
A Complete Guide to Visual Management in Manufacturing | 2023
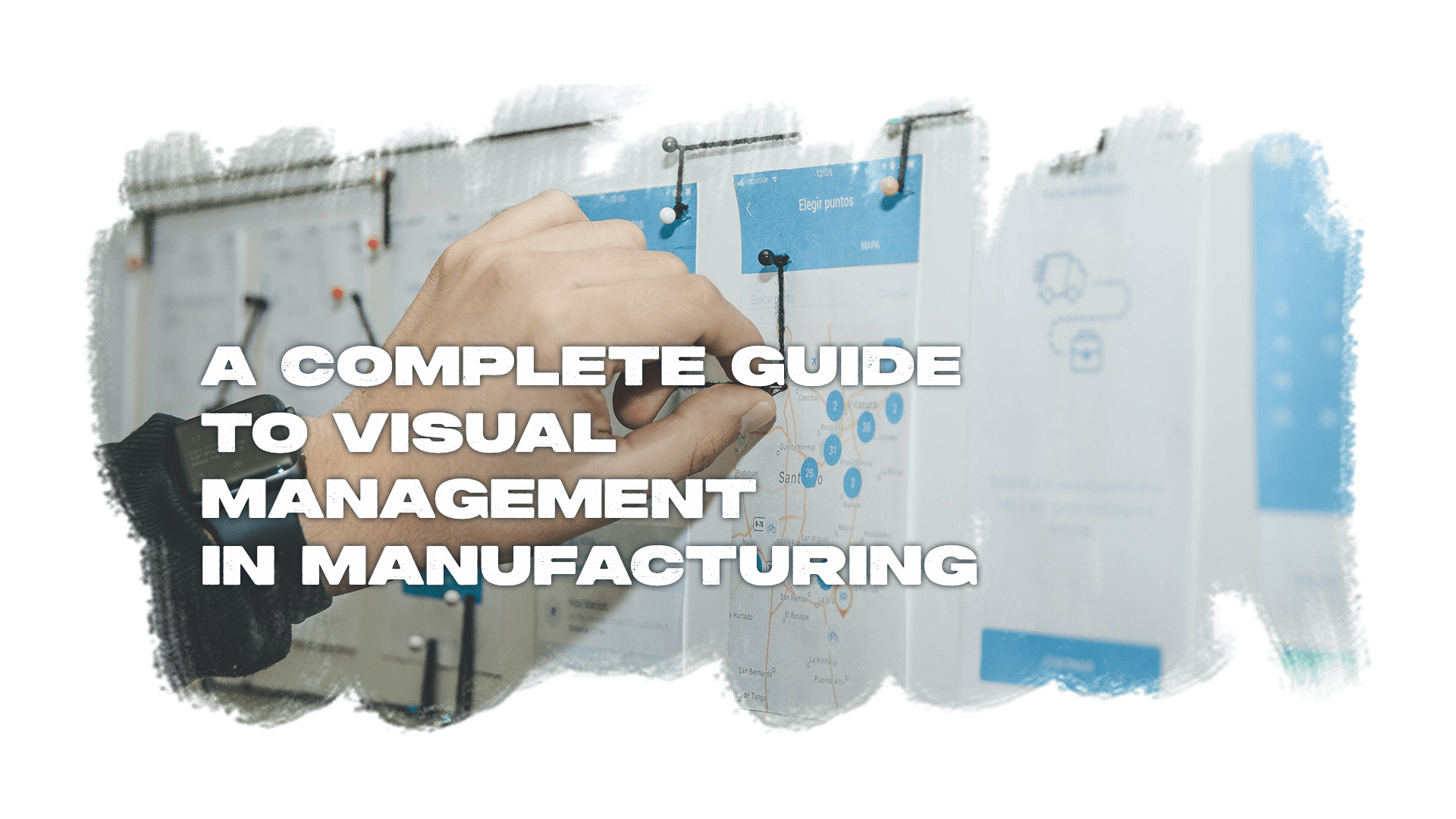
Visual Management is a concept that can apply to everyday life - and life on the plant floor as well. As we go about our day, we encounter visual management cues in different settings, many that we may not even recognize.
Table of Contents
1. What Is the Purpose of Visual Management?
2. Benefits of Implementing Visual Management Systems
3. Key Principles of Visual Management & Examples
4. Overcoming Challenges in Visual Management
5. Types of Visual Management Tools
6. Implementing Visual Management
7. Lean Manufacturing & Visual Management
The traffic lights warn us when it’s safe to proceed when to slow down, and when to stop. Signs, barriers, and lights at the train station tell us where it’s safe to stand and when the next train is expected to arrive.
Even the dashboard of our vehicle uses visual cues to alert us of our speed and our engine performance and to warn us when the fuel level is getting dangerously low.
Daily, we rely on visual cues to know what to do and where to go. And organizations worldwide use visual management to create order and safety in public settings. The same concept is used in manufacturing companies and on the factory floor to create a safer and more productive environment.
Visual management can be used to stop abnormalities once they occur by providing a warning and preventing the issue from continuing – saving companies from potentially losing profits. It can also be used to improve communication and champion a culture of continuous improvement.
This article will define the concept of visual management and explain how manufacturers can apply it in their workspaces. Plus, we will list some examples of visual management in action.
What Is the Purpose of Visual Management?
Communication is critical to any workforce, but that importance skyrockets in manufacturing. When humans work near potentially dangerous machinery and equipment, safety is paramount.
An effective communication system is one of the best ways to ensure everyone on the plant floor is as safe as possible.
Aside from these apparent benefits, communication via visual management is an influential tool organizations can use to improve workplace metrics. Faster and more efficient communication makes processes swifter and more accurate.
Think of the adage, "Work smarter, not harder." Using visual management can help to improve productivity by making people's jobs easier. But why are visual cues so effective? A lot of it has to do with the way our brains recognize and understand information.
According to studies, 75% of all information processed by the brain is derived from visual formats. And in learning settings, research has shown that visual information is mapped better in students’ minds.
Our brains are designed to glean information from the world around us, and because we are surrounded by visuals everywhere we go, that’s where we get most of our knowledge and information. Our brains take in, process, and retain visual information much faster than via any other pathway.
Visual management relies on that fact and employs it in a work environment to communicate information quickly and efficiently. And it does so in a way that everyone can easily understand.
Benefits of Implementing Visual Management Systems
The 3M Corporation recently commissioned a report stating that visual aids improve learning by up to 400%, that humans process visuals 60,000 times faster than text, and that the average person only retains about one-fifth of the information they hear.
With those statistics backing the use of visual management, it’s clear that the benefits for manufacturers would be many.
In a factory setting, communicating information quickly and effectively is vital. It can save the organization millions of dollars and could even save lives.
Let’s look at some specific benefits manufacturers can gain by implementing visual management system
Improved Communication
Many manufacturing companies are experiencing increased cultural and language diversity among their workforce, making communication more difficult.
Maybe that’s why OSHA found. more Hispanic workers are injured in the workplace than any other ethnic group. Visual management allows people of all languages and cultures to understand information easily.
Increased Safety
The factory floor can be a dangerous place on a good day. Visual management is one-way companies can identify and correct potential hazards, thus preventing accidents and injuries.
Reduced Errors
Visual cues can help to prevent mistakes by providing clear instructions and expectations to workers. Visual aids can also remind seasoned workers not to rush, cut corners, or take potentially dangerous risks.
Increased Productivity
Visual management can improve productivity by making it easier for employees to see what needs to be done when it needs to be done, and in what order to complete a task. It can also speed up production by demonstrating exactly how to do something.
Enhanced Customer Satisfaction
Visual management extends beyond the plant floor. Companies can rely on visual tools to provide customers with clear information about products and services. Customers will have a better understanding of what to expect. And they will be more satisfied when they receive exactly what they are promised.
Key Principles of Visual Management & Examples
Depending on the needs of an organization at any given moment, or the needs of a specific department, a visual management system can look very different.
Any system can be individualized for a particular need. This is one component that makes visual management so incredibly useful for manufacturers.
Below are some of the main components of a visual management system and some examples you can use for inspiration.
Standard Work
Standard work is a set of detailed instructions. But in a manufacturing setting, it's much more than that. The complexity of processes, equipment, and machinery makes it critical for every employee to follow the exact instructions to avoid mistakes and deviations.
Including visual tools in standard work instructions makes it easier for workers to visualize, understand, and retain the information.
Andon
The term Andon comes from Japanese and translates to “paper lantern.” Like many lean manufacturing principles, Andon lights were implemented by Toyota Production to communicate problems or abnormalities in a process.
Andon goes hand in hand with Jidoka; another concept originated by Toyota based on the idea that it’s more efficient to stop a process and address an issue as soon as possible.
Visual Controls
Visual controls are simply tools used to communicate information. They could be physical objects, signs, displays, or some other form of visual communication.
Visual controls can be used on the plant floor, for example, floor markings, color coding, arrows, or safety signs. Or they can be used in the board room to communicate goals and performance metrics.
The 5S Methodology
The 5S method is a Japanese lean manufacturing methodology focused on organizing and maintaining a clean, orderly, and efficient workplace. The 5S method includes the following steps: sort, set in order, shine, standardize, and sustain. Visual management can be used in conjunction with 5S steps.
This will encourage every worker to take ownership of their workspace and use the same standards as a guideline.
Overcoming Challenges in Visual Management
While the definition and uses for visual management are extremely wide-ranging, organizations often face similar challenges when putting together a system.
These challenges may look different in a particular setting because of the variations in an organization's specific needs and structure.
But understanding the common pitfalls may help organizations succeed more when implementing a visual management strategy.
Choosing a BI supplier and understanding the difference.
Business Intelligence, or BI, often needs to be clarified with visual management because both are used to convey information. But while BI solutions provide insights into historical data, visual management is intended to communicate real-time information.
Choosing a solution that is not connected to your information system.
The point of visual management is to make the transfer of information faster and more efficient. When systems don’t work together, that goal becomes harder to achieve.
Systems that are not flexible and interconnected lead to more work in the form of manual data entry and updating. The result is a time-consuming process prone to error and systems working against each other.
Favoring a free solution over effectiveness.
Yes, free is one of those phrases that companies love. But as they say, you get what you pay for. Free solutions may be readily available and easy to jump into. However, spending more of the budget on a visual management solution will likely mean a more comprehensive and user-friendly result with ongoing vendor support.
Not involving employees in the selection process.
Visual management solutions and tools are purpose-built for employees and an organization's specific needs. Since workers will primarily use these tools, relying on their expertise and opinions only makes sense.
Visual management solutions will be most effective when they’re designed with direct input from those who will be working with them – the employees.
Not implementing a change management plan.
Like any new initiative, implementing a visual management plan is a significant change for workers.
That means two things.
First, workers will require proper training to understand the tools and how to use them.
Secondly, employees need to feel a sense of purpose and inclusion in the process. Make workers a part of the solution and planning process so they embrace the changes instead of resenting them.
Types of Visual Management Tools
Visual management tools can vary, and only some solutions suit an organization. But specific tools are commonly used in a factory setting, and for a good reason.
The visual management tools in this next section all have uses that can benefit workers on a plant floor.
Dozuki
Dozuki is a cloud-based visual knowledge management platform that helps manufacturing organizations capture, share, and manage their knowledge.
This standard work instruction tool uses visual management to communicate standard instructions to workers quickly.
Dozuki allows real-time communication between workers, supervisors, and even separate departments. And using visual management as a training tool, Dozuki makes onboarding, training, and cross-training easier and faster.
Andon Systems
The Andon system is one of the most useful visual tools for factory workers. Andon uses a system of lights, colors, and information boards to indicate the status of a production line.
These lights can alert workers when errors occur, allowing them to identify and address problems quickly. The result is fewer defects, reduced waste, increased productivity, and a higher-quality result.
Shadow Boards
Shadow boards can help workers organize and track tools in the workplace. Using a visual image featuring the actual outlines of the tools where they are supposed to go, a shadow board makes it easier for workers to stay organized.
A shadow board also makes it immediately apparent when a tool is missing or out of place.
Colors Visuals
One of the most straightforward visual management tools, this is also one of the most effective. Using colors in the workplace can quickly and effectively communicate messages to workers, regardless of their training, position, native language, or culture.
Color visuals are also incredibly flexible and can be used for several purposes. These include helping workers quickly identify potential hazards, making it obvious when an area requires attention, or communicating instructions for safe work practices.
Implementing Visual Management
Knowing where to start might seem overwhelming, with so many variations in how visual management can support an organization. But just like anything else, step-by-step planning and implementation is the key to making it work.
Organizations should set clear goals for any new system, aim for specific expectations, and follow up on progress.
Each organization's plan will look different, but we’ve included a basic framework below.
Step #1 – Identify Goals
Step number one involves formulating a reason. What is the reason for deciding to implement each specific visual management tool? Because visual management tools are so flexible and varied, each goal should be clear and include measurable expected results.
Step #2 – Choose the Right Tools
Depending on the specific goal, the visual management tool should be suited to deliver the expected results. Choose the right tools for your organization's needs for the best results.
Step #3 – Design the Visuals
For a visual management tool to be effective, it needs to be clear, concise, and easy to understand. Any device that falls outside of this definition defeats the intended purpose. Use input from team members and workers in the design so it meets everyone’s needs.
Step #4 – Place the Visuals
A visual tool that isn’t very visible won’t make much difference. Make sure the visuals are positioned where they will be seen by those specific employees who need to see them. Check for obstructions in the line of sight as well.
Step #5 – Communicate with Employees
Any successful implementation requires a team effort. Make sure that everyone within an organization understands the importance of visual management and the intended purpose of a specific visual tool.
Most importantly, ensure they know how the tool will make their jobs easier and safer.
Step #6 – Monitor Progress and Update Visuals as Needed
Monitor the effectiveness of visuals frequently. Make any improvements or updates to ensure visuals are still accurate, relevant, and operating correctly.
Make your visual management strategy a component of a more extensive continuous improvement culture – meaning never stop seeking to improve.
Lean Manufacturing & Visual Management
Lean manufacturing is one component that falls under the umbrella of continuous improvement. Visual management is an effective tool for helping an organization build a lean culture.
Manufacturers can make huge strides toward reducing waste by implementing visual tools in the right places. Therein lies the secret to lean manufacturing.
Several types of waste can be created by a manufacturing process, including:
- Overproduction
- Waiting
- Transportation
- Processing
- Inventory
- Defects
Visual management tools can identify and correct these potential wastes in manufacturing. Doing so helps to reduce the number of defects that come off the line.
A defective batch can cost a company millions of dollars, wasted materials, and wasted labor. Ultimately, allowing faults to occur unchecked reduces quality and the likelihood of unhappy, unsatisfied customers.
Visual tools can also help identify processes where overproduction is occurring. A department-wide visual representation of production results can help manufacturers balance their needs with output.
Eliminating instances of overproduction can save both time and money, as well as help employees to be more efficient.
Eliminating overproduction results in a reduction in waiting and inventory waste as well. When a factory operates at peak efficiency, every department works together at the same pace and on the same page.
Nobody is waiting for someone else to finish up. Nobody is creating stockpiles of unnecessary inventory, just eating up resources and taking up space.
Final Thoughts
Visual management serves a vital role in manufacturing, more so than most organizations realize. The same is true of our everyday lives. Without visual cues telling us where to go, what to do, and when to do it – chaos would prevail in many situations.
The eyes are the windows to the soul and allow us to see and understand the world around us. That understanding is critical to the safety and success of a manufacturing company.
Organizations can make the most of this fact by knowing how prominent and crucial visual tools are on the plant floor.
Strategy always works better when it is a researched, targeted, and purposeful process. Gain an understanding of visual management and its many uses in manufacturing, Make the most of the tools available. What will result is a more efficient, productive, and successful team.
Related Posts
View All PostsUnderstanding Corrective Action vs. Preventative Action in Manufacturing
One of the most important aspects of a successful manufacturing organization is the ability to solve complex problems as they arise. In keeping with the continuous...
Continue ReadingBest Practices to Maximize Production Capacity in Manufacturing | 2023
According to the numbers, manufacturing makes up around 12% of the U.S. GDP and provides jobs for 12.984 million Americans, or about 9.6% of all U.S. workers. In other words,...
Continue ReadingIdentifying Defects: How Root Cause Analysis Will Save Manufacturing
Manufacturing companies work hard to build a lean culture. The never-ending march toward the ideal of perfection through the motto of continuous improvement requires constant...
Continue Reading