
Maximizing Efficiency: A Guide to Total Productive Maintenance
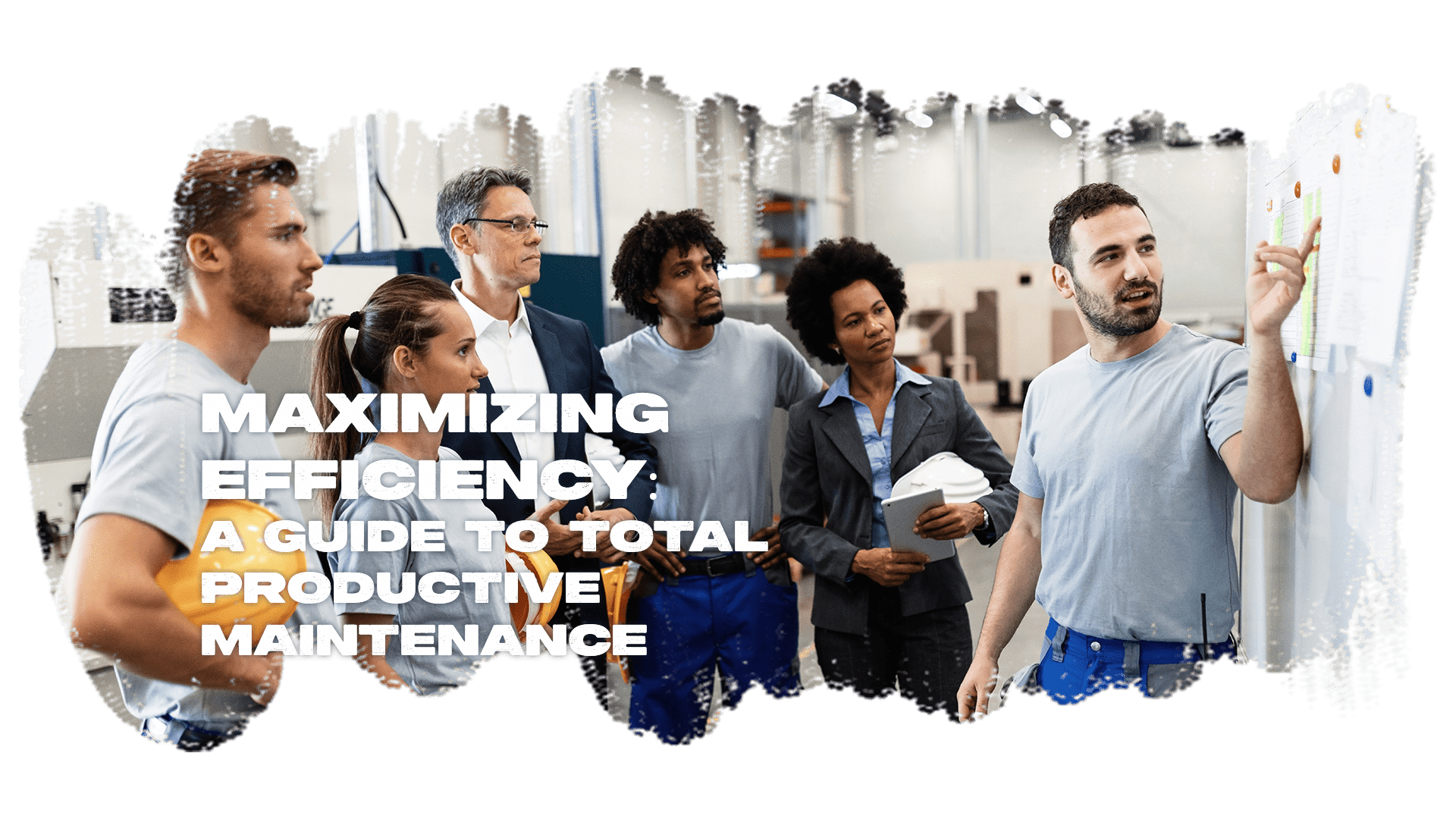
Maintenance is an essential requirement for any manufacturing company. Whenever machinery and equipment enter an equation, there will be a likelihood of that machinery breaking down. Maintenance is one way to reduce the likelihood of those breakdowns, and sometimes eliminate them. But who oversees that maintenance?
Table of Contents
4. Advantages of Autonomous Maintenance
5. Challenges of Autonomous Maintenance
7. Tips for Implementing Planned Maintenance
11. The Five Steps to Productive Maintenance Mastery
The concept behind total productive maintenance is that everyone is responsible, not just maintenance technicians. TPM can be traced back to Japan in 1951 when it was implemented at Nippondenso, a company operating as part of the Toyota brand.
The organization developed this concept to solve problems using automated machinery. Instead of tasking the maintenance group to fix problems after they occurred, the team tasked the operators themselves to do preventative and routine maintenance.
This freed up the actual maintenance department to focus on making improvements that would increase the reliability and performance of the machinery.
Nippondenso learned through this experience that when everyone within an organization is held responsible for maintaining machinery, the company has less downtime, fewer defects, and a higher level of productivity. The concept worked so well that it became standard at manufacturing plants worldwide.
With an increased focus on building a lean manufacturing culture and finding ways to cut costs by eliminating waste, total productive maintenance is a solution that companies must embrace.
TPM gives manufacturers a structured system that will lead to more efficient production processes, increases Overall Equipment Effectiveness (OEE), and reduces unplanned downtime – something that costs industrial manufacturers an estimated $50 billion annually and as much as $260,000 an hour.
This article will explain how manufacturers can implement TPM in their facilities. We will break down the basics of the TPM structure and explain how companies can benefit from the concept that maintenance is a key component of lean manufacturing.
The Eight Pillars of TPM
According to Safeopedia, Total Productive Maintenance is an approach to maintenance that aims to achieve a perfect production process.
All organizations strive for increased productivity, efficiency, and safety within their facilities. TPM reaches those goals by creating processes that aim for zero unplanned failures, product defects, and zero accidents.
Total productive maintenance is built around the 5-S system, which the Japanese created to organize processes for the best results. The 5-S system consists of five Japanese phrases, each used to define a specific part of the organizational structure.
Seiri (Organize) - Eliminating clutter.
Seiton (Orderliness) - Follow the “a place for everything and everything in its place” rule.
Seiso (Cleanliness) - Maintain a clean workspace at all times.
Sekietsu (Standardize) - Standardize work processes for consistency.
Shitsuke (Sustain) - Reinforce these steps constantly.
TPM uses eight pillars within its structure, each with a specific purpose and goal. Those eight pillars are:
Focused Improvement (Kaizen)
Continuous improvement and focused improvement go hand in hand. This is focused improvement when teams make a concerted and constant effort to improve across the board, including specific and targeted tasks.
Autonomous Maintenance
The definition of autonomous is the “freedom to act independently.” In terms of maintenance, it means giving employees the autonomy to take control of their workspace and their equipment.
Planned Maintenance
Downtime is a productivity killer for manufacturers. Planned and preventative maintenance help reduce downtime by scheduling maintenance at opportune times and reducing the number of unplanned breakdowns. Preventative maintenance is preferred by 80% of maintenance personnel as part of a multi-faceted strategy.
Quality Management
Quality is key for manufacturers and helps ensure customers are satisfied with products. TPM helps bolster that goal by eliminating defects through processes and systems that keep quality management at the core.
Early Equipment Management
Early Equipment Management happens when new processes, machinery, and products are designed. It involves taking advantage of previously learned information and lessons. Building processes with maintenance in mind helps eliminate downtime and defects proactively.
Training and Education
Putting factory workers in charge of their machinery and equipment maintenance won’t succeed without proper training and education. For example, poor compliance with lockout and tagout procedures is one of the top OSHA violations and can lead to serious injury.
Safety, Health, and Environment
Lean manufacturing aims to reduce waste and the environmental impact of manufacturing processes. And it significantly focuses on increasing employees' health, safety, and well-being. These things have multiple benefits for organizations, from reducing costs and fines to reducing turnover and worker harm.
TPM in Administration
Total Productive Maintenance extends beyond the plant floor. Even those at the administrative level can contribute to the maintenance, whether via scheduling or seeking to build better processes and systems.
Implementing TPM
Description: Provide a detailed guide on implementing a successful (TPM) program. Highlight TPM's foundation and pillars, including 5S, autonomous maintenance, planned maintenance, and focused improvement.
Provide a step-by-step guide for implementing TPM, including addressing significant losses, restoring equipment to prime operating condition, and implementing planned maintenance. Include a case study of how TPM has been successfully implemented in plants worldwide.
Studies have shown that adequately implementing a TPM program positively correlates to reduced lost production of 70% and a 50% reduction in breakdown labor rates.
The first step is to have an organized system to boost the efficiency and success of maintenance procedures. That’s what total productive maintenance provides.
The second step is implementing that system successfully and across all arms of the organization. We’ve broken it down into a step-by-step guide that will facilitate a smooth transition to the culture of TPM.
Step #1 – Pick a Pilot Program
When implementing a TPM program, starting small and targeted is best. That way, organizations can test methods, build a training system, and create processes specific to each piece of machinery.
Focusing on one area at a time also reduces the risk of putting a critical piece of equipment out of commission. Conversely, companies can focus on one crucial piece of equipment if the benefit of improving maintenance on that unit outweighs the risks.
Step #2 – Start by Restoring the Equipment
Using the 5-S method, focus on the first goal of returning or restoring the equipment to its prime working condition. This means fixing any problems that currently exist. Set a standard for operation, results, and productivity that will be the goal going forward.
Step #3 – Measure OEE
OEE, or Overall Equipment Effectiveness, measures the operability and efficiency of a singular piece of machinery. Tracking unplanned breakdowns, and their underlying causes, is the first step in correcting those issues for better performance next time.
Step #5 – Address Major Losses
When experiencing a significant downtime event, it’s vital to construct a plan to address the contributing factors. This step requires a close look at the cause of these significant events and creating and implementing a plan designed to solve the problem so it doesn’t reoccur.
Step #6 – Proactive Maintenance
Once the equipment is restored to peak operating condition and major loss events have been addressed, the next step is to regularly conduct preventative or proactive maintenance.
This requires building a process that addresses common failures and keeping detailed maintenance records to help streamline and optimize this process.
Step #7 – Take advantage of Every Pillar of TPM
A basic structure for implementing TPM practices in a facility includes the steps listed below. But TPM stretches across an organization. Use the eight pillars to ensure that every step of the TPM process is utilized and implemented consistently for the best results.
Autonomous Maintenance
At the heart of total productive maintenance are the employees themselves. Rather than leaning on a team of maintenance technicians to swoop in and address problems, autonomous maintenance puts the power in the hands of the operators.
Doing so streamlines production, saves valuable time, and allows operators to take ownership, pride, and care of their equipment. The goal is to add to the culture of lean manufacturing and use autonomous maintenance to increase a facility's overall quality and output.
The goals of autonomous maintenance are:
- Training machine operators to perform basic maintenance tasks on their specific machines, such as cleaning, inspecting, and lubricating.
- Using preventative maintenance to prevent equipment deterioration and breakdowns.
- Bringing equipment to a “peak” or “like-new” condition
- Keep equipment at this level through restoration, maintenance, and operations.
- Create a culture of autonomy and responsibility throughout every level of an organization.
Advantages of Autonomous Maintenance
Increases operator knowledge and efficiency – Training and education always lead to better performance.
Autonomous maintenance requires operators to learn every detail of their machinery, including what is required to keep it in peak operating condition and what scenarios lead to unplanned breakdowns. This knowledge will help them spot potential problems before they arise.
● Increases Efficiency of the Maintenance Team
Tasking operators to maintain their machinery saves the maintenance team from spending all their time completing the same tasks. This allows them to focus on bigger projects, upgrades, and rebuilding processes that will increase productivity, quality, and efficiency overall.
● Lower Labor Costs and Reduced Downtime
Maintenance teams spend much time traveling between machinery. It might not seem like much, but all that travel time adds up.
They also wait for a machine to become available if maintenance is required, and operators spend time waiting for the maintenance team. Much of this waste is eliminated when operators take over daily maintenance tasks.
● Increases Team Cohesiveness
Autonomous maintenance blurs the lines between maintenance techs and operators. Even though each operator becomes responsible for their machinery, the idea of autonomous maintenance builds a culture where everyone works for the greater good and efficiency of the organization – as a team.
Challenges of Autonomous Maintenance
Autonomy can be extremely useful in this application but must also be implemented carefully. Tasking individual operators with their machinery's care and basic maintenance helps improve efficiency and productivity.
But without communication and a sense of team cohesiveness, the plan can backfire.
Organizations can combat this by treating the implementation of TPD as a company-wide initiative. That means communicating goals, plans, and reasons to the entire team initially and throughout the process.
Secondly, keeping communication open between all departments and facilitating conversations between operators and maintenance techs builds cohesiveness and cooperation.
Planned Maintenance
Planned maintenance encompasses any maintenance activity that is planned, documented, or scheduled in advance. Planned maintenance can be scheduled and preventative, to fix potential problems before they manifest.
It can also refer to planned but unscheduled maintenance. An example of this type of maintenance would be having a plan to repair a breakdown as quickly and efficiently as possible.
Planned maintenance is typically one of the first ways organizations seek to perform maintenance – or should be. In the context of total productive maintenance, the goal for planned maintenance is twofold.
First, prevent downtime from occurring through preventative maintenance. And two, reduce downtime after it occurs by having a contingency plan to solve problems quickly.
Planned maintenance, whether proactively or in response to a breakdown, increases efficiency because it allows technicians to plan their steps ahead of time. That means all the necessary parts for a repair are present.
Technicians have reviewed the best practices and procedures for a particular situation. And it means a safe and secure equipment shutdown before repair work starts.
Tips for Implementing Planned Maintenance
● Take Stock Beforehand
Part of successfully implementing planned maintenance is planning. Take note of all the assets on both sides of the coin; machinery that requires preventative maintenance; machinery that is likely to require unscheduled maintenance. Categorizing each asset correctly will help when it comes time to build processes and procedures for carrying out maintenance.
● Utilize Checklists
Once a planned maintenance strategy is in use, tracking its effectiveness and efficiency is important. You can create checklists to measure specific KPIs around each planned maintenance activity.
Look for places where the procedures could benefit from changes and fine-tuning. And pay attention to feedback from the technicians and operators.
● Take Advantage of Planned Maintenance Software
A CMMS, or computerized maintenance management system, uses technology to organize and schedule planned maintenance activities. This system will help maintenance techs by pulling together all the resources and information they need in one place.
A CMMS system can also track parts and materials replenishment so that the pieces needed to perform maintenance are in stock at the right time. And it can schedule automated triggers alerting techs when repairs are needed.
Quality Maintenance
The next pillar of total productivity maintenance we will cover involves quality. Although quality maintenance is the sixth pillar of TPM, its importance is high because its effects trickle down to the customers.
It falls lower on the list of pillars because those above it must be in place and perfect for quality maintenance to be possible.
Quality maintenance has the goal of creating conditions where zero defects are possible. This is accomplished through careful oversight of the systems, people, materials, processes, and machines that all come together for production.
Each one of these components can introduce variables that might lead to defects. Quality maintenance seeks to remove those variables. The result is fewer defects and a higher quality product.
The key to quality maintenance is prevention. For manufacturers, preventing a defect from occurring in the first place is more efficient than spending time and resources building rigorous testing and inspection systems designed to detect a defect.
Once a defect can manifest, the time, labor, and materials have already been spent and wasted. It's important to catch these defects so the problem can be remedied and the defective product does not reach customers. But from a TPM perspective, preventing the defect altogether is much more advantageous.
Quality From Start to Finish
Quality should be included in every activity that occurs within a facility. It is one of the most important success drivers for manufacturers. Quality maintenance happens when activities surrounding any type of maintenance are optimized so that defects are eliminated, waste is reduced, downtime is cut, and equipment reliability is enhanced.
All these things add to the overall quality of the results. Here are some tools organizations can use to improve quality maintenance processes.
Continuous Improvement
Quality is viewed as a part of the bigger goal of continuous improvement. Tasks surrounding quality maintenance are performed with that goal, meaning they never stop and become a part of the culture.
Root Cause Analysis
Preventing defects before they occur is the key to quality maintenance. However, if a defect or issue occurs, root cause analysis is a tool that teams can use to discover the underlying, direct cause of the defect and create a plan to ensure the problem doesn’t reoccur.
Standardized Work
Having documented standards in place will help teams understand what is expected of them and how to accomplish those things. Rather than allowing a trial-and-error environment, standardized work puts the best policies, practices, and procedures in place from the start.
Early Equipment Management
The next pillar of total productive maintenance is early equipment management. The key word here is "early." This pillar involves steps that organizations can take before production even begins that will serve the overall purpose of continuous improvement, reducing downtime, increasing productivity and efficiency, and building a better-quality product.
Early equipment maintenance involves things like
- Designing with maintenance in mind
- Considering the cost of maintenance in the design
- Implementing machinery that requires infrequent maintenance.
- Building processes that result in infrequent breakdowns.
- Building designs and processes with safety in mind
Design for Maintenance
The design of the machine itself will determine how much maintenance is required to keep it in peak condition, and what type of maintenance must be employed. Keeping these things in mind from the start will ensure designers account for them during the initial phases of a project.
Design for Reliability
The components of a piece of equipment or machinery will determine how frequently maintenance must be performed. Early equipment maintenance means opting for components that reduce the need for maintenance instead of adding to it.
Design for Infrequent Breakdowns
Teams will make many decisions during the designing and planning process, including choosing between high-quality parts and components and less expensive options. If a less expensive component ultimately leads to more frequent breakdowns, then it does not meet the goals of early equipment maintenance. The cost will outweigh the benefits.
Training & Education
Implementing any new system requires thorough training and education if it’s expected to be successful. People are at the heart of every manufacturing facility activity, including total productive maintenance.
As organizations seek to build and implement TPM systems within a facility, they must also build training and development programs that coincide with those activities. And it’s not just a one-and-done process but an ongoing and permanent addition to the company's culture.
Training for TPM is crucial because a big part of what makes it successful is the operators themselves. You can’t task employees with a new job and expect them to perform well without the right knowledge and training first.
Training employees properly also motivates them to perform better. It helps organizations fill spots when they become available by giving employees the right platforms to upgrade their knowledge and abilities. And cross-training provides a source of talent and skill that organizations can use to fill gaps.
The Five Steps to Productive Maintenance Mastery
Learning any new skill is a process, and it works best when that process is laid out to provide the best advantage for the learner. Following The Five Steps to Mastery is the best way to build a training and development program for any task, including TPM.
1. Assess Understanding and Ability
Start by assessing the current ability and knowledge of the learner. This helps to set a baseline for what is already in place and identify gaps in their knowledge that must be addressed within the program.
2. Assess Skills
Maintenance tasks will require specific skills. Assessing the skill level of the learner beforehand is essential. It should be targeted to the job they’re expected to perform, how to recognize potential problems, and how to address those problems.
3. Set Development Targets
The goal of training and education is to improve the learner's knowledge, skills, and performance. Setting targets for development and training will help facilitate learning and motivate the learner to hit those goals.
4. Monitor Progress
Monitor the learner's progress throughout a training program and note areas where they are missing targets. Identify the cause of those missed targets, whether the responsibility lies with the learner or because of a weakness in the program.
5. Periodically Assessing Improvement
No training program is ever complete. It’s an ongoing process that involves monitoring and assessment. This will identify areas where training is incomplete or retraining is necessary.
Final Thoughts
Total productive maintenance is one of the best ways for manufacturing companies to maximize their efficiency – a significant component of success for organizations.
Reducing waste, eliminating defects, and improving quality are its goals. Empowering teams and operators to take ownership and control of maintenance processes and giving them tools to be successful is how organizations accomplish it.
The eight pillars of TPM are designed to help organizations meet these goals. They contribute to creating a lean manufacturing environment by taking a systematic and holistic approach to maintenance. But there must be a concentrated effort from the whole team to get it right.
It starts with a step-by-step implementation process that includes communication and teamwork. It involves a strong focus on continuous improvement as the end goal. And it must include a never-ending focus on training and education.
TPM has been around for nearly two-thirds of a century, and its success is one reason it has been embraced worldwide. With a successful TPM program in place and everyone in the organization working toward the same goals, the benefits will be apparent, measurable, and worth the effort.
Related Posts
View All PostsA Comprehensive Guide to Predictive Maintenance in Manufacturing | 2023
Effective maintenance requires a well-rounded approach. Manufacturing companies use planned, reactive, and proactive systems to prevent breakdowns and address problems as...
Continue ReadingUnderstanding Corrective Action vs. Preventative Action in Manufacturing
One of the most important aspects of a successful manufacturing organization is the ability to solve complex problems as they arise. In keeping with the continuous...
Continue ReadingImpact of AI in Manufacturing: Benefits, Challenges & Use Cases
Artificial Intelligence has become a hot topic in society today. What once was a term relegated to science fiction novels is now commonplace among people from all walks of...
Continue Reading