Partnering With World-Class Companies
With hundreds of customers spanning more than 38 countries, Dozuki is transforming manufacturing work from the frontline.


Connected Worker: World Class Training
"The Dozuki connected worker solution is on track to save millions of dollars on just one of our production lines this year. It's a game changer." —Plant Manager
Connected Worker: Digitizing Processes

“
Dozuki helped us fix a culture of information that was not current or standard across sites.”
“
Dozuki is amazing. The approval workflows and document control are second to none. We use it to control all of our documentation.”
“
There is no better software to document and train production operators in a standard and repeatable way. They focus on the operator experience.”
Reducing Employee Turnover Rate By 50%
Despite industry-leading low turnover, veteran workforce nearing retirement prompted proactive hiring for expansion and better onboarding. To prepare for the tsunami of oncoming retirement, proactive hiring became a top priority to shore up their workforce. To accommodate new hires, a strategy was devised to instill day one confidence and ensure their long term retention.


Enterprise Grade Digital Training
"A half percent increase in productivity gets us tens of millions of dollars of savings across facilities. —Operational Technology Engineer
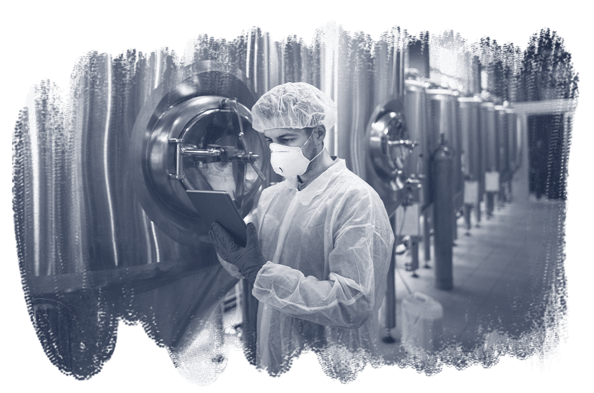
“
Easy to use. Everyone from engineering to assemblers to supply chain can benefit from Dozuki.”
“
I've been here for 20 years, and Dozuki has fundamentally changed not only how we train employees but also how we work together.”
“
Dozuki offers not only a great product but a great service. Our support team from Dozuki is phenomenal. They reply quickly, they are very knowledgeable and very polite and professional. The product, too, is great. The ability to have fantastic visuals for our team members, and for them to be able to supply feedback on those visuals has been priceless.”


Building Trust in Standards
"Dozuki allows operators to relieve some of their anxiety where they wonder 'Am I doing my job correctly?' 'Did I remember to do everything?' This motivated members to adopt Dozuki because they can now rely on the processes rather than tribal knowledge." —Taylor Harlin, Learning & Development Change Coach

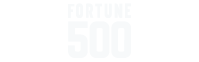
“
We were able to give a new employee with zero manufacturing experience a Dozuki work instruction. He performed a complex changeover without issue in just 90 minutes, this used to take 3 hours before Dozuki in place. The confidence it gave him was amazing.”
“
We have to spend less money on training a new employee and see better overall quality of the products we make.”
“
Dozuki is so versatile that we can place any training in the platform using multi-media methods. The best aspect of Dozuki is its ease of use.”
Breaking Barriers in Efficiency
“After comparing Dozuki to other options, it became a clear choice. The system is so intuitive and easy to kick off. The simple page design lets people catch on pretty quick ... just like navigating to a website.” —Ryan Bocook, Lead Manufacturing Engineer
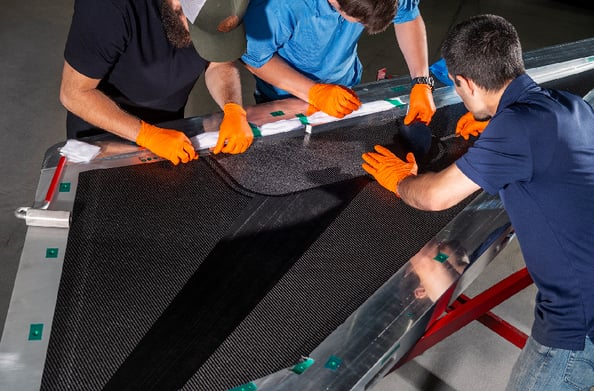
AML Oceanographic
Remotely Improving Process Efficiency
"In the same amount of time, we now keep twice as many SOPs up to date."
Go
Automation Plastics
Achieving ISO Certification
“Dozuki gives us the ability to capture knowledge of experts while utilizing the digital skills of millennials. The collaboration has been incredible.”
Go
Kettle Cuisine
Improving Food Processing Standards
“We no longer have key processes held in the heads of our seasoned experts.”
Go
International Telematics
Training Field Service Technicians
“With Dozuki, we update information, upload it, hit publish, and boom—it’s sent to our field techs. It’s fantastic.”
Go