
Why Your Work Instructions Need Quality Checklists
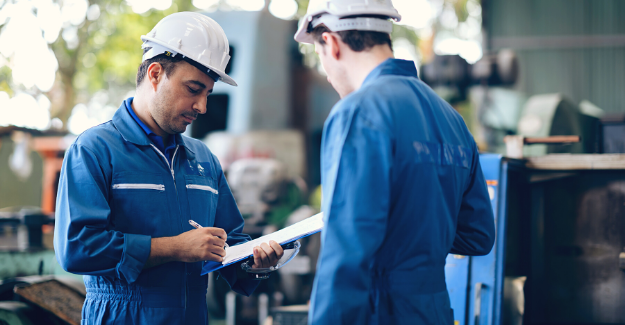
Quality checklists or inspections are a routine part of production. While they are a crucial part of quality management and control, checklists only catch errors, rather than preventing them.
Instead of reacting to mistakes, consider taking a proactive approach to quality management. This allows you to focus on preventative measures and boost employee performance.
Quality is About People
At Dozuki, we believe that quality management means supporting the people behind your business. Employees on the floor or in the field are ultimately the ones responsible for the quality of your product.
Yet 85% of quality checks are still caused by worker errors. This indicates that companies are failing at supporting employee performance and preventing quality costs.
"The greatest waste is the failure to use the abilities of people...to learn about their frustrations and the contributions they are eager to make."
W. Edwards Deming, Quality Control Leader
Why Use Quality Checklists in Work Instructions?
We’ve all been there. A routine task becomes dull, we lose interest, and perform sloppy work.It can be difficult to see the impact that our work has on a business. Rather than punishing employees for being human, quality checks should support your workforce and enable them to do their jobs better.
Adding quality checks within procedures is a simple strategy to support employee performance while keeping quality at the forefront of operations. By integrating these checks into your work instructions using digital forms, employees can check their work as they follow a procedure.
Not only does this ensure that quality checks are performed regularly, but they become a part of the process, rather than an additional task after the procedure is completed.
After working with hundreds of businesses to improve quality and standardize work on production floors, we’ve seen first-hand how these preventive quality checks can make a big impact.
Reduce Downtime with Quality Checklists
For example, a consumer goods manufacturer with a continuous assembly line had polishing machines that required routine cleaning throughout the day. The chemical used was messy, and often clogged up parts of the machine. Improper cleaning and maintenance lead to unplanned downtime and scrap waste.
Here’s where it gets interesting. Employees were required to perform a quality checklist after they completed the cleaning procedures. But it simply wasn’t having an impact.
As workers finished the tedious task, the checklist became a formality. Operators would quickly check all the boxes so they could move on to the next task. Eventually, machines would fail and management had no way to look back at the process and see what went wrong.
As they digitized their work instructions on the Dozuki platform, managers included digital forms to prevent cleaning mistakes. These digital quality check forms prompted operators to snap photos after they cleaned key components. The results were unprecedented.
Unplanned downtime plummeted, nearly falling flat. While the quality checks were designed to catch mistakes, they also signaled to operators that these steps were important. Quality was important.
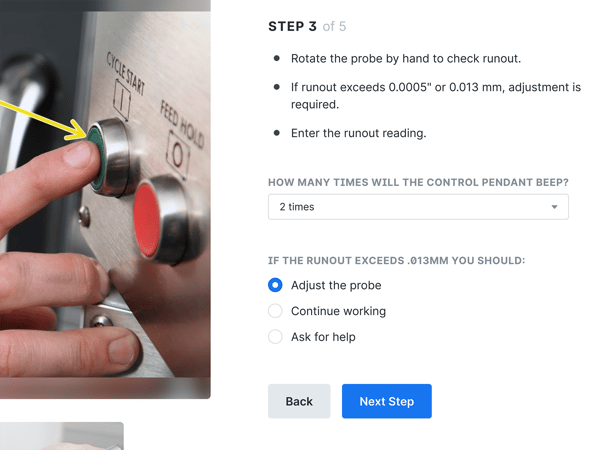
Using Dozuki for Quality Checklists
The Dozuki platform specializes in communicating best practices and standardized procedures. By leveraging our integrated digital forms in your work instructions, you can give operators the confidence to perform their work to controlled standards.
“Dozuki allowed operators to relieve some of their anxiety where they wonder 'Am I doing my job correctly?' They can now rely on the documented processes rather than tribal knowledge.”
Learning & Development Change Coach, Johnsonville
When operators submit their work, managers and supervisors can verify that the work meets quality standards via a digital signature, which can be performed remotely or in-person. This delivers the in-process quality checks in real-time, allowing mistakes to be caught before they have a chance to halt production, create rework, or scrap waste.
Digital work instructions have many benefits beyond their paper-based counterparts. Improve quality and reduce downtime with accessible, visual work instructions in Dozuki.
Related Posts
View All PostsThe Cost of Bad Work Instructions
Bad work instructions are the norm. Documentation is often created to check a box for audit or compliance purposes. But once completed, those work instructions get trapped...
Continue ReadingNavigating Processes: Standard Work vs. Work Instructions
The manufacturing industry is a professional arena with an overwhelming variety of industry terms and acronyms. We’ve tried to make a list of the most common Lean terms...
Continue ReadingElectronic Work Instructions in Industry 4.0
How do electronic work instructions factor into Industry 4.0 and your digital transformation strategy? With advancements in technology, it’s time to reevaluate how these...
Continue Reading