
7 Best Practices in Manufacturing Training for Employees
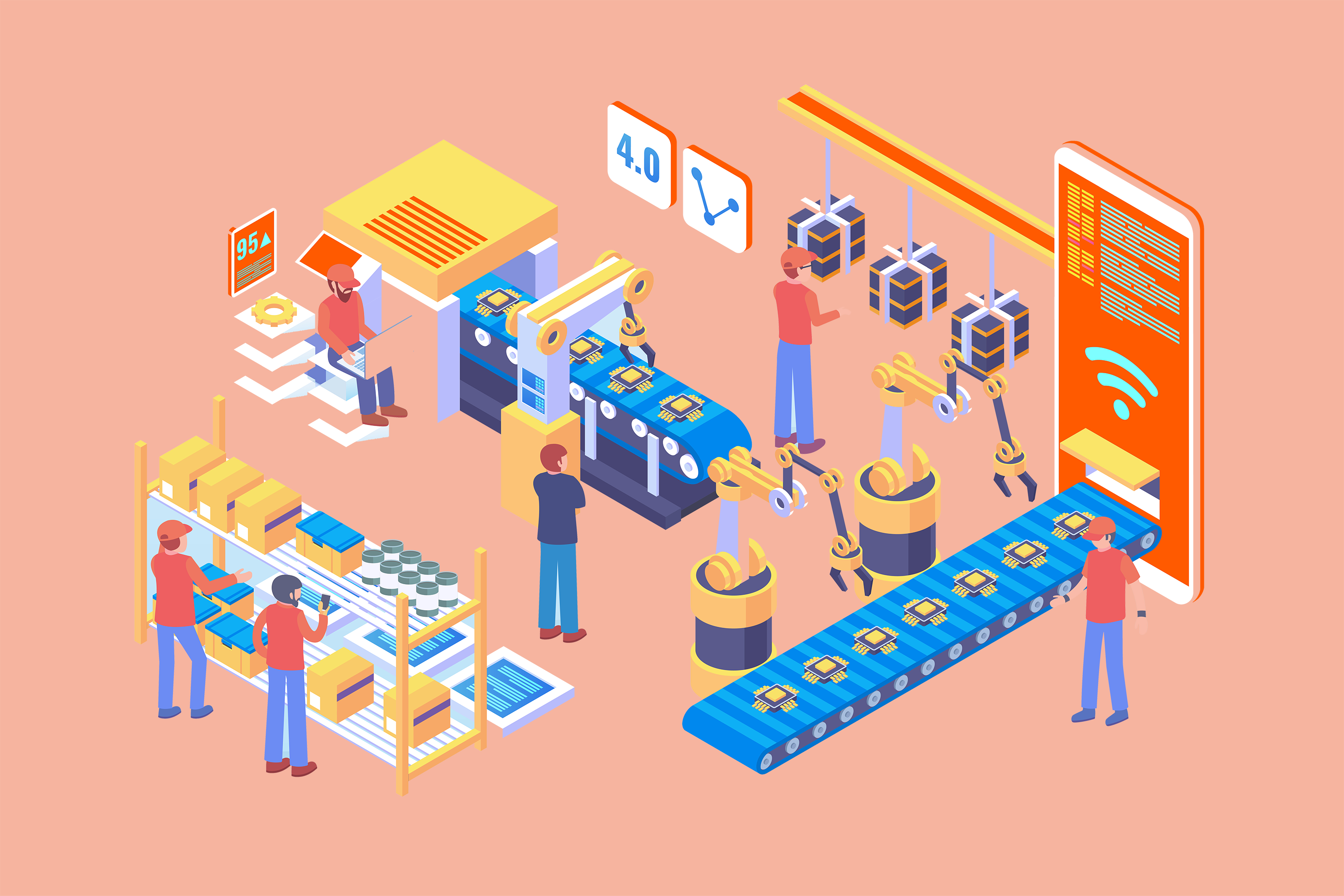
Training employees is a surefire way to improve productivity and efficiency within manufacturing. As the company grows and expands, its employees must also grow with it, which means they must be properly trained in every task.
To ensure success and improvement in a manufacturing company, the company must aim to increase productivity, improve quality, improve efficiency, and most importantly, establish an effective team.
Training employees provides an opportunity for employees to grow and expand their knowledge... which in turn will help the company grow and maintain smooth processes.
The benefits of training the employees at a manufacturing facility include a whole lot more, such as:
- Prepare employees for higher responsibilities
- Show employees that they are valued
- Patch weaknesses and gaps in their skill
- Increase productivity
- Improve problem-solving and critical thinking skills
- Improve safety standards
At the end of the day, your employees are human; they will have weaknesses and struggles. It is in the best interest of a company to make sure that these are conquered in order to keep the organization competitive.
In today’s ever-changing marketplace, the importance of making sure that your employees are efficient and up to the task has never been greater.
Studies have shown that trained employees help the business not only grow, but actually succeed in increasing revenue.
One study shows that compared to companies that don’t properly train their employees, those that invest in employee training have 24% higher profits and experience a 20% increase in sales.
Another study, by Fred Reichheld, also shows how well-trained employees provide better service, which can increase customer retention by 5%.
Facing a significant shortage in skilled labor, the manufacturing industry is now having difficulty filling open positions.
2.4 million jobs are projected to remain unfilled through 2028, despite rapid growth in the manufacturing industry. By employing the best practices in manufacturing training, employers can now fill these vacant positions and continue to add valuable employees to their current workforce.
In this post, you will learn the best practices in training employees at a manufacturing company.
These practices will allow you to equip your employees with the skills they need to operate and handle intricate machinery, the knowledge to complete complex processes, and the framework to troubleshoot work effectively.
Prepare Manufacturing Employees Before Training
One of the most important steps before you begin training new or existing employees, is making sure that the company prepares the employees and gets them ready to be trained.
Employees who are prepared for training are more likely to have a complete understanding and digest all the information they learn throughout the training.
This will allow them to effectively transfer the skills they learn during training. Here are some things you can do to prepare employees for the training process.
-
Prepare training materials and equipment:
Having training materials and equipment ready is essential to make sure that the training goes smoothly.
-
Let them know what to expect:
Provide the employees with information about what the training process will involve and cover.
-
Make your expectations clear:
Ensure that employees understand what tasks the company expects them to perform.
-
Train the managers and supervisors:
This can be done together with the employees or separately. The managers and supervisors must know what to expect from the employees after training. Additionally, they need to understand what the employees were taught, in order to enforce it in the workplace.
Knowing how to prepare employees can help you save a ton of resources during training.
Demonstrate How To Perform Each Task
Employees may often feel overwhelmed when you give them too much verbal or textual information during the training process. Sometimes, the workload might be daunting when they are untrained or undertrained.
That’s why it is important to make sure that employees receive not only auditory or textual instructions, but also visual and physical demonstrations.
A software like Dozuki can help manufacturing companies capture the expertise of seasoned team members or supervisors (usually the person who trains new employees) in a visual format.
Dozuki allows supervisors and trainers to bring tablets on the factory floor or place stations across the facility where employees can easily access visual instructions on how to complete a given task.
It’s like having a supervisor follow you around to make sure you’re doing the job correctly…
… minus the feeling of being micromanaged.
For the training to be effective, it is important to remember that different employees have different learning styles.
While a company might think that the most efficient way to train employees is through verbal and textual training, this couldn’t be farther from the truth.
An effective trainer would apply different styles of communication to cater to employees. This is especially important when training a factory workforce, as their job often requires them to operate physically.
There are a few things to keep in mind when training to a specific process to ensure the effectiveness of the demonstration. See to it that you:
-
Do not rush the demonstration.
-
Ask for feedback from the observers or employees.
-
Organize a supervised demonstration with the employees as the demonstrators.
By demonstrating the proper way to complete their tasks, you can ensure that the employees understand how to complete their jobs in the most effective and safe manner.
Make it Interactive (Hands-on Training)
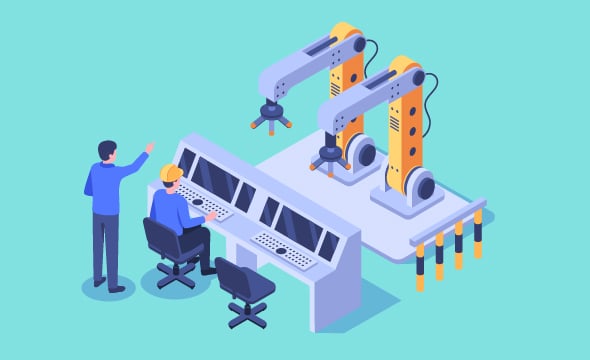
Making the training more interactive and hands-on is one of the best approaches to manufacturing training for employees. Hands-on or interactive training is a powerful method of teaching used by companies to improve employee training programs.
Instead of subjecting your employees to a boring text and audio-based presentation that they will probably forget, an interactive learning process is a surefire way of grabbing an employee’s attention, and it leaves a lasting impression.
Besides the benefit of increasing the retention of knowledge from the training, it also allows the employees to practice the skills they have learned through the training, in a safe and controlled environment.
More recently, advanced technology has allowed manufacturers to switch to a semi-automated means of production. These machines still require human involvement in the production process. This means that workers must be skilled enough to handle and operate these machines.
The knowledge and skills that these employees possess should not come from a simple PowerPoint presentation. Instead, it should come from hands-on and interactive training given by their manufacturing company.
More importantly, a hands-on and interactive approach allows the employees to finish the training with confidence. When a problem arises, those with experience will always be better at solving the problem compared to the employees who don’t.
Communicate Instructions Clearly
Proper communication is a crucial part of training employees. It allows for the effective transfer of ideas from leaders to employees.
Needless to say, it is an essential part of making sure that all the objectives of the training are met. Establishing a clear line of communication is an important step in fostering a good working relationship, which improves both morale and efficiency.
Just knowing the importance of communicating instructions is not enough.
Employers and managers sometimes give what they think are clear instructions to an employee, only to find out that the employee has completely misinterpreted it. No need to worry! This is a very common problem…
…and one that you can avoid by applying the following steps.
By doing the 7 things listed below, you can minimize errors and mistakes during the training process.
-
Don’t assume your employees know what you mean.
-
Practice being clear and specific with your instructions.
-
Emphasize important points.
-
Let the employees know what to avoid doing that might harm their progress.
-
Be specific with time frames.
-
Demonstrate or show examples.
-
Ask for feedback.
Staying Consistent with Training Factory Employees
Another essential part of training employees at a manufacturing company is consistency.
The manufacturing industry ranks number 1 in the list of industries that benefit most from consistent training. Being consistent goes a long way in guaranteeing that the training process will produce skilled employees. Especially in manufacturing, consistent training plays a critical role in preventing safety incidents.
It truly helps move forward with the training process at a steady pace while ensuring that the employees still receive and take in all the knowledge they need to learn.
Inconsistent training may also lead to dangers and errors involving your employees. Here are some of the dangers involved in providing your employees with inconsistent training:
-
Loss of productivity.
-
Employees are unaware of the company culture.
-
Knowledge deficit.
-
Endangering the safety of employees at the factory.
-
Company policies remain unclear for employees.
There are other additional benefits of consistent training in the manufacturing industry, which include:
-
Increases productivity.
-
Improves employee confidence.
-
Improves employee performance.
-
Clarifies company policies and culture to the employees.
The key is to focus on the return on investment. When done effectively, consistent training provides the high levels of return on investment you need to stay ahead of the competition.
Providing Frequent Feedback to Employees
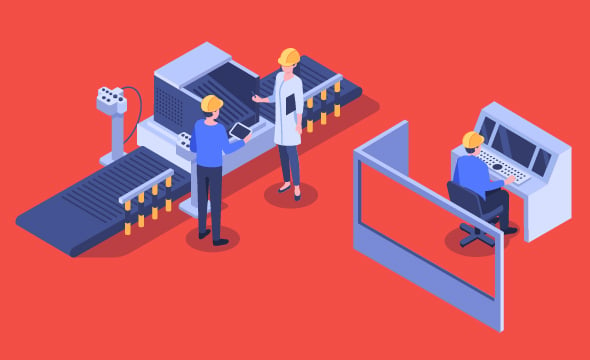
We often overlook the importance of giving feedback to our employees, despite its numerous benefits.
As long as feedback is given clearly and constructively, it can go a long way in ensuring the success of the training. Constructive criticism and proper feedback can improve an employee’s performance throughout the training, promote individual growth for the employee, promote employee loyalty, and decrease long-term training costs.
Feedback creates an opportunity for the employees to identify and acknowledge their gaps and errors, and it gives them a chance to improve.
Knowing the importance of giving feedback, how can one provide feedback effectively and constructively?
Since employers, factory managers, and supervisors are responsible for their employees’ performance and actions, it is important for them to know how to give both positive and negative feedback.
Here are some tips to provide proper feedback to help your staff:
-
If you need to give negative feedback to the employee, make sure to give positive feedback first.
-
Be specific with your feedback and don’t beat around the bush.
-
Be objective in your feedback by justifying them with factual information. Don’t base your feedback on personal emotions.
-
Do not criticize without giving actionable advice.
-
Communicate face-to-face as much as possible.
-
Ask for feedback, as well. This can help you identify your flaws as a trainer and educator.
Emphasize Safety & Security
Of the 7 best practices in training employees at manufacturing companies, the one you should NEVER forget is to practice safety and security at the factory.
In manufacturing companies, employees might work in dangerous environments with dangerous equipment or hazardous material. It becomes extra important to emphasize safety and security in the workplace.
The employees are the company’s responsibility. You must make it a priority to train your employees to prioritize and exercise their safety and security.
In manufacturing, there are many safety measures to take to ensure the safety of your workforce:
-
Have regular safety meetings.
-
Frequently conduct safety audits and inspections.
-
Punctually complete OSHA logs.
The first step in training employees in safety and security is making sure that they understand that they have a voice. Employees should know that they are allowed to inform managers and supervisors about unsafe working conditions.
Circling back to the previous practices discussed in this article, the employee must know how to use equipment, machines, and tools properly in order to avoid accidents. Let’s not forget the work attire in a factory environment! The training must encourage employees to wear the proper clothing or safety equipment.
Wrapping Up Manufacturing Training
Training is an essential part of ensuring that your employees succeed in the manufacturing workplace.
Proper training provides employees the opportunity to expand their knowledge about manufacturing, which helps them be more confident in their skills.
With these seven best practices as your guide, you can rest assured that you are training your employees to have the skills and knowledge to operate in the manufacturing industry successfully and efficiently.
FAQs From This Article
What is Manufacturing Training?
Manufacturing training encompasses various programs and practices aimed at equipping employees with the skills and knowledge they need to perform efficiently and safely in a manufacturing setting.
Why is Training Important in Manufacturing?
Effective training ensures that employees are competent, reduces accidents, increases productivity, and maintains the quality of products, which are all crucial for the success of a manufacturing company.
How Often Should Manufacturing Training Occur?
The frequency of training can depend on factors such as the introduction of new equipment, changes in procedures, or regulatory requirements. Continuous improvement models suggest regular, ongoing training to keep skills up-to-date.
What are Some Effective Manufacturing Training Methods?
Effective methods include hands-on practical training, digital work instructions, simulation-based training, and continuous on-the-job training to reinforce skills and knowledge.
Related Posts
View All PostsBest Practices On How To Retain Factory Workers
Manufacturing companies rely on workers to be the frontline of production. And while companies across all sectors struggle to recover from a labor crisis perpetuated in part...
Continue ReadingHow To Increase Productivity in Manufacturing
There are several ways to define productivity depending on the context. In terms of manufacturing, productivity relates to the speed at which quality work is performed....
Continue ReadingWhat Makes a Good Digital Work Instruction Software?
When Bob Dylan sang the lyrics, “the times they are a-changin’,” he probably never envisioned what the world would look like just six short decades later. The rise of digital...
Continue Reading