
Understanding Corrective Action vs. Preventative Action in Manufacturing
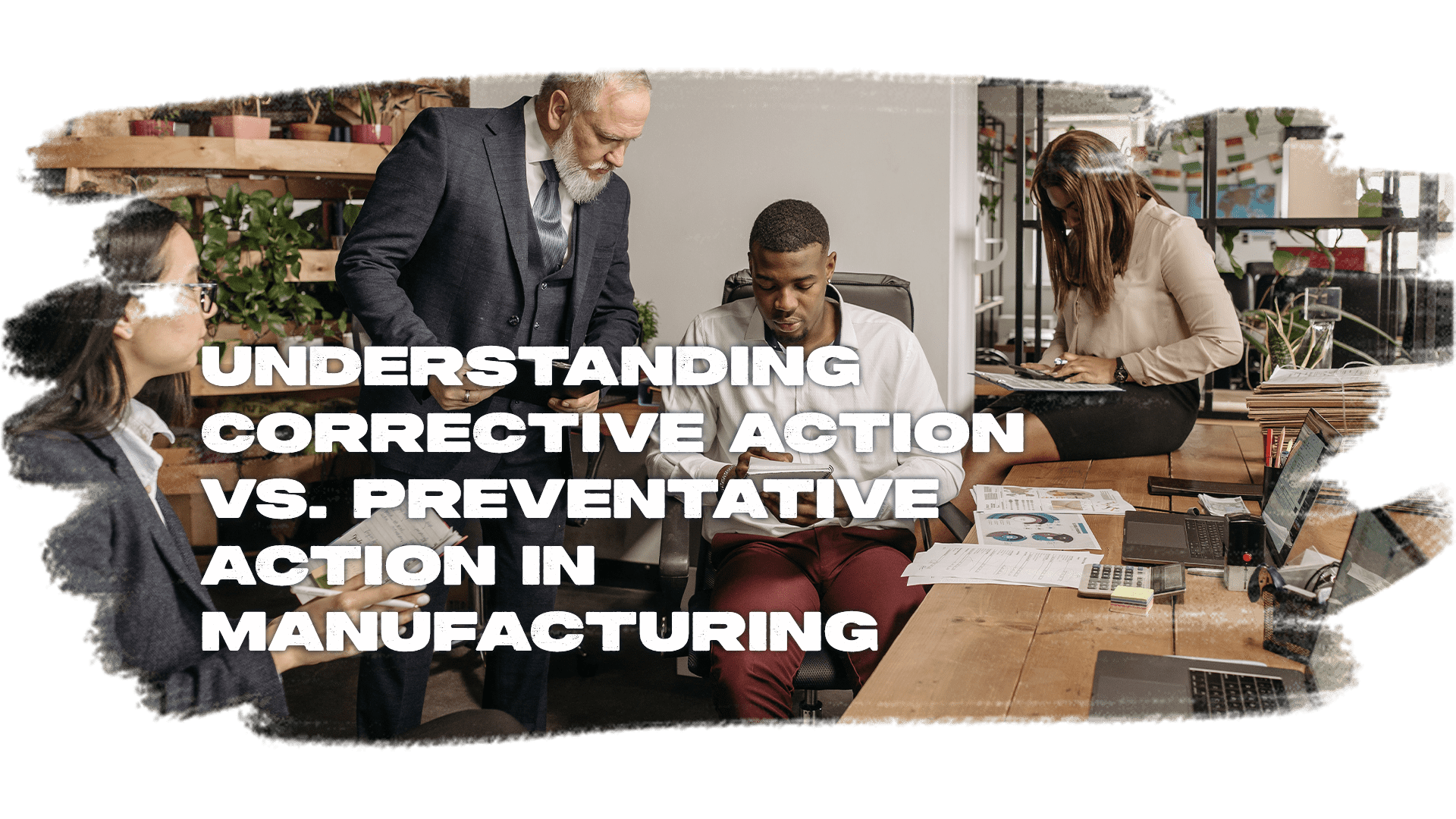
One of the most important aspects of a successful manufacturing organization is the ability to solve complex problems as they arise. In keeping with the continuous improvement methodology, manufacturing companies need to approach issues with the most effective problem-solving process.
Table of Contents
1. Critical Differences Between Corrective Action & Preventative Action
2. Corrective Action: Importance & Benefits
3. Preventative Action: Importance & Benefits
4. Best Practices for Implementing Corrective and Preventative Actions
5. Techniques for Preventative & Corrective Action
6. Challenges and Pitfalls in CAPA
7. How to Improve Preventative & Corrective Actions
A CAPA, or Corrective and Preventative Action Plan, is a document that outlines that process.
Both corrective and preventative action measures are critical for manufacturers. Corrective action involves identifying the root cause of a problem and then implementing a solution to prevent that problem from recurring.
Preventative action is a more proactive approach that works to identify and address potential issues before they can occur.
CAPA is an essential part of any quality management system. It helps organizations to improve their processes and in turn, their products. Efficient problem-solving systems contribute to a manufacturer’s ability to create a more excellent quality product, protect the public’s health and interests, and cut costs simultaneously.
Creating an effective CAPA plan and understanding the difference between these two methods is the topic of our article today.
In this article, we cover the basics of corrective vs. preventative action, offer examples of both in action, and detail how manufacturers can benefit from implementing these techniques in their operations.
Critical Differences Between Corrective Action & Preventative Action
ISO 9000:2015 outlines the differences between corrective vs. preventative action. Corrective action is taken to eliminate the cause of a nonconformity, while preventative action is taken to eliminate the cause of a potential future nonconformity.
Both help produce a higher quality product and are critical for manufacturing companies.
Let’s look a little closer at the differences between the two.
Corrective Actions
Corrective action is implemented in response to a problem that has already occurred. When a product comes off a production line defective, a root cause analysis is performed to determine the cause of the problem.
Then, appropriate corrective action is taken to eliminate the defect and prevent the problem from reoccurring.
When a vehicle breaks down, it typically ends up at the mechanic. The mechanic diagnoses the problem that led to the breakdown and takes corrective action to repair the problem.
For those who discover a health problem requiring medical intervention, these are corrective actions designed to correct a problem and prevent an issue from recurring.
Preventative Actions
Preventative action is a measure that is implemented before a problem even occurs. It is designed to prevent a problem from occurring in the first place. This process provides a way for manufacturers to avoid a defect entirely.
Vehicle maintenance is an excellent example of preventative action. Vehicle owners know from experience that failure to change the oil in a vehicle eventually leads to problems.
To prevent these problems from occurring, vehicle owners perform routine maintenance like oil changes and radiator flushes. These are preventive actions because they’re completed before a breakdown occurs and to prevent the outcome of vehicle failure.
Another example is people who eat a healthy diet, exercise, and visit a doctor regularly. These people are taking preventive measures to help protect themselves from potential health problems down the road.
Corrective Action: Importance & Benefits
The concept of corrective vs. preventative action is one that manufacturers should pay close attention to. Both methodologies bring specific benefits to an organization and must be implemented for the best outcome.
According to the Association of Clinical Research Professionals, the benefits of an effective CAPA system include reduced costs, the ability to meet regulatory requirements, more efficient processes and procedures, and a focus on continuous improvement.
Taking corrective action involves formulating a plan first. A corrective action plan is a document that outlines the steps an organization will take to address a specific problem or safety concern.
Benefits of Corrective Action
Improve Problem-Solving Processes and Results
A corrective action is one that first identifies and then solves a problem. And by its definition, it solves the problem in a way that prevents the same problem from reoccurring.
This process makes the problem-solving itself more effective. Instead of band-aiding a problem, corrective action solves the root cause of the problem.
Reduce Risks
Any problem with a production process opens a manufacturer to all kinds of risks such as the potential for a defective product to the risk of injury to workers and more. Solving that problem most effectively – so that it does not continue – reduces these risks for an organization.
Reduce Costs
Product defects cost organizations millions of dollars, both during production and afterward – especially if those defects can reach consumers. The cost of wasted time, effort, and materials is one thing. The cost of litigation is another beast entirely.
Protect a Company’s Reputation
A manufacturer hangs its reputation on the quality of their product. If lesser quality output is allowed to reach customers, it doesn’t take long for those customers to avoid doing business with that organization. In the cut-throat manufacturing landscape, companies must protect their reputation at all costs.
Preventative Action: Importance & Benefits
While corrective actions seek to identify and solve problems, preventative action takes a more proactive approach.
The difference between corrective vs. preventative actions is the difference between fixing an issue and stopping it from ever occurring in the first place.
Preventative action plans seek to eliminate safety hazards before they can cause accidents, defects, or downtime.
Benefits of Preventative Action
Reduced Accidents and Injuries
Companies can’t quantify the cost of a human life. However, the cost of accidents and injuries to a company's bottom line can be.
According to Liberty Mutual’s 2021 Workplace Safety Index, employers paid more than $1 billion weekly for workers’ compensation costs for disabling non-fatal workplace injuries in 2018.
An increased focus on preventative action plans can reduce the risk of workplace injury and accidents by improving safety throughout an organization.
Improved Morale
A safer work environment leads to more satisfied workers. When employees feel like their organization is making moves to improve safety, it boosts morale. Follow the path from improved confidence to greater engagement, increased productivity, and higher retention rates.
Reduced Cost
Besides the obvious costs of workplace accidents and injuries, organizations face other expenses related to production problems. Downtime is expensive, and product defects are costly.
Corrective actions can help to solve problems after they happen and prevent them from recurring. A preventive approach saves companies all the money lost when those problems manifest.
Best Practices for Implementing Corrective and Preventative Actions
Implementing an effective CAPA plan is the best way for a manufacturer to solve problems to uphold the tenets of continuous improvement.
But getting it right can be tricky, especially when deciding between corrective action vs. preventative action.
Instead of using a trial-and-error approach, follow these tips and best practices for implementing a CAPA plan.
Create Standard Procedures
Work starts with the creation of standard procedures. An effective CAPA plan should be outlined. These standards should be based on the organization's needs and ensure that specific regulatory rules and regulations are met.
Communicate With Employees
Once a set of standards has been established, the next step is to communicate those standards with employees.
That means ensuring they understand the CAPA process, including its use and how to implement it correctly. And it requires ensuring that employees are trained and monitored throughout the process.
Monitor Effectiveness
Effectively solving a problem requires implementing a solution and then monitoring the effectiveness of that solution. Measure, test, and document the results after implementing a new process or solution.
Based on those results, team members can rework the solution for a better result. The answer can be deemed effective and potentially reused in future problem-solving scenarios.
Techniques for Preventative & Corrective Action
Part of what makes the CAPA plan useful is determining when to use corrective vs. preventative actions.
This decision is where many organizations lose their footing because these two processes can overlap – and when dealing with complex processes, things can become murky. The process can start once a determination has been made between the two.
The next question the organization faces is how to start that process. And just like any job, the right tools are required to make the work as effective and successful as possible.
Here are some common tools used in corrective and preventive action plans.
Fishbone Diagrams
A fishbone diagram is a tool that can help identify the root cause of a specific problem and is especially useful when dealing with a large amount of information. Sorting that information into an understandable format helps to identify the cause and effect of problems.
Following the logical conclusion of this cause-and-effect format eventually uncovers the root cause of a problem.
Instead of being distracted by effects that are cumulative or secondary to the root cause, the fishbone diagram assigns a reason to those effects. It keeps team members focused on following the thread to its source.
The 5 Whys
The 5 Whys method is often used in conjunction with the Fishbone Diagram. When presented with a problem, team members ask “why” that problem manifested.
But instead of stopping there, the "why" questions continue until they reach the root cause or there is no answer to the question of why except the solution to the problem.
Let’s take a real-world example of the 5 Whys to better understand.
Problem: I was late for work this morning.
Why were you late for work this morning?
Answer: I slept through my alarm clock.
Why did you sleep through your alarm clock?
Answer: Because I was still tired.
Why were you still tired?
Answer: Because I didn’t get to sleep on time.
Why didn’t you get to sleep on time?
Answer: Because my friends were over until past midnight.
Why were your friends over until past midnight?
Answer: Because I didn’t ask them to leave at a reasonable hour.
Solution: Let your friends know they need to leave earlier, so you can get to bed earlier and wake up when the alarm clock goes off.
This process of asking “why” until you reach the root cause of a problem avoids the scenario of trying to solve the wrong problem.
For example, stopping at the first why might lead to the reasoning that the alarm clock itself was to blame for the lateness, but it doesn’t solve the root cause of not getting to sleep at a decent hour.
Fault Tree Analysis (FTA)
Another helpful tool for identifying the root cause of a problem is FTA or Fault Tree Analysis. This method is helpful in solving problems that include multiple moving parts.
But more than uncovering the root cause, FTA allows for risk analysis of potential failures and their outcomes, allowing organizations to implement preventive actions before a failure occurs.
A fault tree analysis starts with the potential failure, or problem, at the top of the diagram. Using a series of symbols, components, and outside factors are identified according to how they are linked to the original fault and each other.
While the 5 Whys works backward, starting with the outcome of the failure, the FTA works in the other direction by identifying a potential failure and mapping its eventual outcome.
Failure Mode and Effect Analysis (FMEA)
While FTA uses a top-down approach, with the failure at the top of the diagram, the Failure Mode and Effect Analysis, or FMEA, works oppositely.
FMEA is a highly flexible method of root cause and risk analysis because it allows for a greater focus on individual components within a system.
The FMEA starts with a component within the system and then maps out the potential failures of that component and their effect.
In a complex system, this typically leads to the failure of other components within the system or the map of a cascading cause-and-effect scenario.
The FMEA is also extremely useful when identifying the actual event of a failure is difficult. Working backward from each component within a system can pinpoint which was responsible for a particular loss by examining the outcomes in conjunction with each other.
The Hazard Analysis Critical Control Point (HACCP)
HACCP, or Hazard Analysis Critical Control Point, is a system used within the food industry to identify and control potential hazards.
By preventing problems at specific points within the process, referred to as “critical control points,” organizations can identify and eliminate potential risks associated with food production.
The HACCP uses hazard analysis to pinpoint specific risks within the system and then focuses on the critical control points or areas within the process where controls can be implemented to eliminate or control the hazard.
For example, mandating temperature-checking procedures throughout a process to reduce the risk of bacteria growth or contamination.
When a failure occurs at one of these CCPs, corrective action is taken to prevent any fallout. So, in essence, the HACCP uses preventive and corrective actions to control the outcome within a facility.
Challenges and Pitfalls in CAPA
Manufacturers should use methods to determine whether corrective vs. preventative action is the right path. But making that decision isn’t always enough. And the more complex a system, the harder it is to effectively implement CA and PA.
Look at some of the most common challenges and pitfalls that manufacturing organizations face when implementing CAPA plans.
Inadequate Root Cause Analysis
Performing an effective Root Cause Analysis is the key to making any CAPA plan successful. One cannot take effective action, or implement effective solutions, without understanding the problem's root cause.
Focusing attention on both halves of this equation, meaning the root cause and the solution, is critical to improving processes from both a corrective and preventative standpoint.
Ineffective CAPA Plans
The CAPA plan itself needs to be detailed, documented, and malleable. Yes, it’s essential to have a set of standard procedures that team members can follow. But an understanding that problem-solving should be flexible can help team members brainstorm solutions more effectively.
The CAPA plan should be a framework; companies should revisit and revise it often.
Inadequate Documentation
The entire CAPA process should be documented from start to finish. Implementing solutions through corrective or preventive actions is more effective when the results are tested and measured.
Proper documentation should occur at every step of the process to ensure regulatory compliance and as a learning tool to help team members improve the process in the future.
How to Improve Preventative & Corrective Actions
We have outlined the benefits of a CAPA plan and the differences between corrective action vs. preventative action. But just like any process within manufacturing, the focus must be on doing things better – striving for that ideal of continuous improvement.
CA and PA require a correct root cause analysis so that the following solution, or action, can be targeted to solve the right problem. But they also require effective solutions that will solve the problem for good.
Here are some tips for improving preventive and corrective actions and their outcomes.
- Monitor Progress – Ensure that team members monitor progress during and after CA or PA actions are implemented. Make sure that actions are completed on time and that the required standards are met throughout the process.
- Establish Clear Deadlines for Follow-up – Follow-up should be included as a step within the CAPA plan, including setting specific deadlines and requirements for that follow-up.
- Assign Responsibility – Assign specific team members to the follow-up process. Make sure they understand what is expected from them and when follow-up should be completed, including when and to whom they should report.
- Evaluate Both the Results and the Plan Itself – A thorough analysis of the CAPA process should follow its use. This includes determining if the action taken to correct or prevent a problem was effective, including if it prevented the recurrence of the problem. And it should include an analysis of the CAPA plan and process itself. Document what worked within the plan and what didn’t, and where team members struggled or faltered with the implementation of the system.
Final Thoughts
Manufacturing organizations are going to face failure. It’s a fact of life, inside and outside of a business environment.
Successful organizations are those who understand this fact and take action to do better next time – to learn from mistakes, so to speak.
Implementing a CAPA procedure and differentiating between when to use corrective vs. preventative action is one way that organizations can attack a problem.
CAPA allows manufacturers to improve their processes and outcomes by focusing on solutions that both correct failures after they occur and prevent potential problems before they arise.
An effective CAPA process includes several components: an effective root cause analysis, the implementation of practical action plans, and precise documentation and follow-up.
With these steps in place, organizations can improve their ability to identify and address problems and reach the goal of continuous improvement. The outcome of an effective CAPA plan is a higher-quality product, safer operations, lowering costs, and ultimately, an improved bottom line.
Related Posts
View All PostsConnected Workforce | What Is It & How Does It Benefit Companies?
One of the best ways businesses can get ahead and remain competitive is to embrace the available tools. And right now, that means implementing a connected workforce. Table...
Continue ReadingA Complete Guide to Visual Management in Manufacturing | 2023
Visual Management is a concept that can apply to everyday life - and life on the plant floor as well. As we go about our day, we encounter visual management cues in different...
Continue ReadingA Deeper Look Into Quality Assurance vs. Quality Control in Manufacturing
Manufacturing is taking raw materials and turning them into a product people need. Our industry makes the world go around. But competition, which is in part responsible for...
Continue Reading