
Effective Ways To Reduce Employee Training Costs In Manufacturing
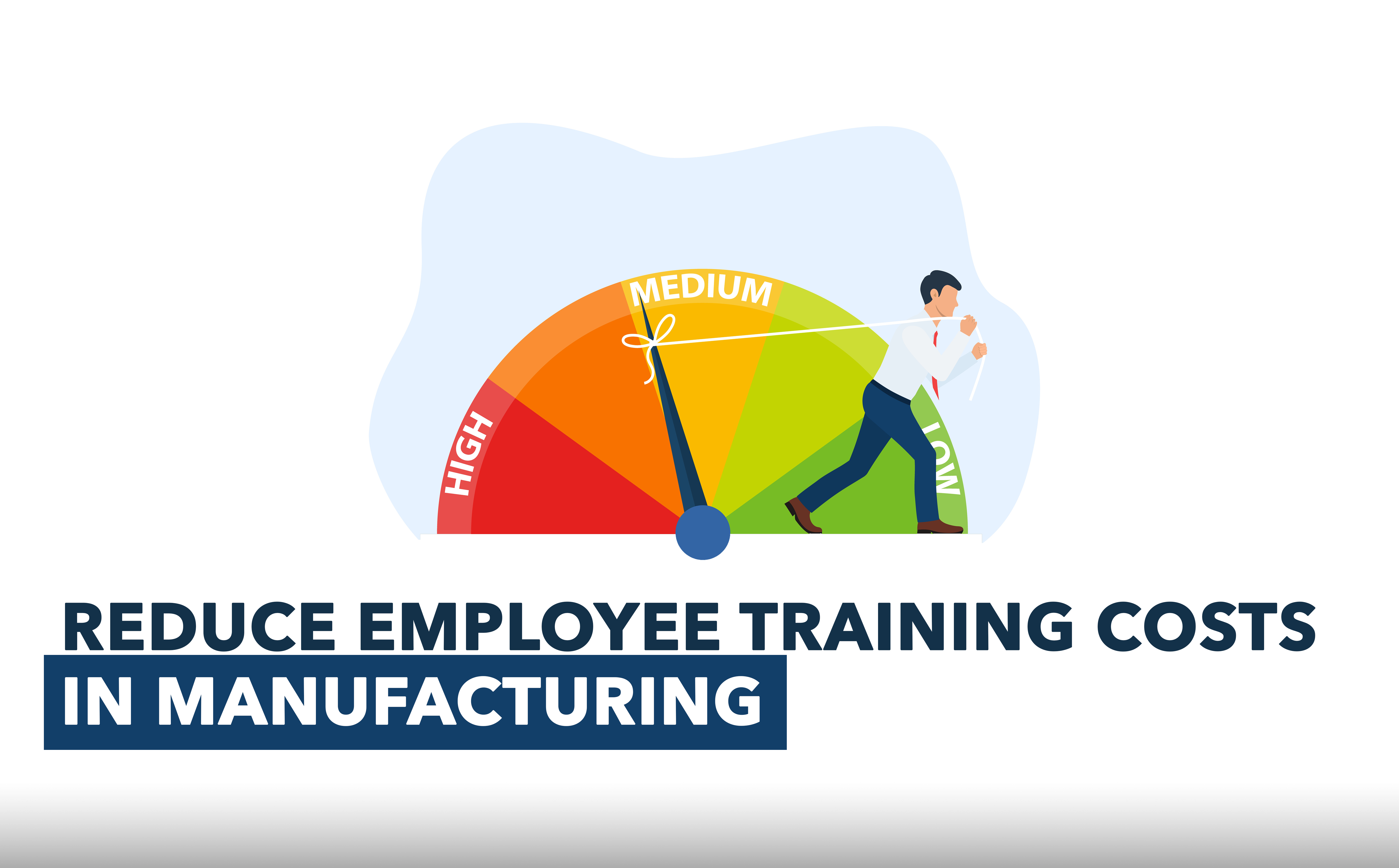
If you have a business that includes the use of employees, one of the first and most important tasks you must fund is training. This is true of all industries, but companies that operate in the manufacturing section have an increased responsibility regarding properly training their employees.
Manufacturing companies use employees to design, assemble, and produce their products. This process puts those workers at the front-end of productivity and ensuring they're trained properly reaps huge rewards.
Benefits of Training Employees
- Increased efficiency
- Increased productivity
- Higher quality products
- Greater return on investment
- Safer work environment
- Higher retention rates
- More engaged employees
- More competent employees
The problem most companies face when training their employees is the cost. Employee training programs can represent a significant percentage of company expenditures.
Between 2020 and 2021, total U.S. spending on employee training grew from $83.5 billion to $92.3 billion.
Part of this increase comes from a shortage of highly skilled workers in the market, resulting in companies having to spend more on training to fill their open jobs.
Post-pandemic, costs across all sectors have increased dramatically, and those effects tend to trickle down. Even with a decrease in costs in some areas, like in-person training, other areas have seen an increase in expenditures centered around investing in new technologies that allow for more remote learning opportunities.
Now more than ever, manufacturing companies are searching for ways to increase the efficiency of their training programs while balancing the rising costs of implementing new methods and technologies.
In this article, we will discuss the many benefits companies can gain when they focus on training, and the ways companies can reduce employee training costs in manufacturing.
The True Cost of Training Employees
So how much does it cost for companies to train their employees? The thing to remember is that time and money both represent a kind of cost. The time and effort spent eventually boils down to a dollar amount as much as the actual up-front cost that employers spend on training.
According to the 2021 Training Industry Report, the average cost to train a single employee in 2021 was $1,071, which is slightly lower than it was in 2020.
And each employee used an average of 64 training hours to get through the process, which represents an increase of almost ten hours more than the previous year.
The Covid-19 pandemic had a huge effect on training time and costs over the past two years. Many companies had to rethink their methods and turn to virtual learning to safely expedite training.
Training costs are not going to be the same for every company and will vary depending on several factors.
Figuring Training Costs
If you need to know how much to budget for training costs, there is a simple equation that can help estimate what to expect. Simply add up the total training costs and divide them by the number of employees trained. This gives you the average dollar amount spent per employee.
You can use this figure to determine if costs need to be lowered or if there’s money available to invest. And then put a focus on ways to help reduce employee training costs in manufacturing companies.
Causes of Increased Employee Training Costs
As a company grows, training costs may increase as a direct result. And some companies face an ever-changing technological landscape where ongoing training and development are a constant need in order to stay competitive.
A great example is the software industry, where employees need regular training on new products and procedures.
Once organizations can identify the things that are driving up costs, they can restructure their training methods to be the most efficient and effective as possible.
Factors That Will Affect Training Costs:
Size of the Company
Smaller companies spend more per employee on training costs, while larger organizations spend less on upfront costs, but spend more time training their new hires. This is because larger corporations can utilize group training methods and train many employees at once.
Type of Industry
This type of industry has a lot to do with training costs, because certain sectors are highly regulated or require specialized training. Jobs that require specific training or certification for potentially hazardous tasks will require extra attention.
Required Skill Sets
If the skill set of your new hires does not meet the requirements for their positions, then training will have to include courses to get them up to speed. And because there is a shortage of skilled labor at the moment, companies may find an extra expense providing that training before work can begin.
Method and Type of Training Needed
There are many methods companies can choose from when training employees, and the choice will have a significant impact on costs. On-the-job and instructor-led classroom training are more traditional methods.
Many companies are shifting to a focus on technology-based training because even though it represents an investment, they can streamline the training process and save time and money long-term.
Equipment and Materials Required
The materials and equipment that employers provide for training are a direct, upfront cost. Training courses will need to be developed, manuals or videos may need to be produced, and technology-based learning may require the use of personal devices like laptops or phones.
Time Spent on Training
Time spent training can result in a loss of productivity, especially if you utilize current employees as training leaders or coaches. Companies may choose to hire outside trainers so as not to affect the productivity of their current workforce.
There is also the possibility that current employees will need ongoing training as new processes and technologies are implemented, or recertification needs to take place.
Dozuki Can Help Companies Save Money on Training Costs
Dozuki is a workforce management application that includes tools for companies to streamline the training process. Having a centralized, digital location for training materials, and a built-in learning management system gives companies an advantage when implementing in-depth training.
Utilizing the newest technology available is the best way for companies to keep training costs low, even while organizations grow and expand.
Different Types of Training
With advances in technology, companies have access to a plethora of new and improved training methods that allow them to rethink and streamline their processes. And the great news is that many of these new technologies and techniques have proven to be more effective than traditional training methods.
Companies may need to use a combination of training methods to find the most effective and efficient way to reduce training costs in manufacturing. Recognizing the differences and advantages of each training method is the first step in understanding how to best utilize them in a training program.
On-The-Job Training
On-the-job training is a great choice for companies that hire already qualified and skilled workers to fill roles. Placing them with a mentor or allowing them to shadow a current employee allows hands-on experience performing the actual tasks they will be performing and provides the experience to get started working sooner.
On-the-job training can increase productivity during the training process. It tends to be more cost-effective than other training styles because work and training are being performed by employees at the same time.
Most other training strategies will require some hands-on learning at some point anyhow, so it may be beneficial for companies to expedite the learning process by skipping straight to practical experience. This may not be the right strategy for all scenarios but might be the best method depending on the complexity and compliance requirements of the job.
Instructor-Led Classroom Training
Traditional classroom training involves employees learning in groups that are led by an instructor. Sometimes these instructors are full-time staff members or current employees, and other times they are brought in from an outside source.
Classroom training has benefits and challenges. It can be great for big organizations that need to train many employees quickly. And it offers the opportunity for learners to have direct interaction with instructors. But it can also inhibit learning if group sizes are too big. It doesn't allow employees to self-direct their pace and requires the extra cost of paying an instructor.
If using the classroom method, be sure to keep training courses interesting and engaging so employees aren’t dozing off during courses.
Technology-Based Training
Technology-based learning may go by many names, but it all refers to learning that takes place virtually. It might be on a computer, tablet, or mobile device and can be performed either at home or at the actual workplace. The portability of this learning method means that employees can learn at their own pace, and learning can even take place on the plant floor.
Technology-based learning is the wave of the future when it comes to training employees, and many companies have implemented this style of learning at some level post-pandemic. The greatest benefit of technology-based learning is that it's very customizable and flexible enough that it can either be the primary training method or can be combined easily with other styles.
The benefits of technology-based training are many, and include:
- Removes the need for a live, in-person instructor
- Is cost-effective
- Is self-paced
- Allows learners access to materials from anywhere
- Is scalable to any number of employees
- Can incorporate a variety of learning materials on a single platform
- Automates the learning process
Tips to Reduce Costs
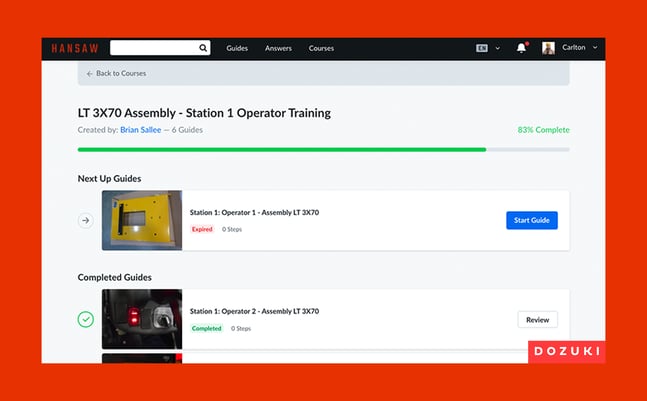
Because training employees represents an average of eleven percent of a company's operating budget, it's important to leverage the tools available to keep costs down. To reduce training costs in manufacturing, companies should take a hard look at their methods, streamline processes wherever possible, and cut unnecessary expenses.
Here are some factors companies should consider to reduce training costs:
- Focus on the most essential or necessary training courses
- Reduce or eliminate training that is unnecessary for the specific job role
- Implement group training to consolidate training costs
- Reduce the number of training sessions
- Create training materials in-house
- Include micro-training courses to keep training hours down
- Use virtual gamification to keep employees engaged and focused on coursework
- Utilize current staff as trainers instead of outsourcing instructor positions
- Transition to online or e-learning, utilizing virtual forums instead of classroom settings
- Implement a learning management system to help learners self-direct their training
Dozuki Software Can Help Reduce Training Software
Using an all-in-one training software program like Dozuki is the best way for companies to keep training costs down. Dozuki provides all the tools needed to create, implement, and organize training processes and programs for organizations of all sizes.
Dozuki is super-interactive, allowing instant embedding of information needed to monitor and update work processes instructions through the use of images and video captured from anywhere on the plant floor.
Updates and information can be easily communicated and reflected across all devices with an established approval process, allowing companies to instantly maneuver the fast-changing work environment.
Automatically assign, document, and track employee learning with Dozuki, so companies can focus on expediting onboarding processes and easily handle ongoing training opportunities. Use Dozuki to train new employees and grow the knowledge base of current employees through the practice of continuous improvement.
How to Make Employee Training More Efficient
One way to control and reduce the cost of employee training in manufacturing facilities is by making training programs more efficient. Spending money on training is an important aspect of building a successful business, but companies will get farther faster when they ensure training programs are as efficient as possible.
Here are some tips for how to improve the efficiency of training programs:
Focus on Clear Communication
Communication is one of the most important aspects of efficient training. Employees need to know what the expectations of the company are, and they need to be able to clearly understand how best to go about achieving success.
It’s also important to allow employees the opportunity to ask questions and seek guidance during the training process. Learning should be as valuable as possible, and if employees leave a training session feeling uncertain or unsure about something they won’t have confidence in their newly gained skills.
Utilize Employee Feedback
Communication goes both ways, so be sure to offer employees the opportunity to share their feedback and experiences as it relates to the training process. Gathering insights about training outcomes can help companies customize their training strategies going forward.
It can also be helpful to ask employees about their personal learning goals. Employees who feel like their employers are advocates for their success are more likely to be engaged, productive employees.
And it’s a proven fact that companies who are focused on building and developing employees through training programs are more likely to retain those employees long-term.
Accessible Training Options
In today’s job market, employees expect more from their companies and their onboarding experience, and this includes the flexibility of being able to access training from their smartphones. The percentage of people who use a mobile device versus a desktop computer is over 50% worldwide, and that number is expected to grow.
So, when companies are developing remote training options for their employees, they will gain the most benefit by ensuring that training programs are mobile-friendly.
Allowing employees, the ability to access training courses via a mobile device allows them to perform training tasks and maintain communication with training leaders anywhere, at any time. And it puts the control of their progress in their own hands, including learning at their own pace and when it's most convenient for them.
Benefits of Using Software for Training
For companies that truly want to reduce the cost of training employees in the manufacturing industry, implementing dedicated software applications is the best way to get there. While other cost-saving strategies should be considered as well, training employees with technology will reap the greatest benefits.
What is Training Software
Also known as a Learning Management System, or LMS, training software is used to easily manage and operate online learning for employees. Organizations can create custom courses, include video and engagement activities, assign and track training objectives, and provide clear routes for testing, certification, and success for learners.
So, what are the direct benefits of using software programs for training?
Low cost
Utilizing training software saves companies money by digitizing training materials instead of requiring companies to produce hard copies of individual documents. It eliminates the need for classroom learning, saving companies money associated with instructor fees, travel, and venue costs that often come with in-person training sessions.
Easy to access
The future of training is virtual, digital, and on the spot. Nothing provides that more efficiently than training software. Whether employees are learning from home, in the office, or on the factory floor, LMS systems are accessible anywhere.
Utilizing software applications also allows easy and quick access for instructors and administrators, allowing them to assign lessons, track progress, analyze results, and make changes immediately.
Requires less time to train than traditional methods
Because training software can be accessed from anywhere and at any time, employees will move through the training process faster and more efficiently.
Increases knowledge retention
Utilizing micro-learning is proven to increase knowledge retention during learning. LMS systems allow for the creation of micro-learning courses that users can navigate and complete at their own pace, improving their chances of retaining vital information.
Centralizes and digitizes training materials
Allowing employees easy access to training materials provides them with a streamlined way to access the information they need, including the ability to learn skills and gain knowledge beyond the required courses.
Automates training processes
LMS systems are a great way to save time and money during the training process because they allow for the automation of repetitive tasks. Automatically assign training courses, administer testing, and allow learners to self-enroll through a centralized interface.
Automatic triggers can also remind employees when retraining or certification courses are required.
Allows for customization
Training software is super-customizable and can meet the needs of any organization. Include gamification and interactive learning options to drive employee engagement. Use tools to build branding with logos and designs. Create custom training routes for specific job roles. Easily access progress reports and performance metrics.
The Best Software for Reducing Training Cost
Dozuki is a workforce software application for use in the manufacturing industry and is particularly well suited for cutting employee training costs in manufacturing. And it offers a wide range of features that companies can benefit from beyond training programs.
78% of manufacturers use outdated work instructions.
Not only does this lead to lowered productivity and efficiency, and results in decreased employee morale, but it is generally unsafe and irresponsible. Providing employees with the tools they need to safely and effectively perform their jobs is a responsibility of employers, and Dozuki makes it easy.
Here are just a handful of the benefits companies can gain by using Dozuki to streamline their work processes:
Access to an Intuitive Interface
A customizable and intuitive interface that allows easy access to updated work instructions, training modules, internal messaging and alerts, and automation options for tons of tasks.
Train to Changing Standards
Changes and updates to documents, instructions, and training programs can be automatically authorized with established approval processes.
Helpful Tools at Your Fingertips
Communicate on any level. Set custom groups for messaging and training activities. Integrate outside applications for a completely centralized location for training, process control, and document storage. Instantly embed pictures and video from anywhere.
Focus on Continuous Improvement
Set automatic triggers and reminders to employees when work instructions change, or recertification is required. Allow employees access to training anywhere, at any time.
Build Custom Training Content
Using documented standards and authorized experts, step-by-step training courses can be customized for specific job assignments.
Gain Real-Time Data
Operational and training data is instant and accessible, allowing companies to gain an essential oversight of performance and identify opportunities for improvement.
Highly Affordable Training Options
Utilizing an all-in-one training software program like Dozuki is the most cost-effective way to train employees. With scaling options for organizations of all sizes and complexities, customized training application software has never been this affordable.
Proper Training vs. Improper Training
As companies look for ways to reduce the cost of training employees in manufacturing, they must maintain focus on providing the most effective training possible. Lowering costs is great, but organizations need to do so in a way that doesn’t sacrifice the quality or success of their training programs.
Benefits of Proper Employee Training
Greater Retention Rates
According to research, 94% of employees will stay longer in a job role if their company invests time in their training. Considering the substantial investment employers make in sourcing and hiring potential employees, it only makes sense to keep them around as long as possible.
On top of that, companies that offer opportunities for employees to move up within an organization retain employees almost twice as long as companies that don’t. And the best way for companies to express to new employees that they are dedicated to their upward growth and continued success is through comprehensive, customizable, and successful training programs.
Companies that excel at internal mobility retain employees for an average of 5.4 years, nearly twice as long as companies that don't, where the average retention span is 2.9 years
More Productive Employees
Proper training not only ensures workers will stick around, but it helps to ensure that the employees who continue to work for a company are more efficient and productive. Training programs that focus on work, safety, and quality standards give employees the skills and knowledge they need to succeed.
When workers are properly trained, they are less likely to make mistakes or cut corners. As a result, companies gain the advantage of increased productivity, higher quality products, and happier, more satisfied customers.
Add to that the benefit of a safer work environment and companies can reap huge benefits in the form of a greater return on investment overall.
Improved Morale
Workers who are provided with the tools to perform their roles successfully and are allowed to develop their skills and careers through training programs are more engaged and have higher overall morale.
Employees want to feel valued within their companies and providing the ability for ongoing training and development is a key factor in their happiness. Engaged workers perform better, stick around longer, and are more likely to refer potential new employees to their organization.
Effects of Improper Employee Training
Higher Turnover
Research shows that over 16% of workers quit a new job within the first week, 17% within the first month, and another 14.5% within the first six months. Most of the time, these voluntary resignations are the result of improper onboarding and training for their positions.
Either the workers went into a new job with unclear expectations, felt like they weren’t properly prepared for success, or didn’t see clear opportunities for advancement and development within the organization.
A Workforce That Can’t Compete
With the ever-changing landscape of the manufacturing industry, the development of new technologies, and the implementation of more efficient and automated processes, employees need ongoing and on-the-spot training to keep up.
Companies that fail to focus on providing valuable training for new and improved processes within the industry are doing a disservice to both their workers and the success of their own companies.
Employees need the ability to develop new skills related to improvements in the industry to stay competitive, and companies need employees who can successfully operate and navigate advancing technologies.
Lowered Efficiency and Productivity
An improperly trained workforce will make more mistakes, need more direct supervision, and cost the company money as a result. When workers aren’t trained effectively, they don’t have the skills required to make good decisions on the factory floor, which could lead to an increase in injuries and accidents.
They also won’t have the skills needed to maintain quality standards, putting company revenues at risk due to lower quality products. This can even lead to a decrease in customer satisfaction if those products reach consumers.
Final Thoughts
Reducing employee training costs in manufacturing is possible when companies use the tools available to them. But to maintain a high level of success across all company metrics, it has to be done the right way.
A well-trained workforce has so many advantages for manufacturing companies. Increased productivity, higher-quality products, greater retention levels, more satisfied customers, and a better return on investment.
Taking advantage of advanced technology like automation can help companies gain the upper hand when it comes to performance, productivity, and efficiency. And the same is true when it comes to training methods.
Leveraging virtual and technology-based training is the future for business, no matter the sector. It can organize and centralize training programs into an easy-to-access format that employees can use when it's convenient for them. And it puts companies in the driver's seat when it comes to creating custom-branded applications that drive employee engagement and get proven results.
Dozuki can help companies speed up the process of revamping their training programs. Users get access to expert advice and knowledge on how to get started, and guidance along the way to make sure they get the most out of the application. It makes sense, right? Companies need cost-control measures to be successful.
With the cost of everything increasing significantly over the last year, companies can’t afford to wait. The time for better, more cost-effective employee training is now.
Related Posts
View All PostsHow to Effectively Train New Employees at Factories
In the manufacturing industry, effectively training new and current employees is the backbone of production. However, simply training new employees on the basics is not...
Continue Reading7 Best Practices in Manufacturing Training for Employees
Training employees is a surefire way to improve productivity and efficiency within manufacturing. As the company grows and expands, its employees must also grow with it,...
Continue Reading18 Books for Better Employee Training
Books are a great way to learn new techniques to train and connect with your employees. Topics can range from practical business practices, to more subjective insights into...
Continue Reading