
How Smart Factories are Impacting Productivity
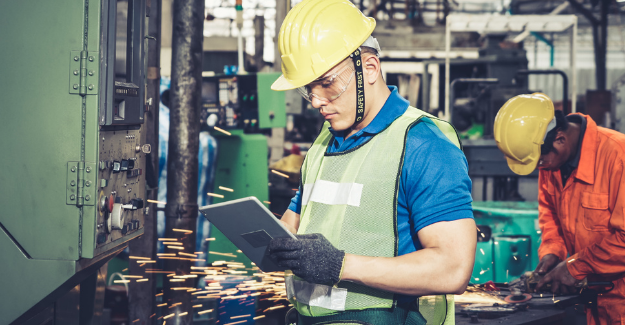
Deloitte research suggests that "smart factory" initiatives have yielded an average of 10-12% increase in labor productivity gains. Despite this success, a majority of manufacturers are still hesitant to move forward. On average, the industry only sees an increase of 0.7% in labor productivity each year. This represents a lack of investment in workforce performance and new technologies.
Early smart factory adopters reap twice as many benefits—reporting a 20% increase in labor productivity.
Companies who were quick to bet on smart factory initiatives have seen unprecedented results. It’s time for manufacturers to learn from these early adopters, or “trailblazers,” and realize operational improvements of their own.
What is a Smart Factory Initiative?
Smart factories are simply manufacturing facilities that are leveraging a variety of digital tools to accelerate operational improvements.
Reports indicate that any manufacturing business will see significant gains in:
- Manufacturing output
- Factory utilization
- And labor productivity
These initiatives are not revolutionary transformations, but incremental improvements sustained over time. It is the culmination of new technologies, processes, and people that makes smart factory initiatives successful.
Why Trailblazers Focus on People, Not Technology
Trailblazers are defined as organizations who are the first to innovate and invest in smart factory technologies. In only three years, trailblazers have reported a 20% increase in productivity and output. That’s nearly twice that of the industry average.
Trailblazers have achieved these extraordinary results by focusing by putting people at the core of their strategy. From executives and managers, to workers on the frontline—engaging all of these stakeholders will determine the success of your initiatives.
82% of manufacturers have yet to realize these same benefits as these early adopters. Learn from companies who have already tested change management strategies and made the mistakes for you.
Engage Leadership Teams Early
Successful trailblazers all shared the approach of seeking leadership support early. This ensures that your initiatives will receive the financial and strategic support needed to maintain momentum. Highly successful initiatives involve the CTO as the main leader for implementing new technology.
Trailblazers also noted involving a wide variety of stakeholders early on. This helps make well-rounded decisions that consider all aspects of your organization. Recognize that your smart factory initiative will impact many other people and departments. Use the wide range of perspectives to make decisions that will have lasting impact.
"If everyone is moving forward together, then
success takes care of itself.”
Put People First
Embrace the human aspect of launching a company initiative. Without the support of the employees, ROI will fall flat. Communicate and work with frontline employees to change their approach to work, rather than dictating new requirements.
Attempting approach work the same way, but with new technology, will not be effective long-term. Leaders should provide reasoning and support during initial adoption.
Technological advancements are only effective if your employees are supported and willing to adapt. Smart factory initiatives should first and foremost be approached with the goal of improving employee safety and enabling better performance.
"The greatest waste is the failure to use
the abilities of people...to learn about their frustrations
and the contributions they are eager to make."
Focus on Incremental Investment
Smart factory initiatives can be daunting. But contrary to popular belief, they don’t require an upheaval of your entire operations. The most successful trailblazers were able to gain momentum early by starting small and using their initial success to justify expansion.
Use small and finite proofs of concept to demonstrate success and scale. Trailblazers report having 10 or more small use cases in action. Individual projects should be small and finite; allowing leaders to minimize risk and focus on their success.
Address major pain points first. This will enable you to gain quicker adoption by employees (who will see the impact) and give smart factory budgets the credibility to expand. For example, Dozuki customers commonly begin with a single pilot plant or location, and then expand to the rest of their operations after ROI is proven.
"Dozuki's digital work instructions allowed operators to relieve some
of their anxiety where they wonder 'Am I doing my job correctly?' This
motivated members to adopt Dozuki because they can now rely on the
processes rather than tribal knowledge."
Learning & Development Change Coach, Johnsonville
Start With Employee Performance
Digital work instructions support employee performance by capturing essential knowledge and communicating best practices more effectively. At its core, Dozuki is about connecting people, processes, and technology in order to provide valuable insights and improvement opportunities.
Learn how Dozuki can support your smart factory initiatives. Schedule a consultation today.
Related Posts
View All Posts6 Shocking Stats for Manufacturing Leaders
After years of research, our show producer, Corey Brown, shares some fascinating statistics that will shock many leaders in the manufacturing industry. In this special...
Continue ReadingHow to Manage Change on the Plant Floor
Change management is a crucial part of any digital transformation or improvement efforts on the plant floor. But how do you deal with stubborn employees or older workers that...
Continue ReadingDigital Technology Trends in Manufacturing
In the past, manufacturing technology was focused on improving equipment and tools. Now, the industry is shifting its priorities towards workforce enablement. How will the...
Continue Reading