
How to Effectively Train New Employees at Factories
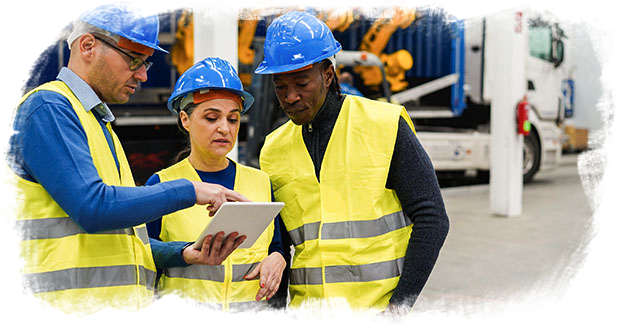
In the manufacturing industry, effectively training new and current employees is the backbone of production.
However, simply training new employees on the basics is not enough to guarantee long-term success.
Companies must focus on effectively training new employees at factories to give workers every opportunity to execute their jobs efficiently.
Not only is training valuable for companies, but it’s one of the most important factors that workers will consider during their job search and during the first few weeks of employment.
Research shows that 20% of workers in the United States abandon a new job within 45 days, but between 70%-90% will keep a job for between one and three years when the company has a structured onboarding process.
Maintaining a high employee retention rate is vital for companies because the cost of hiring and training new employees can be both steep and time-consuming. Having a solid and consistent labor force helps companies stay more productive and helps increase their ROI.
In this article, we will discuss the different ways companies can effectively train employees, the disadvantages attached to not training employees, and the general effects of having trained employees working at a factory.
Creating an Effective Training Program for Manufacturing Employees
When companies hire new employees, getting them started on the right track from the very beginning is essential to their success. And the only way to accomplish that is with an excellent and effective training program.
Here are some tips companies should consider when creating a training program for success in factories.
1. Assess
To develop a successful and effective training program, companies must first assess the needs and goals of the business and then establish a path to success for each individual goal. Use KPIs (key performance indicators) to measure quantifiable results for each goal.
2. Decide on a Style of Training
Employee training can look like a lot of different things and may include a mix of methods depending on the situation. Each goal outlined in the assessment phase should be paired with a learning format that will best achieve success. Decide what type of training will work best for each scenario.
3. Use Feedback and Results to Evaluate Success
Give employees opportunities to ask questions and use their feedback to tweak training programs going forward. You can use anonymous feedback through surveys or questionnaires to allow employees to offer feedback more freely.
4. Measure Results from Employee Training
Since the goal of each training module is to create success with a specific goal, use the KPIs and measurable outlined in the assessment step to evaluate the effectiveness of training programs. Frequently, check on employees to measure their success and understanding of the materials.
Companies should also track KPIs as they relate to training goals. Look at things like revenue, costs, productivity, quality control, and safety compliance. Were any of these metrics positively or negatively affected as a result of the training?
Putting The Training Program Together
Crafting a well-constructed program is vital for effectively training new employees at factories. Each component of a training program should be planned out in advance and should be included for a purpose.
Follow these steps to create an effective program that is tailored to your company and its specific needs.
1. Create an Outline
Having a structured outline and objectives for each learning goal helps to ensure that all pertinent information is covered. Include topics, testing, or certifications that are required for each goal. Stress information that’s the most important for success.
2. Design the Materials
Once you have the objectives laid out and have decided the best method for success for each goal, decide upon which training materials will be included at each step of the process. You can develop your own based on company needs or borrow from already existing materials.
3. The Final Product
Finalizing the training plan means looking at the path you’ve created for each objective and deciding if everything is where it should be. Is each objective covered sufficiently and in the right place? Are there gaps in the process that need to be addressed? Take a final look and make sure everything in the training process is optimized for success.
4. Implementation
Before getting employees into place to begin learning, give the training a test run to make sure everything is in place and works as it should. Test any technology before beginning to avoid delays.
On the day of training, be sure to take time to guide employees through expectations and procedures so they understand what’s expected of them.
5. Reevaluate The Training Program
Use feedback and measurable results to tweak training programs. Consider the choice of training type, the materials included, and which metrics you used to evaluate success, and then make changes where necessary.
Why is Training New Employees at Factories Important?
The benefits of training new employees in a factory setting can be defined as more than just benefits.
For companies that want to be successful, they’re more like requirements. Not only will companies reap rewards related to effective training, but employees and consumers stand to benefit as well.
Here are some of the benefits of effectively training new employees at factories:
Benefits of Effectively Training Employees - For Companies
- Increased production – Properly trained employees are more efficient and will have a higher productivity rate because they understand how to perform skills correctly.
- Lowered cost from waste and defects related to mistakes – Training leads to a reduction in costly errors that create waste, both increasing cost per unit and slowing productivity.
- Higher retention rates – Employees who receive proper training from a company are more likely to stay with a company versus employees who don’t.
- Creates uniformity related to work processes – Training programs help companies communicate standards and expectations, and ensure employees perform tasks the same way.
- Increased ROI for companies – Spending time and money on effective worker training increases revenue, lowers costs, and increases the overall return on investment for companies.
Benefits of Effectively Training Employees - For Employees
- Better adherence to safety standards – Proper training on safety standards and compliance creates a safer work environment for employees. This is a multi-faceted benefit, because not only does it decrease the occurrence of workplace accidents, but also lowers costs related to worker's compensation claims, prevents possible litigation, and saves money on lost productivity related to missed work.
- Increased knowledge of advanced technologies – The manufacturing industry is rapidly changing, and the implementation of new technologies related to production is evolving every day. Training provides employees with new skills and knowledge they need to compete and succeed in their jobs as those roles change.
- Reduced need for supervision – Having a properly trained workforce lowers the need for constant supervision. When workers have the skills and knowledge to perform their jobs correctly, they are better able to work independently.
- Increased employee satisfaction and morale – This is a big one because workers who have better training and learning opportunities feel more valued by their employers and are more likely to stay with the company rather than seek employment elsewhere.
Benefits of Effectively Training Employees - For Consumers
- Higher quality products – Employees who are properly trained in quality control processes will in turn create higher quality products, and the consumers are the ones who will reap the benefits. When companies focus on effectively training new employees at factories, customers will benefit from the knowledge workers gain in the process.
- Increased customer satisfaction – Not only will higher quality products increase customer satisfaction but companies that focus on and value their employees gain a better reputation in the market. Customers recognize and appreciate companies that spend time and resources bettering their employees.
- Better product in-stocks – When companies can be efficient and productive, consumers are less likely to be faced with out-of-stock or limited supplies related to production issues.
Best Strategies for Creating a Training Program for Employees
Creating an effective training program takes thought and planning.
There are many aspects to consider, and not all training programs are created equal. Companies face different challenges and have different needs that should be considered when planning what should be included to effectively train new employees at factories.
1. Assess the Needs of the Company
Before crafting a training program, consider what the goals are. Things to consider include specific knowledge and skills that are needed for employees to be successful in their roles. Collaborate with supervisors and leaders to better understand what the goals should be.
2. Examine Employee Knowledge Gaps
Training should be goal specific, so consider the performance and knowledge of current employees to identify areas where additional training topics would be beneficial. You can speak to employees one-on-one, utilize performance reviews, and directly observe employees at work on the factory floor to gain valuable insights into where worker knowledge might be lacking.
3. Consider Company Resources
Not all companies will have access to the same resources and budget when it comes to training. Consider the technology available to increase the efficiency of a training program. Companies should also evaluate if they have sufficient staff to conduct training and allow employees the time to complete training sessions without hampering productivity.
Also consider how much of the budget is available to be allocated to employee training, including wages and the costs associated with creating training materials.
4. Prioritize The Importance
The best way to effectively train a workforce is to prioritize knowledge and skills based on importance. This is especially important when companies have a limited budget or face time constraints related to training. If compliance and certifications are required for a specific role, be sure to prioritize those learning courses first.
5. Designate Training Coaches
Employees often make the best teachers, so utilize top performers who show desire and initiative to be training leaders. Make sure that the employees you designate have the required knowledge and skills to be effective. When specialized training is required, it may be necessary to hire an external instructor.
6. Use A SWOT Analysis
SWOT stands for Strength, Weakness, Opportunities, and Threats. Defining each of these categories can help companies understand where their training should be focused.
7. Keep Workers Engaged
Training won't be effective if employees are dozing off instead of learning. Training courses must be designed to keep workers engaged, interested, and even excited with the experience of learning. Focus on creating training programs that offer a variety of interactive materials to better engage workers with the process.
Common Employee Training Programs To Consider
When creating programs to effectively train new employees at factories, companies should consider that not all training programs are the same.
There are a variety of targeted training programs that should be utilized when considering specific goals. Here are some examples of common employee training programs to consider.
New Employee Orientation Training
Proper orientation training covers all the information employees will need to successfully perform their jobs. It includes job-specific skills training, safety procedures, and hands-on learning opportunities with machinery and equipment.
New Employee Onboarding
Onboarding refers to the knowledge employees need regarding the company itself and their specified role as an employee. It covers company culture and mission statements, information on the history and success of the company, and an overview of future goals. It also allows new employees the opportunity to truly understand expectations and gives them a chance to ask questions.
Compliance Training
Compliance training refers to specific skills or knowledge that require documented certification. Often these regulations are put forth by an outside regulatory agency and are specific to an industry or a job within that industry. Safety compliance is common in the manufacturing sector, especially when workers come in contact with heavy machinery or potentially hazardous materials.
This is one of the most important training programs and must be executed consistently and efficiently. Proper compliance training reduces a company’s risk related to injuries and accidents, helps foster a safe work environment, and prevents employers from facing potential litigation.
Product and Service Training
Employees who are tasked with production, sales, marketing, or have jobs related to any interaction with customers should be well versed in the types of products and services that companies offer. This training should be tailored to the employee's role within the company and should add value for the employees and customers alike.
Managerial and Leadership Training
Offering training for management and leadership positions has multiple benefits. It will help employees in a leadership role be more effective in their positions by offering them the knowledge and tools to properly oversee and motivate employees.
A company that offers a clear path towards advancement with leadership training is also guaranteed to increase morale and raise retention rates. Employees want to feel valued, and they will appreciate it when companies lay out specific steps that can be taken to advance their positions within the company.
Technical Training
With the ever-changing environment of the manufacturing sector, companies must pay extra attention to proper training regarding new and advanced technologies. A greater percentage of factory workers utilize automation, AI, and integrated workforce management applications as a way to enhance operations and increase productivity.
Properly training both new and current employees on how to implement and operate new technologies is vital to keeping both companies and employees competitive and adaptable.
Quality Control and Assurance Training
This type of training centers around helping employees understand the policies and procedures that lead to higher quality products and services. A company that focuses on quality control will gain the benefits of happier and more loyal customers, reduced waste, and improved profit margins
Proper quality control training also results in employees who are more motivated and engaged with the processes aimed at creating a higher quality product and providing a better value for customers.
Sales and Marketing Training
Manufacturing companies are often focused on the tasks related to production, but proper sales and marketing training is vital for the departments that deal with selling and marketing those products. Giving employees the skills and knowledge that will lead to higher sales and better customer interactions will help companies sell more products and gain customer loyalty.
Sales and marketing departments should also be trained on the specific software applications and digital tools they can use to increase lead generation and sales performance.
Soft-Skills Training
Soft skills refer to the general knowledge that employees need to succeed within a company. Things like conflict resolution, problem-solving, and effective communication are under the umbrella of soft skills.
Companies should examine which skills to focus on for specific job roles and departments. For example, the skills needed to perform well on a factory floor will differ from those needed for a leadership or sales position. But every employee can benefit from soft-skills training, both on the job and in life in general.
Team Building Workshops
Team building exercises are a common component of training programs because it fosters relationships and communication between employees. This in turn leads to increased morale and greater employee satisfaction. It also allows workers to understand that cooperation garners better results when working toward a common goal.
Diversity And Inclusion Training
In the modern age, diversity and inclusion training is an important aspect of training programs that companies cannot overlook. Companies need to embrace a culture of inclusion that lets workers know that they will be protected and supported by the company, and sets clear expectations for all employees, managers, and executives.
Employees should learn what’s acceptable and what’s not regarding their interactions with coworkers. This kind of training helps companies reduce the risk of discrimination within the workplace, lowers the rate of harassment claims by outlining actions that won’t be tolerated, and helps to protect vulnerable populations within a company.
The Disadvantages of Not Training Workers in Factories
As mentioned earlier, effectively training new employees at factories is more than beneficial, and for a company to be successful in the long-term it is necessary.
There are many possible disadvantages of working with untrained workers in factories, and a lack of focus on executing an efficient training program can cause a variety of adverse effects for a company.
Higher Employee Turnover
This is perhaps the biggest disadvantage the companies face when they fail to give proper importance to implementing an effective training program.
The combination of a labor shortage and the increasing shortage of skilled workers is already putting strain on companies concerning hiring and retention rates.
When companies fail to properly train their workforce, they are essentially flushing money down the drain. It takes time, effort, and money to source potential employees, get them through the hiring process, and train them for their roles.
So, failing to execute an efficient and effective training program is a waste of those resources if it leads to employees leaving after a few weeks.
Employees who feel like a company values their employment will stick around longer. And the best way to accomplish that is by providing them the opportunity to succeed within their role and eventually even advance their position. The ability to gain knowledge and skills is invaluable for employees, and companies should consider it a priority.
Unsafe Work Environment
Possibly even more detrimental to a company’s success regarding inefficient training is the increased risk of injuries and accidents. Improperly trained employees are more likely to disobey safety protocols or simply make errors that can lead to an unsafe work environment.
Employers have a responsibility to their workers to provide a safe working environment, and the only way to accomplish this is to ensure that employees are trained correctly and then supervised to ensure they’re upholding safety standards.
The risk of catastrophic accidents or life-altering accidents, including the possibility of loss of life, is high in the manufacturing sector. Companies must do everything in their power to make sure that employees have the training and knowledge to perform their work safely.
Lowered Production Speed
When it comes to profits, speed, productivity, and efficiency are a large part of the equation for manufacturing companies. Workers who are well trained will be able to better perform their work tasks correctly the first time and will make fewer mistakes.
Human errors on a factory floor cause a cascade of issues. Increased waste of both labor and resources results from defects and inefficient processes. Downtime from improperly operating machinery and equipment causes slows in production that cut into profits.
Unskilled workers will need more supervision and will often need to stop working to ask questions regarding skills they are lacking. Often, experienced and well-trained workers will stop their work to assist a new employee who doesn't understand a task, therefore slowing the productivity of both employees.
Lowered Customer Satisfaction and Loyalty
Employees who lack the proper training will not be able to uphold quality control standards and in turn, will produce products that have a lowered quality and value. If these issues can be addressed before products leave the factory floor, then companies are still out money resulting from correcting those mistakes.
But when products that don’t uphold a company’s quality standards make it to the consumer, then companies face a bigger problem. Customers are the ones who pay the bills, and if they’re not happy then companies won’t succeed. Companies need customers who bring them repeat business and are happy to refer others to your business as well.
More Tips for Training Employees at Factories
Companies need to use forethought when crafting programs to effectively train new employees at factories.
They should use all the tools available to them to create the very best and most efficient training programs for their employees.
Here are some tips to consider during all phases of the training process.
Employees Want to Be Trained Correctly
Being properly educated and trained is important to employees. And they deserve it. When companies fail to spend the time and effort on well-developed and executed training programs, they are cheating their employees out of their chance to succeed and cheating themselves in the process.
Pay Attention to the Onboarding Process
Good training begins before the first day and should include a proper onboarding process. Allowing a good portion of the onboarding process to occur virtually is a great way to prepare employees for success on the first day. They will be more confident and have a better understanding of what to expect.
Have a Plan in Place
A good training program is detailed and planned out in advance. Use checklists to ensure nothing vital is skipped during the training process. You can create your own or borrow a template from numerous online sources.
Train Employees for Why, Not Just How
Every step of the learning process should have a reason behind it. And employees will be more successful and motivated when they understand why they need to learn something and not just how to complete a task.
Include Training Based on Company Culture
Be sure to include information about the culture of the company, the mission statement, and the purpose of the company. Letting employees feel like they understand the values that drive the business gives them a reason to share in the success of the company.
Utilize Technology
Old-fashioned training has been replaced by a concise, virtual experience that can benefit both employees and employers. Take advantage of LMS systems to make the process of tracking, documenting, and executing training programs easier and more centralized.
Using a mobile productivity tool that integrates with an LMS system can also benefit workers, allowing them access to materials anywhere and giving them a way to communicate with managers.
Using off-the-shelf training materials allows companies to take advantage of professionally crafted resources without having to put in the work of creating them internally. And housing a content library allows employees to learn independently and explore skills that may interest them outside of their specific roles.
Track Progress and Success
Training should be more than a one or two-week process. It needs to continue for several months and should include follow-up to ensure employees have understood and are properly executing job skills and knowledge.
Strive for Continuous Learning
The one truth about the manufacturing industry is that it's always changing, and the speed at which advancements occur is only increasing with the implementation of technology. Employee training should be ongoing to keep employees up to date on changes and advancements.
Cross Train Whenever Possible
Companies who take the initiative in cross-training employees gain the benefit of increased productivity and lowered downtime. When employees can learn and execute more than one role, it allows them to step in and fill vacancies created by call-offs, vacations, and resignations.
Plus, employees have a desire to continue learning, and when given the opportunity will have increased job satisfaction.
Get Creative
The more visually interesting and personally engaging a training program is, the more likely that employees will pay attention and absorb the material. Make use of visual aids, video scenarios, and interactive games and activities to keep employees focused instead of offering a long droning block of informational text.
Final Thoughts
It's up to a company to create a program that will be successful in effectively training new employees at factories. And training is an ongoing process. It should be structured, planned out in advance, and followed up on. It should be aimed at giving employees the best possible chance at success with the company.
Workers are the backbone of most industries, but more so in the manufacturing sector.
Companies rely on employees to create high-quality products safely and efficiently. Without the proper training, skills, and knowledge, employees will not be successful. Proper training is a responsibility of every employer, both to the workers they employ and the customers they serve.
Related Posts
View All PostsEffective Ways To Reduce Employee Training Costs In Manufacturing
If you have a business that includes the use of employees, one of the first and most important tasks you must fund is training. This is true of all industries, but companies...
Continue Reading7 Best Practices in Manufacturing Training for Employees
Training employees is a surefire way to improve productivity and efficiency within manufacturing. As the company grows and expands, its employees must also grow with it,...
Continue Reading18 Books for Better Employee Training
Books are a great way to learn new techniques to train and connect with your employees. Topics can range from practical business practices, to more subjective insights into...
Continue Reading