
The Manufacturing Skills Gap is an Opportunity
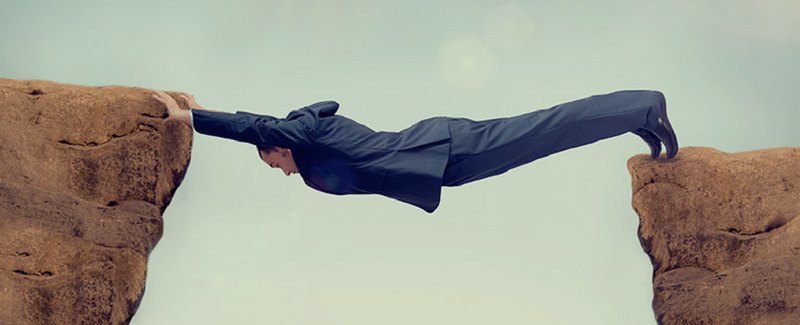
There is a pending manufacturing skills gap impacting the United States workforce. Millions of positions are expected to go unfilled in the coming years, with reports estimating over 2 million positions will need to be filled by 2025.
But discussions of the skills gap have become pervasively pessimistic.
Many reports are addressing this as an industry problem that needs “patching up.” It assumes that this distance between generations is a problem to be solved, rather than an opportunity to be leveraged. The coming changes will give those who anticipate and adapt a competitive edge.
The Concerning Stats
In the United States, 10,000 baby boomers are retiring every day—that’s 4 million a year. The manufacturing industry is particularly affected by this because hiring rates were slow when gen-x (the generation before millennials) was starting their careers. By 2020, 46% of the entire workforce will consist of millennials. As baby boomers in the manufacturing industry retire at an increasing rate, these younger generations will be needed to fill their vacancies.
When experienced baby boomers retire, they take their decades of knowledge with them.
No More Mentors
Retiring baby boomers will create lasting effects beyond just lost employees. When these seasoned employees leave they take their training and knowledge with them. The manufacturing industry has traditionally relied on mentoring and apprenticeship programs to train its workforce. With this drastic drain in experience, the old methods of mentorship and job shadowing won’t be sustainable.
The Encouraging Stats
When these statistics stand alone, it can be overwhelming to consider the efforts required to overcome this growing skills gap. This shift in workforce age and background will require organizations to adapt to new learning styles and implement new tools to improve the way they educate and train.
While this new generation may lack certain skills, millennials are 51% more likely to enter the workforce with a college degree than baby boomers. This foundational knowledge makes them the most trainable generation yet.
Millennials are 51% more likely to enter the workforce with
a college degree than baby boomers, making them the
most trainable generation yet.
The Digital Native Advantage
As the first generation to grow up with digital technologies, millennials have become “digital natives,” making them more comfortable with digital tools than previous generations. With industry 4.0 influencing manufacturing operations, this competence will allow millennials to thrive in the emerging high-tech manufacturing environments.
The Opportunity in the Gap
Reevaluating how employees are trained isn’t all bad. Organizational or “tribal” knowledge is something that has long been a problem for manufacturers. It’s caused Vienna Beef to lose their recipe and is one of the main reasons that vinyl record producers are struggling to meet demand. The International Organization of Standards (ISO) is also aware of this problem, making it one of the key updates in the new ISO 9001:2015 standard.
Any gap between demand and resources is an opportunity for innovation and improvement. The skills gap is an opportunity for companies to begin implementing Standard Work and start turning tribal knowledge into a company asset.
Yes, the changes can be overwhelming. But strategic business leaders will recognize this opportunity for what it is; a chance to upgrade, become more efficient, and stay ahead of the competition.
Training the Next Generation
Workplace training will be different for this new generation of manufacturers because a lack of available mentors necessitates the adoption of new technology and more efficient training. Understanding the learning styles, needs, and ambitions of millennials will be crucial to training and recruiting the next generation.
Related Posts
View All PostsGive Your Manufacturing Company a Boost
Whether you’re in aerospace or automotive, medical device or dairy—it’s important that your manufacturing company grows while keeping up with the latest innovations. In honor...
Continue ReadingTop 10 Taiichi Ohno Quotes
Wise quotes can inspire. Insightful sayings have the power to spark change and foster a culture of creativity and quality. Whether it’s on a sticky note clinging desperately...
Continue ReadingHow to Manage Mobile Devices on the Factory Floor
Tablets and smartphones can transform your industrial operations. This week we are joined by Jacob Rattray, Operational Technology Specialist from 3M. Jacob specializes in...
Continue Reading