that Lean and Six Sigma practitioners are familiar with. Leaders don’t show support because they lack visibility into the benefits. Continuous improvement culture is difficult to take root and sustain.
However, unique to the practice, is an over-reliance on outdated techniques and ineffective tools. The traditional methods for Standard Work haven’t changed since 1951, when Taiichi Ohno (co-founder of the Toyota Production System) first developed the concept.
The Challenges of Standard Work
Despite the dismal lack of innovation, the importance of Standard Work has never been stronger. At its core, Standard Work is a method for documenting and improving standardized procedures. It’s the base on which all continuous improvement efforts are built — it’s fundamental to any Lean business.
Understanding the unique challenges of Standard Work will help your business reduce waste, improve quality, and support a culture of continuous improvement.
Lack of Leadership Support
88% of companies cited lack of commitment from leadership as a top reason for unsuccessful implementation of Standard Work and other lean techniques.
Lean initiatives take commitment from company leaders to be successful and set the precedent for a receptive employee culture. Without leadership support, employees perceive new initiatives as hypocritical and misaligned with company goals.
As leaders fail to practice what they preach, employees have a hard time justifying their own individual efforts.
"For a production person to be able to write a standard work sheet that other workers can understand, he or she must be convinced of its importance."
- Taiichi Ohno
Standard Work is human-driven, and can only benefit companies when a culture of continuous improvement is in place. This takes commitment from all levels. Employees rarely commit to change until managers lead by example. Not only will lack of leadership support damage company morale, but strategic, leadership-level decisions won’t be made with Standard Work in mind.
The Root Problem: Lack of Visibility
Leaders are unable to visualize the benefits of Standard Work because it lacks transparency. A surprising 40% of manufacturers have zero visibility into the real-time statuses of their processes. Operators are improving quality and process efficiency, but leaders don’t have the data to see how these improvements are impacting the bottom line.
Traditional tools are spreadsheet-based, uninformative, and static. Without insight into the ongoing improvements, leaders are in the dark and unable to see the morale-boosting benefits of Standard Work on the floor or in the field.
Feedback and Improvement Workflows
Lean systems are designed to eliminate waste, but they are also intended to develop a culture of action and autonomy in running and improving processes. When practiced well, Standard Work enables employees to provide feedback and improve the processes themselves.
"Employee knowledge is an asset that should be documented and leveraged."
In reality, employees do this already, often finding better ways of doing something, but failing to record the improvement is not easy. The waste generated here is significant, employee knowledge is an asset that should be documented and leveraged across the entire organization.
Standards should be a reflection of the current best known method for completing a process. When companies make it difficult for employees to provide feedback and apply improvements, standards won’t reflect the real work happening each day. As a result, the methodology has developed a reputation for being inflexible, causing people to forget that it’s really a tool for continuous improvement.
The Root Problem: Cumbersome Improvement Workflows
Successful companies have a history of understanding the importance of not only maintaining, but continuously improving standards.
Toyota starts addressing every quality defect on the line by asking, “Was the Standard Work followed?” If the answer is “yes,” then the problem is with the process and necessary improvements are made.
“If you think of “standardization” as the best you know today, but which is to be improved tomorrow—you get somewhere. But if you think of standards as confining, then progress stops.”
- Henry Ford
The Ford Motor Company, often associated with rigid standardization with their moving assembly line, was actually the first to successfully connect continuous improvement with standardization.
Outdated Tools & Techniques
Taiichi Ohno first developed standardized worksheets as a part of the foundation for the famous Toyota Production System (TPS) in 1951. The goal was to record processes as objectively and accurately as possible by tracking time required, work sequences, and inventory. This was achieved through spreadsheets and process flow charts; using symbols and lines to visually connect information.
While effective for their time, these methods haven’t changed much in the last 60 years. This lack of evolution has caused companies to dismiss Standard Work as too difficult to implement.
Where companies have now turned to digital systems to manage other aspects of their business—inventory, quality, product lifecycle management, etc.—Standard Work has been left out of digital transformation strategies.
The Root Problem: Being Disconnected From People
The tools developed in the 1950’s lack the advantages of modern technology, but their primary shortcomings are that they are too broad, lacking practicality for those that rely on them.
Information such as resource requirements, process flow analysis, and takt time, may be important details, but are not relevant to the workers on the floor. This information overload prevents the workforce from focusing on what’s relevant — which is also where they will provide the best insights for improvement.
At the end of the day, Standard Work is about people, and it isn’t working because the tools available are failing to connect with the workforce in a meaningful way.
Standard Work for the Modern Age
Dozuki is a platform that’s been developed specifically to help companies document, improve, and train workers to approved standards. Traditional tools are failing at a rate that’s unsustainable. Learn how to leverage technology to bring Standard Work into the 21st century with our free e-book, The Modern Guide to Standard Work.
Related Posts
View All PostsWhat Caused the False Missile Alert in Hawaii
Apparently, it was a simple mistake that caused the false missile alert to be sent to phones across the state of Hawaii. And while citizens were still recovering from the...
Continue ReadingWhat is Standard Work?
Lean operations and manufacturers have used Standard Work for decades, yet many companies lack clarity when it comes to this fundamental lean methodology. How is Standard...
Continue ReadingWhy Standard Work is a Contradiction
We recently wrote a popular article about a major mistake at a nuclear waste facility. In short, we cited poor standard revision processes as the root cause of the mistake,...
Continue Reading