
How the Best Plant Managers Solve Production Challenges
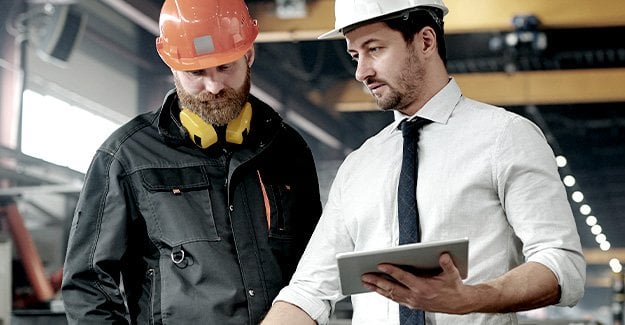
As a manufacturing plant manager, meeting production targets, reducing downtime, and filling empty roles are all ongoing goals. The best plant managers know that these goals are more like moving targets rather than a final destination. As the industry evolves at breakneck speeds, high-performing plants are adopting new tools and strategies to support worker performance and ultimately drive production.
Workforce Challenges Take Top Priority
While the COVID-19 pandemic disrupted many supply chains, it also accelerated workforce trends. Employees on the verge of retirement took the uncertainty as a sign to retire early and left vacancies. Now, recruiting new talent is even more difficult in an industry that requires in-person labor. And all this places strain on training programs that were already outdated.
But if you’re a manufacturing plant manager, underperforming isn’t an option. While some factories are crumbling under the weight of pandemic challenges, others are seeing historic improvements. High-performing plant managers can turn obstacles into opportunities by adapting with new tools and support for worker performance.
Filling Vacant Positions
A study by Deloitte and the Manufacturing Institute reported that the COVID-19 pandemic reversed a decade of job gains in manufacturing — wiping out more than 1.4 million positions.
Before managers can focus on supporting worker performance, they have to recruit enough operators and technicians to fill open positions. According to a recent report, the U.S. manufacturing industry is looking to fill nearly half a million job openings. This number will continue to climb to about 2.1 million unfilled jobs by 2030. The positions that are most difficult to fill are often essential to growth plans as well — creating a dual-threat.
This problem is industry-wide and is not going away soon. Innovative plant managers have to get creative with the resources they still have. Using new tools to cross-train and upskill your existing workforce is a cost-effective way to fill the gap without costly investments in recruiting and onboarding.
An added benefit — investing in your training program will increase retention rates too. Just by improving onboarding programs, companies will reduce turnover by 50%.
The Aging Workforce
27% of the manufacturing workforce is now over the age of 55. As older generations retire en masse, they take decades of experience and tribal knowledge along with them. But without enough available mentees to transfer this valuable information, companies are losing decades of experience and performance improvements.
57% of Baby Boomers have shared less than half of the knowledge needed to perform their job when they retire. More shocking, 21% have shared none of their knowledge — almost a quarter of a generation’s experience and insights are ready to walk out your door.
That knowledge is an asset that will take time to capture and translate into training programs. Without the successful transfer of tribal knowledge between generations, the quality and effectiveness of your operations will suffer.
Manufacturing plants that previously relied on mentoring and job-shadowing to pass down knowledge, innovative plant managers are seeking digital solutions to capture and share expertise in a fraction of the time and cost of traditional training programs.
Conveniently, the incoming workforce is thoroughly skilled in digital tools -- spending endless waking off-hours on their personal mobile devices. These “digital natives” expect all of their learning and training to take place through a screen.
Companies can see success in capturing outgoing knowledge at the intersection of outgoing experts and these incoming digital natives. Manufacturers must lean into technical solutions to capture the knowledge of retiring workers while building long-term training programs.
The Skills Shortage
Experienced plant managers know that a well-trained workforce is the driving force to reduce downtime and improve efficiency. In a recent survey of manufacturers, 90% of plant managers said the main obstacle to keeping their plant thriving was finding and training the right people.
Innovative plant managers are using a variety of strategies to improve training and reduce time-to-competency of their incoming workforce. Digital tools offer a scalable strategy for upskilling and cross-training your workers so they are ready to perform their jobs well and be adaptive to shifting demands.
In the coming years, the best plant managers will be those that lean into digital tools that empower their frontline workforce to perform their best.
As part of that digital transformation, performance will improve, training times will decrease, and career milestones will be achieved.
Where will you stack up?
Related Posts
View All PostsManage Workforce Training with Dozuki Courses
At Dozuki, we’ve made it our mission to make Standard Work an industry standard. We envision documented standards and worker knowledge continuously improving alongside one...
Continue ReadingHow Connected Worker Solutions Reduce Onboarding Time
New employee onboarding is a crucial process that directly impacts a company's productivity and bottom line. On average, the cost of onboarding a new hire amounts to ...
Continue ReadingWhat is Frontline Digital Transformation?
Manufacturing leaders agree that adopting digital technology is essential to future success.
Continue Reading