
Hidden Waste: The Unseen Inefficiency in Shop Travelers
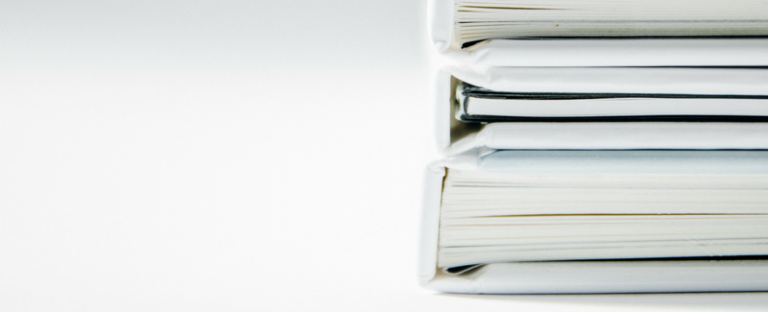
Travelers and build books are intimately related, however, with traditional methods they often function independently.
This gap between the travelers and build books creates waste.
Throughout the build, shop travelers will transfer between workstations and reference large build books at each station. Two sets of documentation that constantly reference one another should integrated efficiently. Dozuki developed a solution to consolidate these processes, as well as give management the ability track process efficiency more efficiently and accurately.
Waste Not Want Not
Shop floor travelers create an enormous burden for companies to track and maintain. Travelers typically consist of large, convoluted documents containing order details, bill of materials, checklists, work schedules, data sheets, and more—all housed in separate binders.
As products are ordered, travelers are created with purchase orders to specify and track each build. The traveler then moves to each workstation and operators reference the document to identify which work instructions to follow, which can even consist of more travelers within the build.
The Solution: Eliminating Waste
Category pages in Dozuki act as digital versions of travelers to be used for creating and managing orders more efficiently.
Instant Access
Rather than creating waste by spending time sifting through large build book binders, employees using tablets can simply scan a QR code at their workstation and the proper work instruction will instantly appear.
Build Books
Each workstation can be divided into a sub-category page, which acts like a folder, containing specifications and assembly instructions. This is the simplest digitization of the process. Dozuki also provides additional benefits, including the ability to track processes remotely and properly distributing updated processes.
Stopwatch 2.0
With Dozuki's integrated cycle timing data, the need for stopwatch experiments is gone. Companies no longer need make inaccurate output estimates based off monthly averages.
For longer builds, tracking will pause and resume as the operator takes breaks. Pausing and resuming work with paper travelers creates waste by requiring operators to shuffle through large binders before and after they start. This is particularly advantageous for complex builds, which may require several days or weeks to complete.
Automatic process Tracking
As production progresses through each workstation, tracking is automatically integrated within procedures. Within each step, workers are able to input crucial data as they proceed. Managers can also check the work order status of a particular build from outside the production floor.
The ROI of a Digital Traveler
Gain instant visibility into the status of a build with tracking dashboards accessible across all devices. Managers no longer need to be on the shop floor, searching through binders, to see status updates.
Digital travelers allow for proper version control and access permissions, forcing operators to follow the correct work instructions for production. Ensuring that workers are referencing the right information greatly helps to reduce mistakes, reduce waste, and improve workplace safety. With integrated cycle timing data, the need for stopwatch experiments is gone. Organizations can work from reliable timing data to identify inefficiencies and bottlenecks, ultimately improving production capacity.
No More Business as Usual
Paper travelers and build books have worked for a long time, but as Taiichi Ohno says, “Progress cannot be generated when we are satisfied with existing solutions.”
In order to maximize continuous improvement efforts, it’s important to take a critical look at processes that fall under the guise of “business as usual.”
More often than not, there’s room for improvement.

Related Posts
View All PostsFrom DIY Solutions To Data Driven Breakthroughs
"Quality assurance is about transforming digital acquisition into information that you can leverage."This might be our most tactical and encouraging episode yet! Mark Gobessi
Continue ReadingManufacturing & Technology Show
Dozuki will be exhibiting at the 2018 Manufacturing & Technology Show, presented by IndustryWeek. The event takes place from May 8 - 10 at the Raleigh Convention Center in...
Continue ReadingA Playbook for Tech Success in Regulated Industries
"When I wake up in the morning to empower an operator and an engineer, and they're using software from four versions ago, then I'm failing them."A former director and manager...
Continue Reading